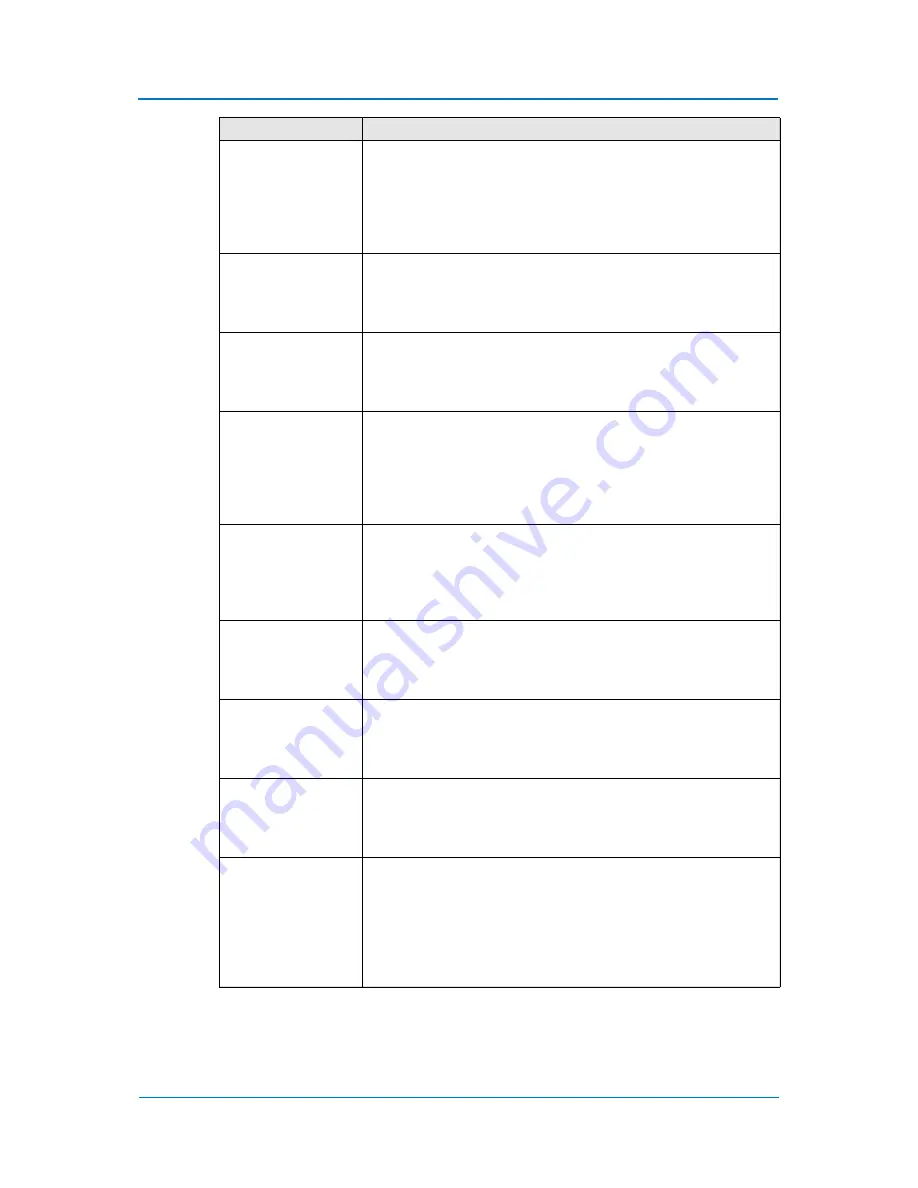
Description of Units and Circuit Boards
8
-
93
30011
SERVO IS ON
This signal signifies that the SERVO power is turned ON, internal
processing such as current position creation is complete, and the
system is able to receive the START command. This signal turns
OFF when the SERVO power supply turns OFF. It can be used for
DX200 status diagnosis for an external start.
30012
TOP OF MASTER JOB
This signal signifies that the execution position is the top of the
master job. This signal can be used to confirm that the master job
has been called
1
.
30013
ALARM/ERROR OCCURRED
This signal signifies that an alarm or an error occurred. If a major
error occurs, this signal remains ON until the main power is turned
OFF.
30014
B
ATTERY ALARM
This signal turns ON to notify that the battery requires replacing
when the voltage drops from the battery for backup memory of the
encoder. Major problems may result if memory data is lost be-
cause of an expired battery. It is recommended to avoid these
problems by using this signal as a warning signal.
30015 to30017
REMOTE/PLAY/TEACH MODE SELECTED
This signal notifies the current mode setting. These signals are
synchronized with the mode select switch in the programming
pendant. The signal corresponding to the selected mode turns
ON.
30020
IN CUBE 1
This signal turns ON when the current TCP lies inside a pre-de-
fined space (Cube 1). Use this signal to prevent interference with
other robots and positioners.
30021
IN CUBE 2
This signal turns ON when the current TCP lies inside a pre-de-
fined space (Cube 2). Use this signal to prevent interference with
other robots and positioners.
30022
WORK HOME POSITION (IN CUBE 64)
2
This signal turns ON when the current TCP lies inside the work
home position area. Use this signal to evaluate whether the robot
is in the start position.
30023
INTERMEDIATE START OK
This signal turns ON when the robot operates. It turns OFF when
the currently executed line is moved with the cursor or when edit-
ing operation is carried out after HOLD is applied during opera-
tion. Therefore, this signal can be used as a restart interlock after
a HOLD is applied. However, it also turns ON in the TEACH mode
and TEACH MODE SELECTED signal must be referred together.
1. This signal is not output during operation.
2. Der CUBE der Arbeitsausgangsstellung und der CUBE 64 sind identisch.
Logical Number
Output Name / Function