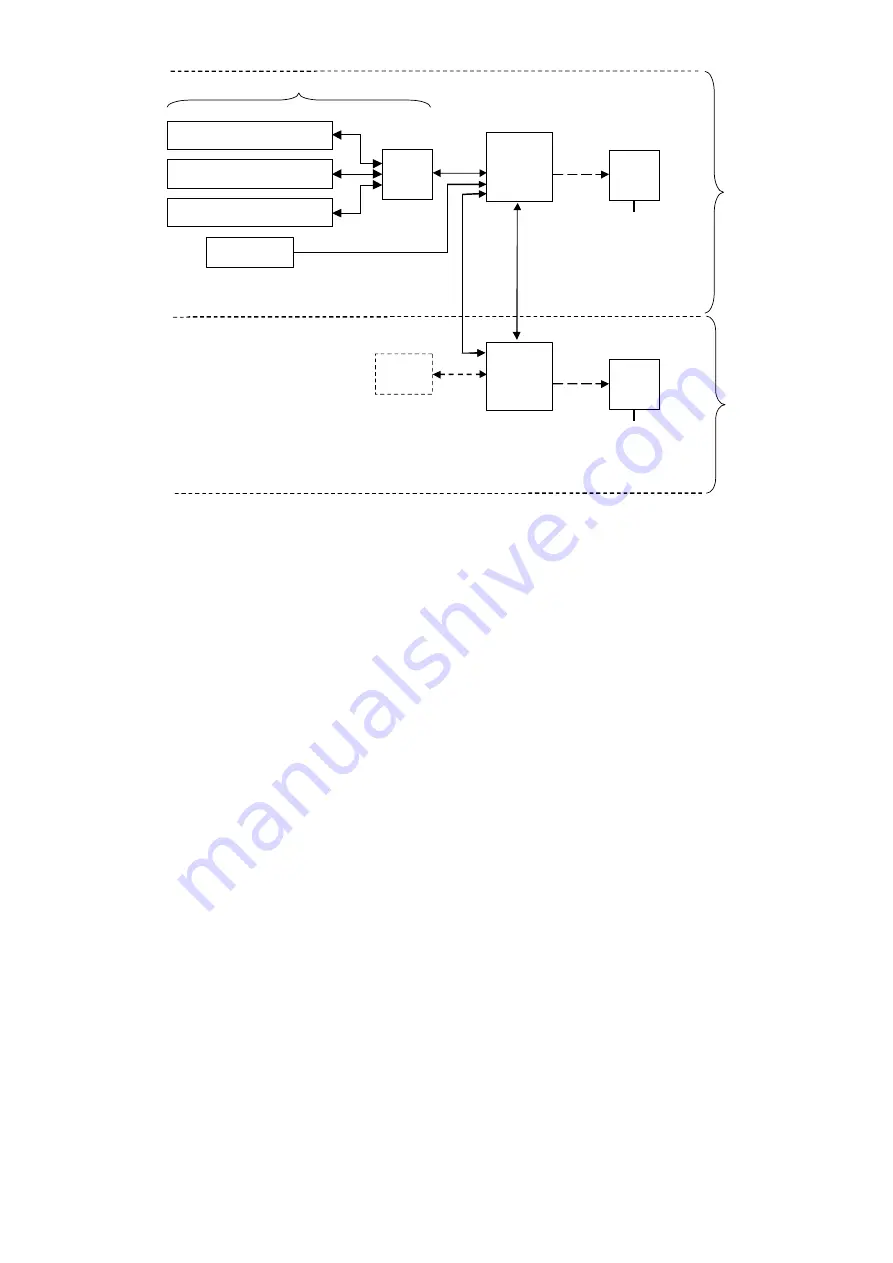
18 Hardware description
Manual Power Quality Filter PQFM
PQF
Manager
PQF
Power
Stage
CAN
Bus
Direct Interface
Modbus & PQ-Link interface
Programmable Digital I/O
3
∼
AC Out
First
unit
Second
unit
User interface
CT signals
(a)
PQF
main
controller
CAN bus (1)
PQF
Power
Stage
3
∼
AC Out
PQF
main
controller
PQF
Manager
(b)
(a)
CT signals to different units (master or slave) must be routed through daisy chain principle with
return path.
(b)
If second unit is a slave unit, it will not have a PQF-Manager. If second unit is a master unit, it will
have a PQF-Manager.
CT’s
Figure 7: Controller interface diagram of the PQFM active filter
When the filter consists of a master unit only, the customer has to:
−
Wire the CT signals (on a designated terminal).
−
Adapt the auxiliary transformer tap settings to the network voltage.
−
Connect the AC power lines and earth connection.
−
Set up the installation parameters and user’s requirements with the PQF-
Manager.
He may also want to wire the communication interface (Modbus or Ethernet) and the
programmable digital I/O (e.g. alarm contact, remote control).
When a second unit is added, it is connected to the first enclosure by means of a CAN
bus communication link (1). In addition, the CT measurements have to be supplied to
each unit, i.e. through a daisy chain link with return path. Also, the earth points of the
different units have to be interconnected.
All slave units have their own AC-connection and main contactor protection.
A PQFM active filter system consists of up to 8 units. Additional units to the first master
unit may be master or slave units. Slave units do not have a PQF-Manager.
4.5 The PQF-Manager user interface
All user interaction with the filter is channeled through the PQF-Manager.
In multi-unit filters consisting of only one master, only the master has a PQF-Manager.