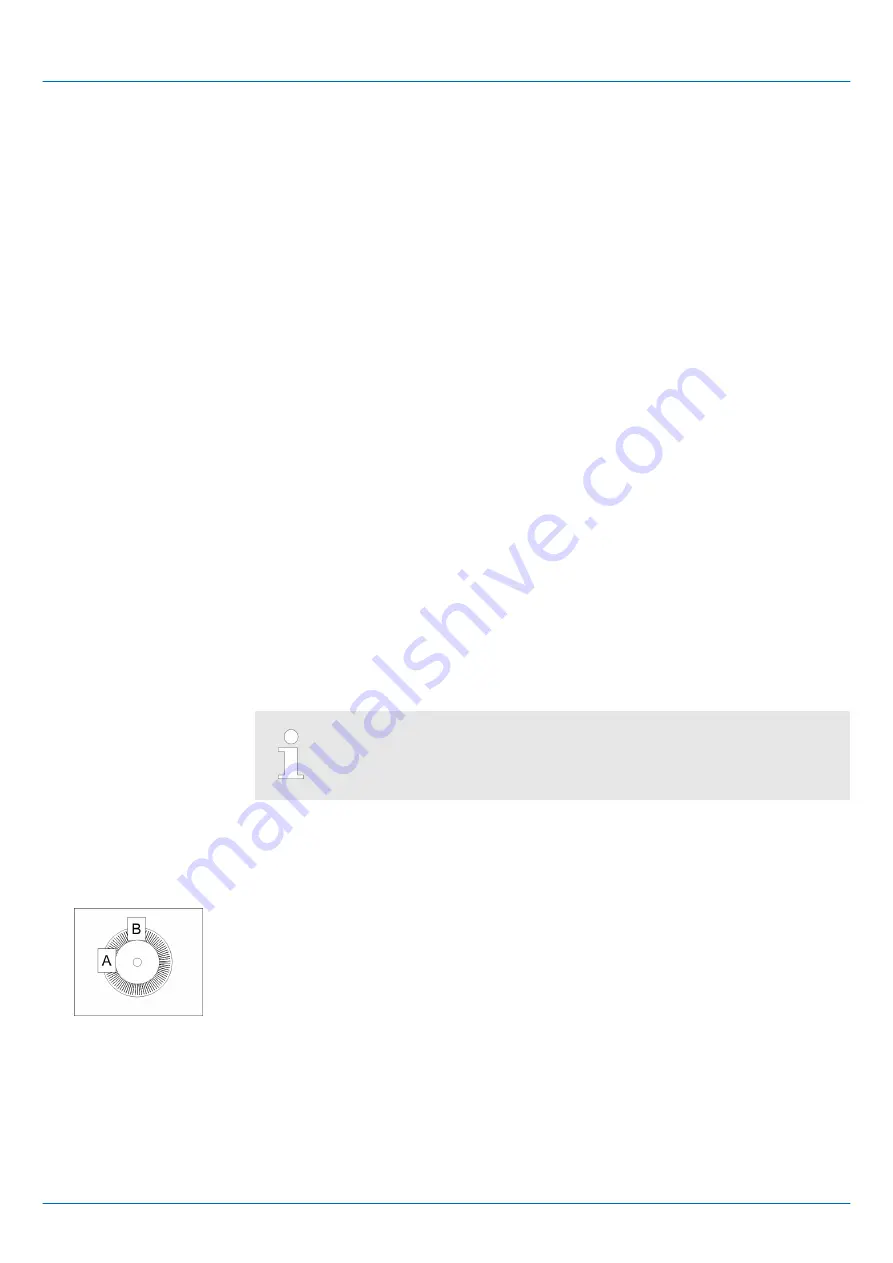
A DC motor is an engine for high-precision positioning. This consists of a fixed stator with
permanent magnets and a rotating armature. The current supply to the armature winding
happens by means of carbon brushes via the commutator as sliding contact. The indi-
vidual armature windings are connected via the commutator, which serves as a pole
changer. As soon as the armature winding is energized, a magnetic field builds up in the
armature. This results, influenced by the permanent magnets, in a rotational movement of
the armature. Due to the rotation the commutator reverses the polarity in the armature. In
this way the rotational movement is continued steadily. Controlling a DC motor by means
of pulse width modulation (PWM) is low-loss and has a high efficiency. With PWM, the
start and stop time of a square-wave signal is varied at a fixed base frequency of 32kHz.
This results in different average voltages. When selecting a motor, the following factors
must be considered:
n
Torque curve across the speed
n
Motor current across the speed
n
Winding resistance respectively motor inductance
n
The encoder respectively rotation encoder provides the controller with the position of
the drive by means of digital signals. This can accordingly be evaluated by the PLC.
n
The encoder respectively rotation encoder supply a certain number of pulses per rev-
olution.
n
The value generation is done by counting the pulses.
For the requirements of the load to be moved and the consideration of additional loads
such as bearings and gears, you can determine the necessary motor data. Here impor-
tant parameters are:
n
Mass inertia
n
Cycle times of positioning
n
Start, holding and torque at the maximum required speed
n
Acceleration and torque when passing through mechanical resonances e.g. when
using mechanical memories as spring elements, vibration buffer or long drive belts.
To avoid step losses, in accordance with the own inertia, the output
torque of the engine should be greater than the determined mechanical
torque.
4.1.3 Encoder - signal evaluation
n
Incremental encoder are sensors for detecting angular or positional changes.
n
Depending on the sensor type and the desired resolution, the scanning happens by
sliding contact, photo electrically or magnetically.
–
The scanning via
sliding contact
works in principle like a switch, which is mechan-
ically operated.
–
With the
optical scanning
a disk, which has a fine raster, is optically scanned.
–
With the magnetic scanning a pole wheel or magnetic band is scanned which has
been written with a raster by a magnetization, before.
n
The incremental encoder has two sensors
Track A
and
Track B
for scanning.
n
The sensors are arranged at an angle of 90 degrees from each other on the system
to be scanned.
Motor
Encoder
Mechanical
Signal evaluation
VIPA System SLIO
Deployment
Basics > Encoder - signal evaluation
HB300 | FM | 054-1CB00 | en | 18-06
45