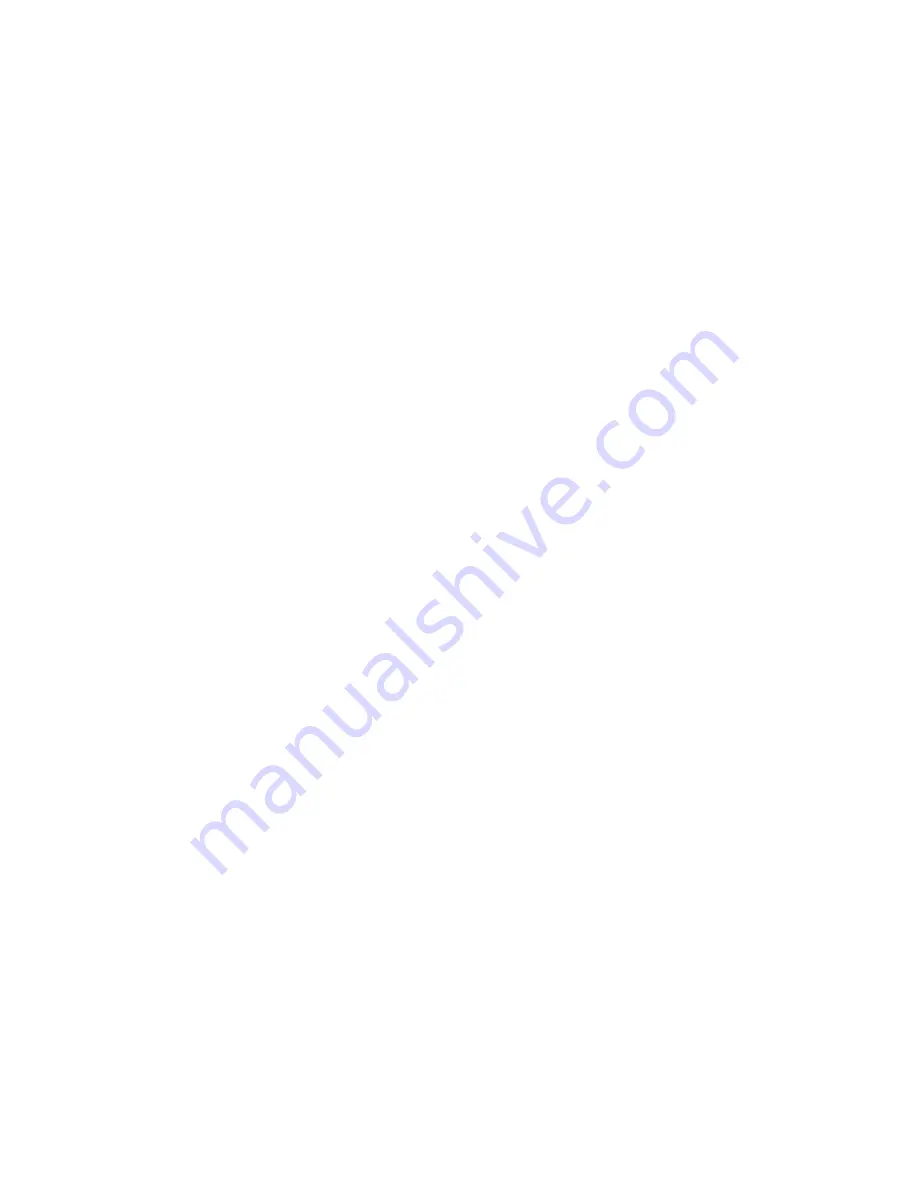
II K 6-22
Operating Instructions
n
Motor drifts at zero speed reference
Eliminate speed offset via
Tacho Offset (5.34)
• switch drive OFF
• read
Speed Actual
from panel
• set
Tacho Offset (5.34)
to this value incl. polarity
• switch drive ON and finetune
Tacho Offset (5.34)
Eliminate speed offset via
alternative parameters
(5.21…5.25)
of speed controller
• switch drive OFF
• read
Speed Actual
from panel
• set
Speed Level 1 (5.16)
to twice this value without
polarity
• set
Alt Par Sel (5.21) = Sp < Lev1
• set
Alt Speed KP (5.22) = Speed Reg KP (5.07)
• set
Alt Speed Ti (5.23) = 0.0s
• set
Alt Accel Ramp (5.24) = Accel Ramp (5.09)
• set
Alt Decel Ramp (5.25) = Decel Ramp (5.10)
• switch drive ON and finetune
Speed Level 1 (5.16)
Eliminate speed offset via additional
Fixed Speed
(5.13 / 5.14)
• switch drive OFF
• read
Speed Actual
from panel
• set
Fixed Speed 1 / 2 (5.13 / 5.14)
to this value incl.
polarity
• set
Aux Sp Ref Sel (5.26) = Fixed Sp1 / 2
• switch drive ON and finetune
Fixed Speed 1 / 2
(5.13 / 5.14)
n
Gear protection
The DCS 400 has no gear protection. However, using
the
alternative parameters
it is possible to reach a
smooth rotation change over, if the alternative param-
eter set is activated and
Alt Speed KP (5.22)
and
Alt
Speed TI (5.23)
are set to appropriate values.
n
Comments to flux optimisation
When selftuning motor
accelerates
to
50% nominal
speed
. The application must allow this. If not do not
selftune.
n
Flux adaptation failed
Check parameter
Diagnosis (7.03)
and read chapter
6.4.7 Diagnostic Messages
n
Change macro
• When changing macros all parameters set
Macro
depend
will be changed as well.
• If parameters originally set
Macro depend
have
been switched individually, they will not change.
• In case SDCS-CON-3A will be exchanged, we
recommend to set all parameters to
Factory Set-
ting
to ensure that all values from former applica-
tions will be extinguished.
n
Regenerative mode plus
fieldweakening
If a DCS 400 is intended to be used in regenrative
mode including field-weakening we recommend the
following sequence to switch the drive on:
• Switch
ON
command only at
zero speed
.
• Switch
RUN
command at any time possible
Reason:
If ON and RUN are given, to regenerate with
reduced field, it may happen, that the field current
cannot be reduced fast enough caused by the time
constant of the field winding, which results in arma-
ture overvoltage and blown fuses.
n
Using motors with nominal armature
current less than 4 A
The armature current range for DCS 400 is
20 A…1000 A. Possible parameter setting for that is
4 A…1000 A. Motors with an armature current less
than 4A are usually not supported because of arma-
ture autotuning function. To make sure that armature
autotuning works right a minimum current of 20% of
nominal converter current is necessary. In case of
smallest DCS401.0020 minimum current is 20% of
20 A =
4 A
.
That’s the reason why
not possible
to set parameter
Arm Cur Nom (1.01) less than 4 A
.
For using motors with armature current nominal
lessthan 4A it’s necessary to set parameter
Arm Cur
Max (3.04) less than 100%
!
e.g. Motor armature current nominal = 2,4 A
Set
Arm Cur Nom (1.01)
= 4 A
Set
Arm Cur Max (3.04)
= 60%
Arm Cur Max (3.04)
is related to
Arm Cur Nom (1.01)
meaning maximum armature current is 60% of motor
nominal current. Maximum current in this case is
2,4A
for normal operation.
But
armature autotuning works always with
Arm Cur
Nom (1.01)
. That means motor will be
tuned with 4A
!
Summary of Contents for DCS 400
Page 24: ...II K 3 14 Technical data ...
Page 29: ...II K 4 5 Overview of Software ...
Page 158: ...II K 6 36 Operating Instructions ...
Page 181: ...II K B 1 Appendix B Declaration of conformity ...
Page 190: ...Notices ...
Page 191: ...Notices ...