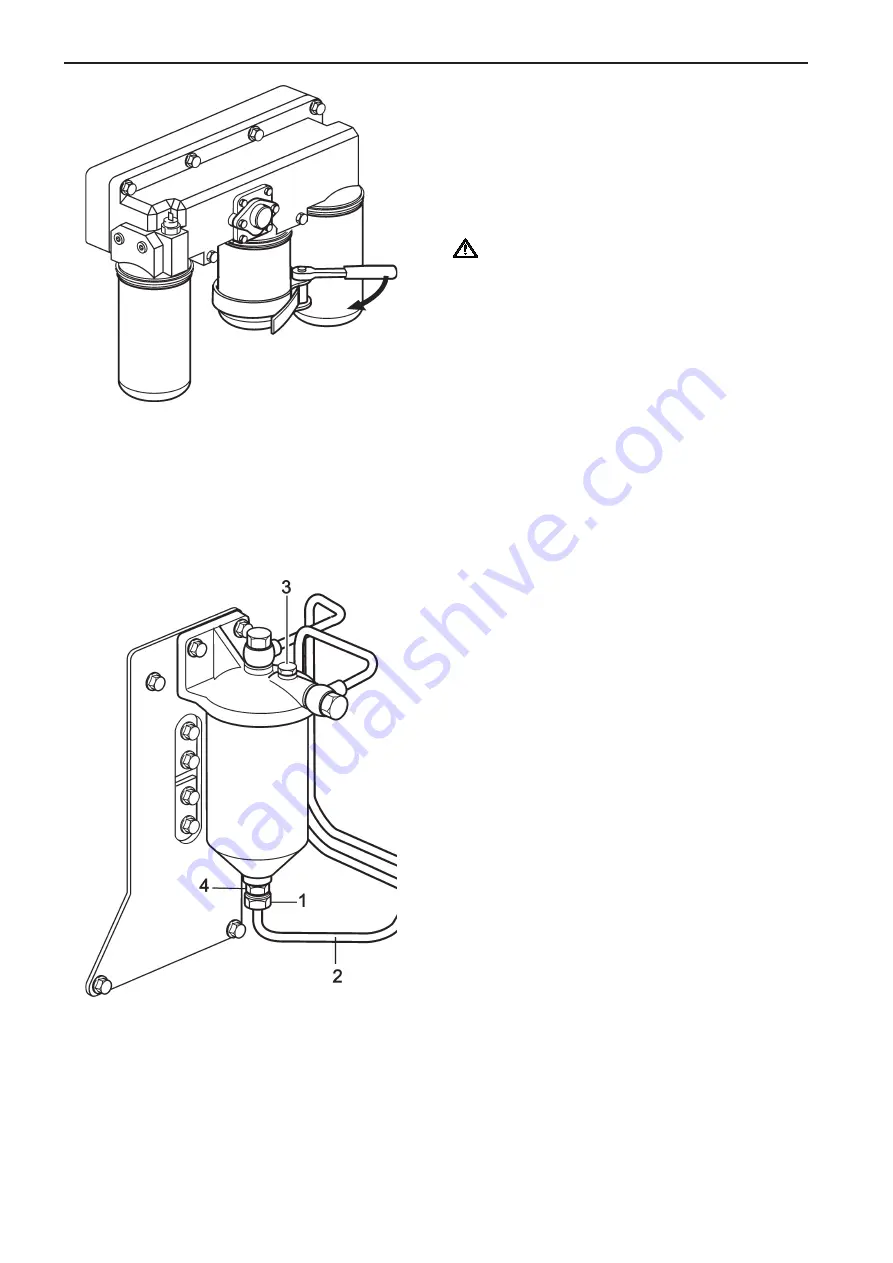
58
Maintenance: Lubrication system
Lubrication oil by-pass filter
change
1. Stop the engine
2. Unscrew the oil filter using a special filter wrench.
Note!
Place a container beneath the filter when remo-
ving to avoid oil spill.
Warning!
Hot oil can cause burns.
3. Lightly oil the new filter’s rubber gasket and check
its mating surface on the mounting.
4. Screw on the new filter by hand until the gasket is
in contact with the sealing surface. Then tighten
the filter a further approximately 3/4 of a turn
using a filter wrench.
Hydraulic governor oil filter change
1. Place a drip pan under the governor oil filter.
2. Loosen the screw holding the pipe connecting the
oil filter and the governor (1).
3. Remove the pipe (2).
4. Open the air vent plug (3) so that the rest of the
remaining oil flows into the oil drip pan.
5. Remove the center bolt (4), remove the old filter
and mount a new.
6. Remove the air vent plug and fill the filter housing
with new oil.
7. Tighten the air vent plug.
Plus d'informations sur : www.dbmoteurs.fr
Содержание D25A MS
Страница 1: ...OPERATOR SMANUAL D25A MS MT D30A MS MT Plus d informations sur www dbmoteurs fr ...
Страница 85: ...Notes Plus d informations sur www dbmoteurs fr ...
Страница 86: ...Notes Plus d informations sur www dbmoteurs fr ...
Страница 87: ...7741946 3 English 04 2002 Plus d informations sur www dbmoteurs fr ...