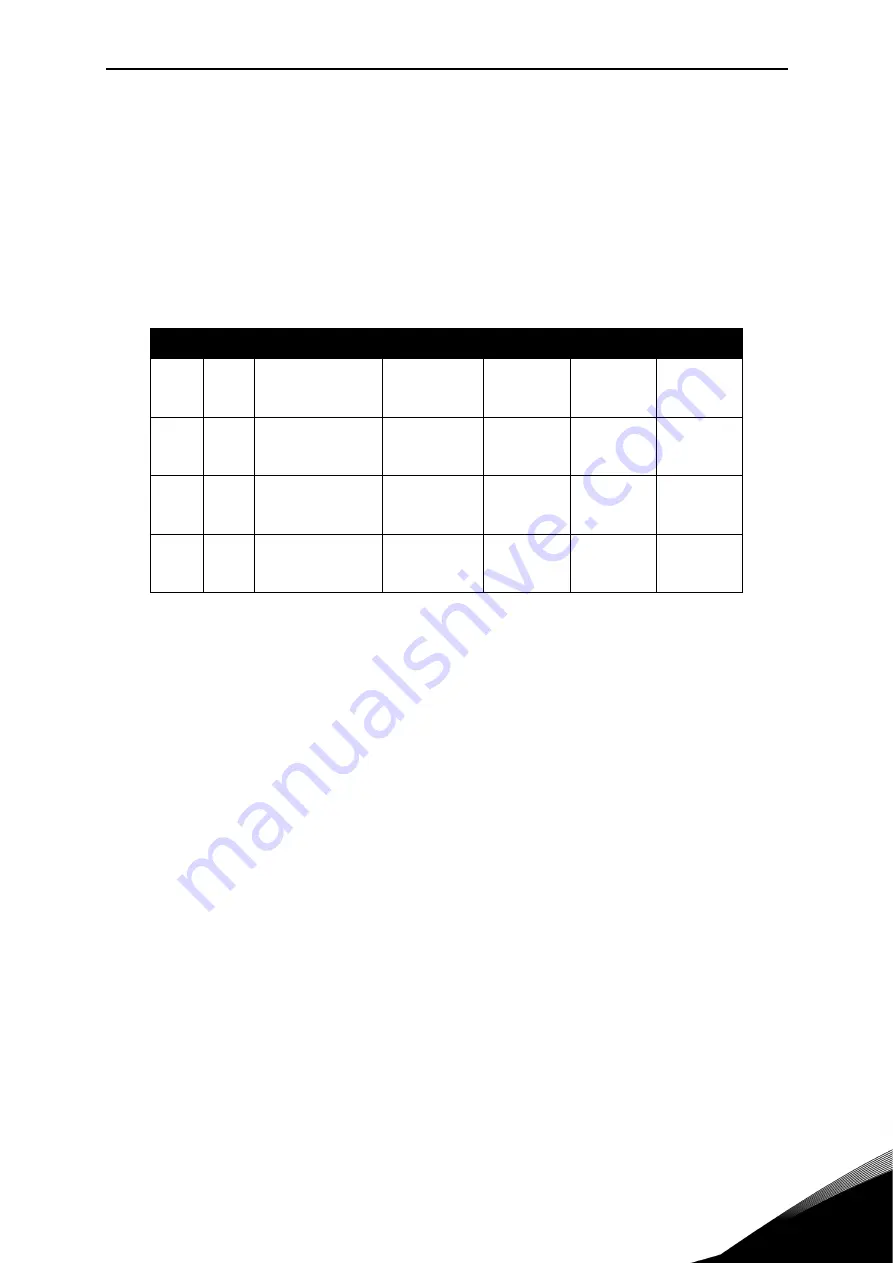
Parameter description
vacon • 56
Service support: find your nearest Vacon service center at www.vacon.com
4
P5.9
TO
P5.12 E
XPANSION
EO1, EO2, EO3, EO4
OUTPUT
CONTENT
These parameters are visible only when an expansion board with outputs is installed (to see
table below). Relays are available on boards OPT-B2, B5, B9 and BF.
Digital outputs are available on board OPTB1, if no more than 3 terminals are used as inputs,
and on OPTBF.
P5.12 is visible only when expansion board OPTBF is installed.
OPTB1
OPTB2
OPTB5
OPTB9
OPTBF
P5.9
EO1
visible if P2.24 < 4
digital out termi-
nal 5
visible
relay termi-
nals 21-22-23
visible
relay termi-
nals 22-23
visible
relay termi-
nals 7-8
visible
relay termi-
nals 22-23
P5.10
EO2
visible if P2.24 < 5
digital out termi-
nal 6
visible
relay termi-
nals 25-26
visible
relay termi-
nals 25-26
-
-
P5.11
EO3
visible if P2.24 < 6
digital out termi-
nal 7
-
visible
relay termi-
nals 28-29
-
-
P5.12
EO4
-
-
-
-
visible
digital out
terminal 3
Table 24. Digital outputs available with OPTB-boards
Содержание 20 CP/X
Страница 1: ...vacon 20 cp x ac drives Solar pump application manual ...
Страница 2: ......
Страница 4: ...vacon 1 5 Fault tracing 82 ...
Страница 6: ...1 vacon 3 Safety ...
Страница 16: ...vacon 13 Solar pump Application 2 ...
Страница 90: ......
Страница 91: ......