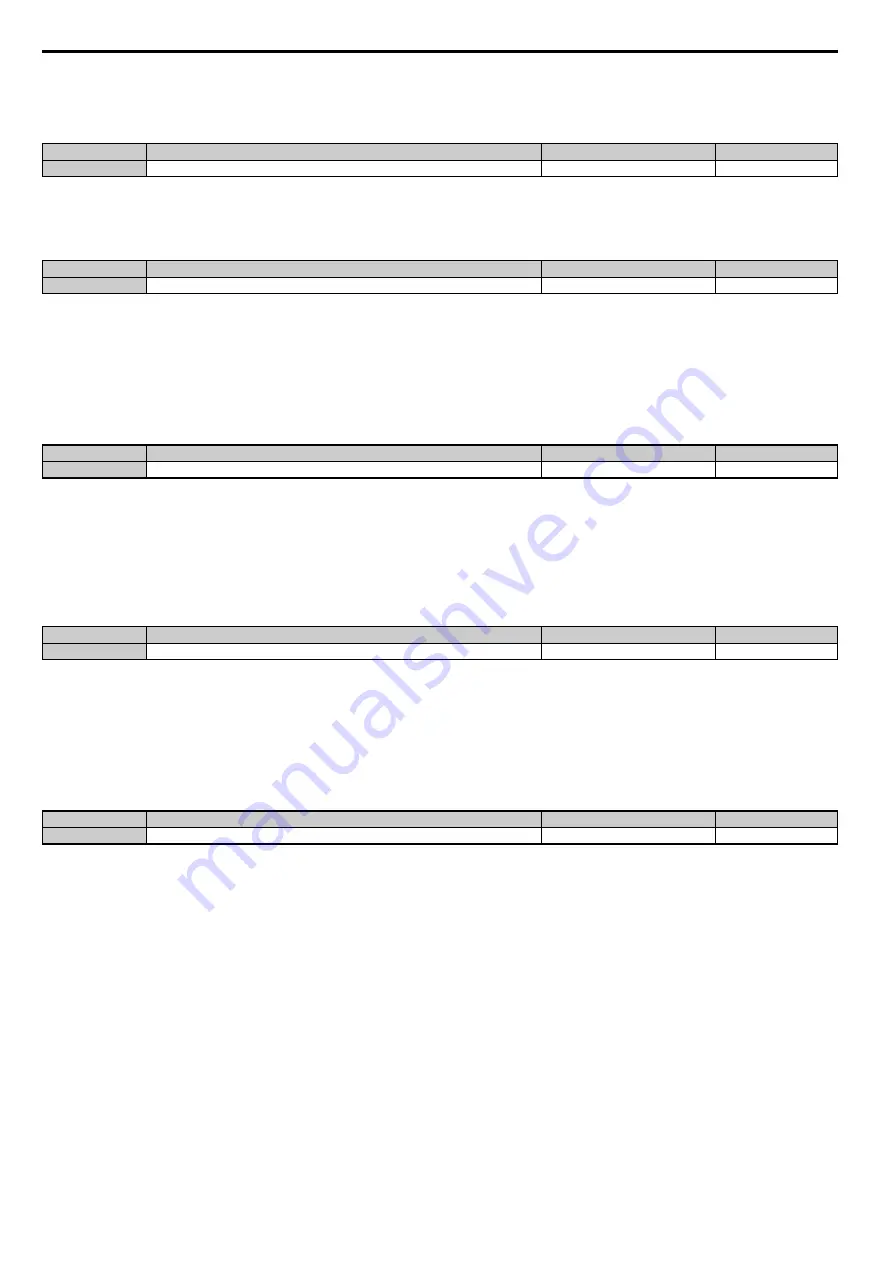
5.5 E: Motor Parameters
172
YASKAWA ELECTRIC SIEP C710616 30B YASKAWA AC Drive T1000A Technical Manual
n
E5-06: Motor d-Axis Inductance (Ld)
Sets the d-axis inductance in 0.01 mH units. This parameter is set during the Auto-Tuning process.
n
E5-07: Motor q-Axis Inductance (Lq)
Sets the q-axis inductance in 0.01 mH units. This parameter is set during the Auto-Tuning process.
n
E5-09: Motor Induction Voltage Constant 1 (Ke)
Set the induced peak voltage per phase in units of 0.1 mV/(rad/s) [electrical angle]. Set this parameter when using an
SSR1 series IPM motor with derated torque or an SST4 series IPM motor with constant torque.
When E5-01 is set to FFFF, use either E5-09 or E5-24 for setting the voltage constant. This parameter is set during
Parameter Auto-Tuning for PM motors.
Note:
Ensure that E5-24 = 0 when setting parameter E5-09. An alarm will be triggered, however, if both E5-09 and E5-24 are set 0, or
if neither parameter is set to 0. When E5-01 = FFFF, then E5-09 = 0.0.
n
E5-11 Encoder Z-Pulse Offset (
Δθ
)
Sets the offset between the rotor magnetic axis and the Z-pulse of the encoder connected. This parameter is set during
Parameter Auto-Tuning for PM motors and during Z Pulse Tuning.
n
E5-24: Motor Induction Voltage Constant 2 (Ke)
Set the induced phase-to-phase rms voltage in units of 0.1 mV/(r/min) [mechanical angle]. Set this parameter when using
an SMRA Series SPM Motor.
When E5-01 is set to FFFF, use either E5-09 or E5-24 for setting the voltage constant. This parameter is set during
Parameter Auto-Tuning for PM motors.
Note:
Ensure that E5-09 = 0 when setting parameter E5-24. An alarm will be triggered, however, if both E5-09 and E5-24 are set 0, or
if neither parameter is set to 0. When E5-01 = FFFF, then E5-09 = 0.0.
No.
Parameter Name
Setting Range
Default
E5-06 Motor
d-Axis
Inductance
0.00 to 300.00 mH
Determined by E5-01
No.
Parameter Name
Setting Range
Default
E5-07
Motor q-Axis Inductance
0.00 to 600.00 mH
Determined by E5-01
No.
Parameter Name
Setting Range
Default
E5-09
Motor Induction Voltage Constant 1
0.0 to 2000.0 mV/(rad/s)
Determined by E5-01
No.
Parameter Name
Setting Range
Default
E5-11
Encoder Z-Pulse Offset
-180.0 to 180.0 deg
0.0 deg
No.
Parameter Name
Setting Range
Default
E5-24
Motor Induction Voltage Constant 2
0.0 to 6500.0 mV/(r/min)
Determined by E5-01
Содержание T1000A
Страница 4: ...4 YASKAWA ELECTRIC SIEP C710616 30B YASKAWA AC Drive T1000A Technical Manual...
Страница 32: ...1 5 Component Names 32 YASKAWA ELECTRIC SIEP C710616 30B YASKAWA AC Drive T1000A Technical Manual...
Страница 104: ...4 10 Test Run Checklist 104 YASKAWA ELECTRIC SIEP C710616 30B YASKAWA AC Drive T1000A Technical Manual...
Страница 334: ...7 5 Drive Replacement 334 YASKAWA ELECTRIC SIEP C710616 30B YASKAWA AC Drive T1000A Technical Manual...
Страница 362: ...A 6 Drive Derating Data 362 YASKAWA ELECTRIC SIEP C710616 30B YASKAWA AC Drive T1000A Technical Manual...