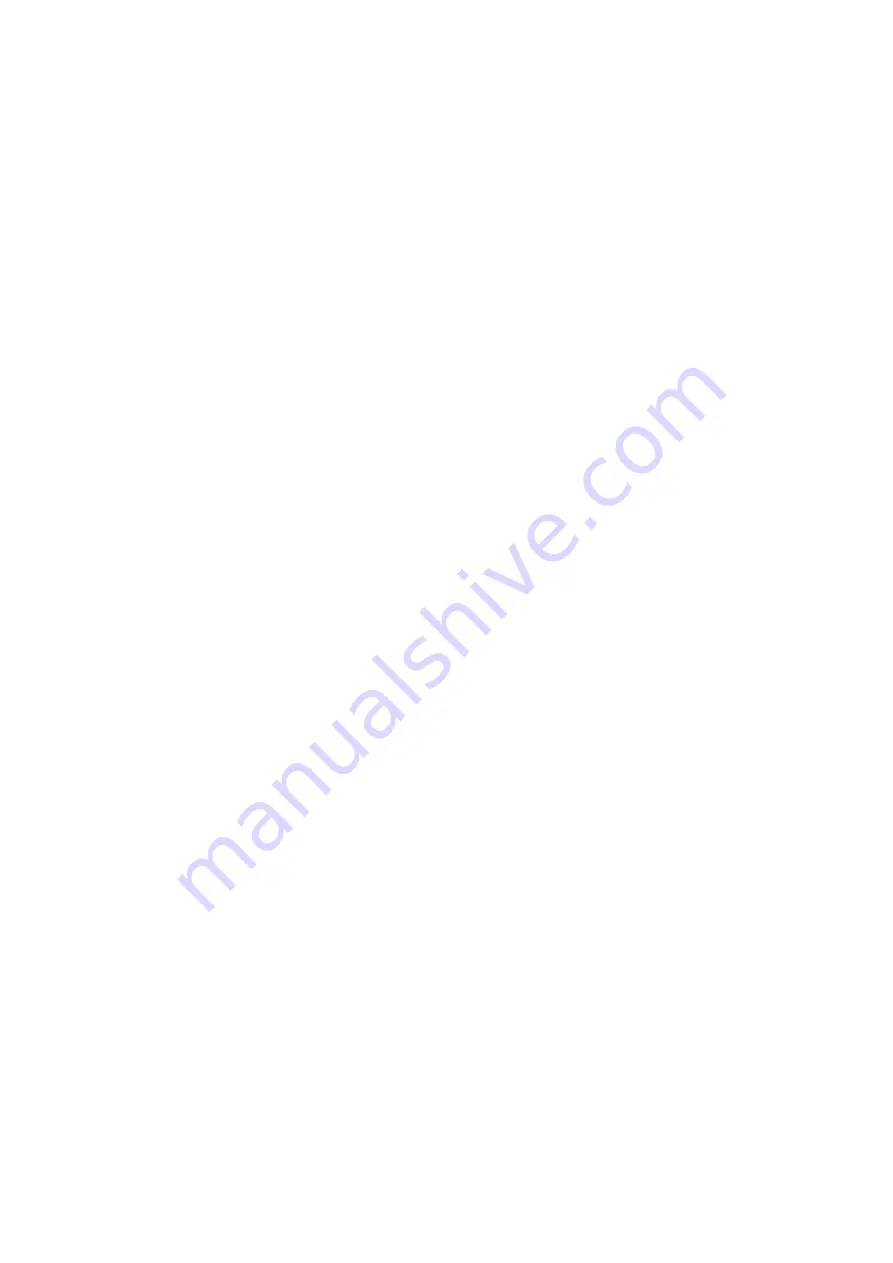
Manual Power Quality Filter PQFM
Hardware description 17
not have to be the same. Please refer to
Chapter 12
for more information on the possible
unit ratings.
In
it may be seen that each current generator consists of an IGBT-inverter bridge
(1) that is controlled using PWM-switching technology. Information from the filter
controller is sent to the IGBTs through three flat cables. At the output of the inverter a
voltage waveform is generated which contains the desired spectral components
(imposed by the filter controller) as well as high frequency noise (due to the IGBT
switching technology). Coupling impedance consisting of a reactor (3) and a high
frequency rejection filter (4) ensures that the useful voltage components are converted
into a useful current while the high frequency noise is absorbed. The IGBT-inverter is
equipped with DC capacitors that act as energy storage reservoirs (2).
In active filters containing more than one power unit the control information between
different units passes through a CAN control cable.
If a master-master configuration of filter is chosen, all power units incorporate a PQF-
Manager display. If a master-slave configuration of filter is chosen, only the master
enclosure contains a PQF-Manager display. All units contain a DC capacitors preloading
resistor (5) which charges the DC capacitors of the filter unit once the auxiliary fuse box
of the unit(s) is closed. This approach ensures a smooth filter start-up without excessive
inrush currents.
4.4 The PQF main controller
The PQF main controller controls the complete active filter system. Its tasks include:
−
Accepting and executing customer requests to stop and start the equipment.
−
Calculating and generating IGBT-inverter control references based on the line
current measurements and the user requirements.
−
Interface to the IGBT-inverters.
−
Measurement of system voltages and currents for control, protection and
presentation purposes.
depicts the controller interface diagram of the PQFM active filter.