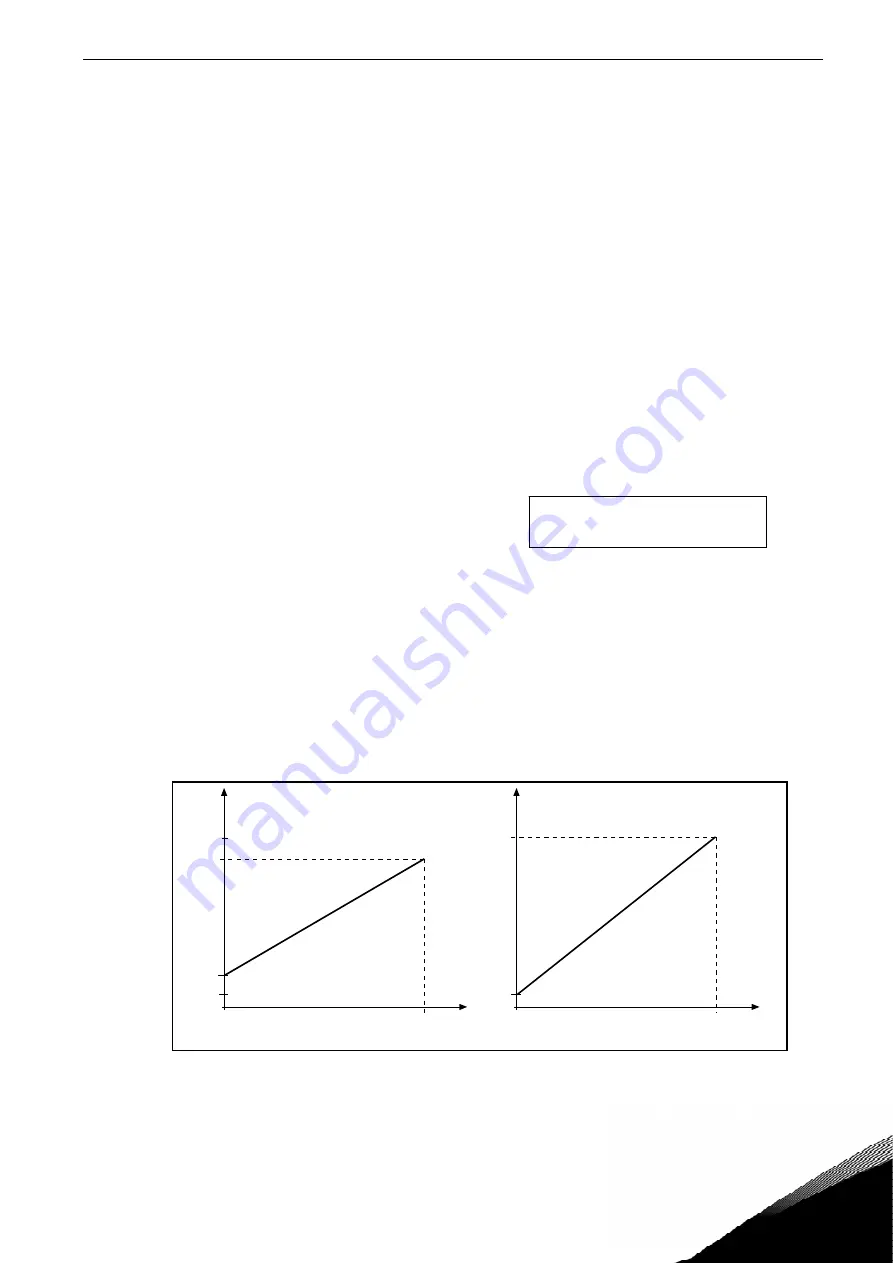
ASFIFF12 High Speed
vacon • 27
24-hour s358 (0)40 837 1150 • Email: [email protected]
301 DIN3
function
(2.2.2)
0
Not
used
1
External fault, closing contact = Fault is shown and motor is stopped when the
input is active.
2
External fault, opening contact = Fault is shown and motor is stopped when the
input is not active.
3
Run enable, contact open
= Motor start disabled and the motor is stopped
contact closed = Motor start enabled
4
Acc./Dec
contact open
= Acceleration/deceleration time 1 selected
time select. contact closed = Acceleration/deceleration time 2 selected
5
Closing contact: Force control place to I/O terminal
6
Closing contact: Force control place to keypad
7
Closing contact: Force control place to fieldbus
When the control place is forced to change the values of Start/Stop, Direction and
Reference valid in the respective control place are used (reference according to
parameters
and
Note:
The value of parameter
Keypad Control Place does not change.
When DIN3 opens the control place is selected according to parameter 3.1.
8
Reverse
contact open
= Forward
contact closed = Reverse
302
Reference offset for current input
(2.2.3)
0
No offset: 0—20mA
1
Offset 4 mA (“living zero”), provides supervision of zero level signal. In Standard
Application, the response to 4 mA reference fault can be programmed with
parameter
303
Reference scaling, minimum value
(2.2.4)
304
Reference scaling, maximum value
(2.2.5)
Setting value limits: 0
≤
P ID303
≤
P ID304
≤
. If parameter ID303 = 0 scaling is
set off. The minimum and maximum frequencies are used for scaling.
Figure 5-6. Left: Reference scaling;
Right: No scaling used (P ID303 = 0).
Can be used for reversing if
parameter
10
0
ID303
ID304
10
0
NX12K13
Output
frequency
Analogue
input [V]
Max freq. ID102
Min freq. ID101
Output
frequency
Analogue
input [V]
Max freq. ID102
Min freq. ID101