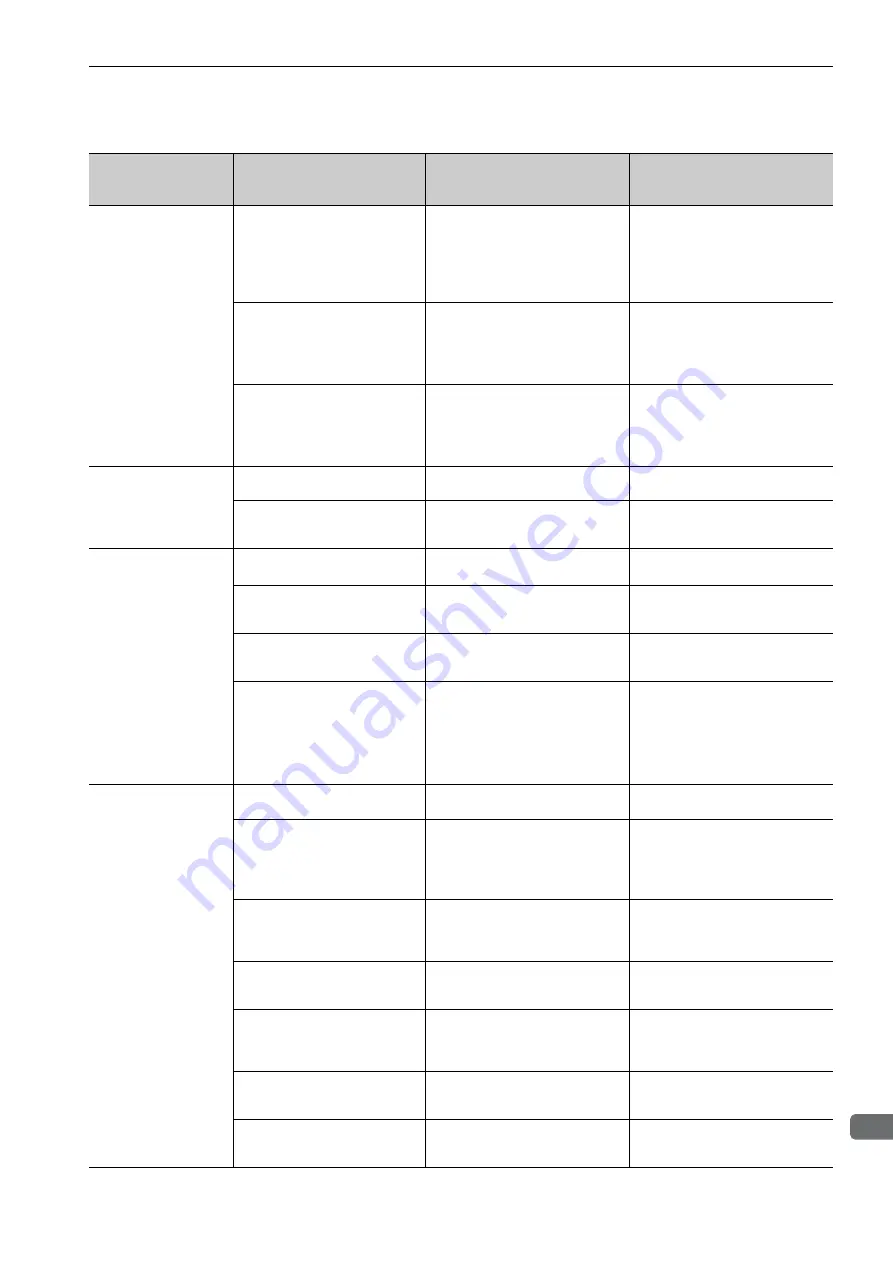
8.1 Alarm Displays
8-9
8
Trou
blesh
ooting
A.100:
Overcurrent or Heat
Sink Overheated
(An overcurrent flowed
through the IGBT or
heat sink of SERVO-
PACK overheated.)
The setting of Pn515.2 (dynamic
brake answer signal (/DBANS)
input signal mapping) does not
agree with the contacts of the
dynamic brake contactor that is
connected.
Check the setting of Pn515.2 and
the contacts of the dynamic brake
contactor.
Set Pn515.2 to agree with the con-
tacts of the dynamic brake contac-
tor.
Current flowed to the dynamic
brake resistor when power to the
servomotor was ON due to weld-
ing or other failure of the
dynamic brake contacts.
Check the contactor to see if it is
welded.
The dynamic brake contactor may
have failed. Replace the dynamic
brake contactor.
A fault occurred in the SERVO-
PACK.
−
Turn the control power supply OFF
and ON again. If the alarm still
occurs, the SERVOPACK or con-
verter may be faulty. Replace the
SERVOPACK or converter.
A.150:
Motor Winding Current
Unbalance
The motor wiring is faulty.
Check the wiring.
Make sure that the motor is cor-
rectly wired.
A fault occurred in the SERVO-
PACK or converter.
−
The SERVOPACK or converter
may be faulty. Replace the SERVO-
PACK or converter.
A.300:
Regeneration Error
An external regenerative resistor
unit is not connected.
Check the external regenerative
resistor unit connection.
Connect the external regenerative
resistor unit.
The regenerative resistor unit is
incorrectly wired, or is removed
or disconnected.
Check the regenerative resistor unit
connection.
Correctly connect the regenerative
resistor unit.
The connection of the I/O signals
(CN901) between the SERVO-
PACK and converter is faulty.
Check the connection of CN901.
Correctly connect CN901.
A fault occurred in the SERVO-
PACK or converter.
−
While the main circuit power sup-
ply is OFF, turn the control power
supply OFF and then ON again. If
the alarm still occurs, the SERVO-
PACK or converter may be faulty.
Replace the SERVOPACK or con-
verter.
A.320:
Regenerative
Overload
The power supply voltage
exceeds the specified limit.
Measure the power supply voltage. Set the power supply voltage within
the specified range.
Insufficient regenerative resis-
tance, regenerative resistor
capacity.
Or, regenerative power has been
continuously flowing back.
Check the operating condition or
the capacity using the capacity
selection Software SigmaJunma-
Size+, etc.
Change the regenerative resistance,
regenerative resistor capacity.
Reconsider the operating conditions
using the capacity selection soft-
ware SigmaJu, etc.
Regenerative power continu-
ously flowed back because nega-
tive load was continuously
applied.
Check the load applied to the servo-
motor during operation.
Reconsider the system including
servo, machine, and operating con-
ditions.
The setting of parameter Pn600 is
smaller than the regenerative
resistor's capacity.
Check the regenerative resistor unit
connection and the value of the
Pn600.
Set the Pn600 to a correct value.
The regenerative resistance is too
high.
Check the regenerative resistance.
Change the regenerative resistance
to a correct value or use an external
regenerative resistor of appropriate
capacity.
The connection of the I/O signals
(CN901) between the SERVO-
PACK and converter is faulty.
Check the connection of CN901.
Correctly connect CN901.
A fault occurred in the SERVO-
PACK or converter.
−
The SERVOPACK or converter
may be faulty. Replace the SERVO-
PACK or converter.
(cont’d)
Alarm Number:
Alarm Name
(Alarm Description)
Cause
Investigative Actions
Corrective Actions
Содержание Sigma-V JUSP-MD D A Series
Страница 21: ...xxi Index Index 1 Revision History ...