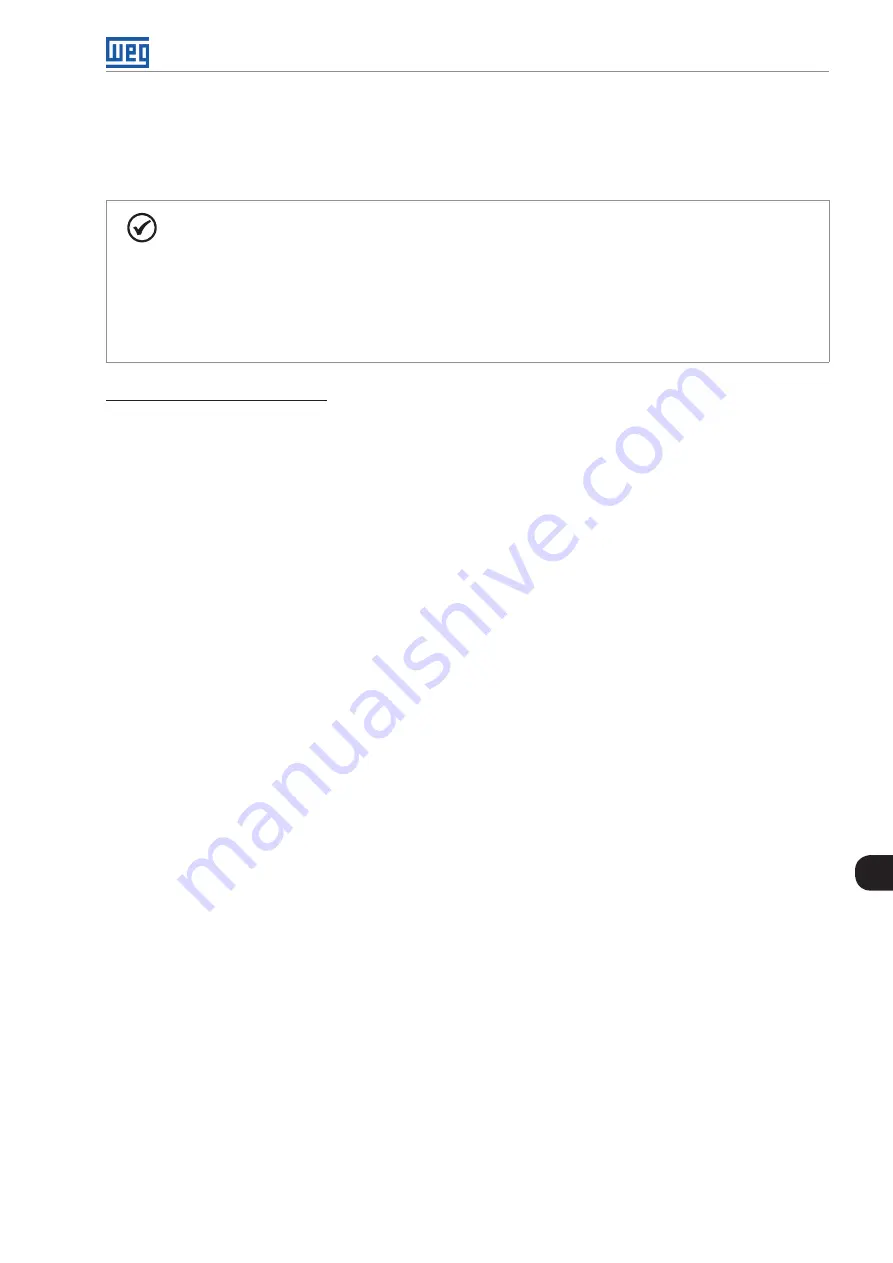
PID Controller
CFW500 | 13-3
13
13.2 START-UP
Before describing in details the parameters related to this function, below we present the directions to perform
the start-up of the PID controller.
NOTE!
For the PID function to operate properly, it is essential to check if the inverter is configured properly
to drive the motor at the desired speed. To do so, check the following settings:
Torque boosts (P0136 and P0137) and slip compensation (P0138) if in the control mode V/f (P0202 = 0).
If the self-tuning was executed if in the control mode V VW (P0202 = 5).
Acceleration and deceleration ramps (P0100 to P0103) and current limitation (P0135).
Normally, the scalar control defined in the factory default (P0204 = 5 or 6) and with P0100 = P0101 = 1.0 s
meets the requirements of most applications related to the PID controller.
Configuring the PID Controller
1. Enable PID:
For the operation of the PID Controller application, it is necessary to set the parameter P0203 ≠ 0.
2. Define the PID feedback:
The PID feedback (measurement of the process variable) is done via analog input AI1 (P0203 = 1), AI2 (P0203 = 2)
or frequency input FI (P0203 = 3).
3. Define the reading parameters of the HMI monitoring screen:
The monitoring mode of the CFW500 HMI can be configured to show the control variables of the PID controller
in the numerical form. In the example below are shown the PID feedback or process variable, PID setpoint and
motor speed.
Example:
a. Main display parameter to show the process variable:
Program P0205 in 40, which corresponds to parameter P0040 (PID Process Variable).
Program P0209 in 10 (%).
Program P0210 in 1 (wxy.z) – form of indication of PID variables).
b. Secondary display parameter to show the PID setpoint:
Program P0206 in 41, which corresponds to parameter P0041 (PID Setpoint Variable).
c. Bar parameter to show the motor speed:
Set P0207 to 2, which corresponds to parameter P0002 of the CFW500 inverter.
Program P0213 according to P0134 (if P0134 = 66.0 Hz, thus P0210 = 660).
4. Set reference (setpoint):
The setpoint is defined similarly to the speed reference as per
Section 7.2 SPEED REFERENCE on page 7-7
but instead of applying the value directly to the ramp input, it is applied to the PID input according to
.
The PID operation internal scale is defined in percentage from 0.0 to 100.0 %, as well as the PID reference
via keys in P0525 and via analog input. The other sources whose references are in another scale, such as the
Содержание CFW500 V1.8X
Страница 2: ......
Страница 4: ......
Страница 8: ...Contents...
Страница 34: ...General Information 2 4 CFW500...
Страница 38: ...About the CFW500 3 4 CFW500 3...
Страница 42: ...HMI and Basic Programming 4 4 CFW500 4...
Страница 52: ...Programming Basic Instructions 5 10 CFW500 5...
Страница 56: ...Identification of the Inverter Model and Accessories 6 4 CFW500 6...
Страница 76: ...Available Motor Control Types 8 4 CFW500 8...
Страница 84: ...V f Scalar Control 9 8 CFW500 9...
Страница 170: ...Communication 17 8 CFW500 17...