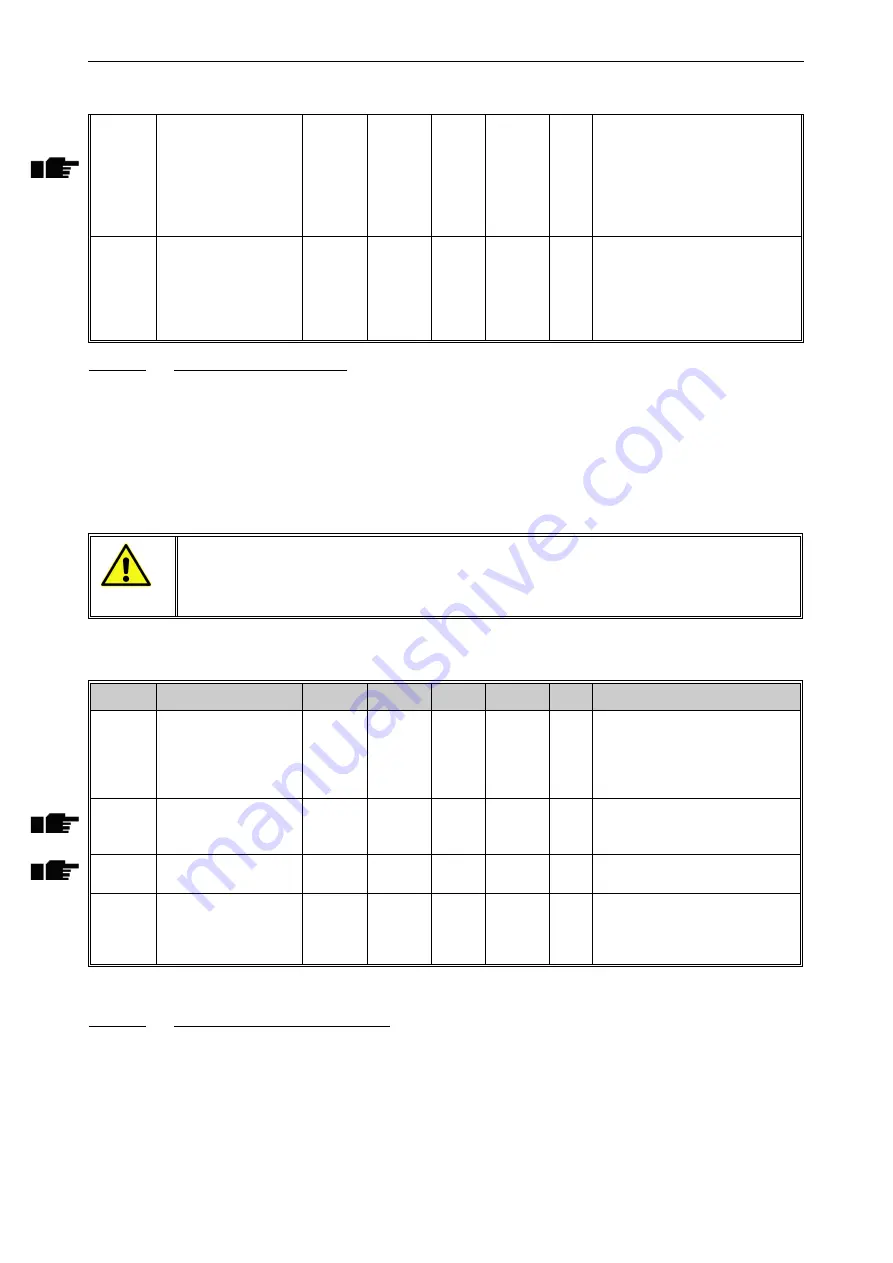
Parameters
vacon • 113
Local contacts: https://www.danfoss.com/en/contact-us/contacts-list/
7.1.10.3
Group 3.9.3: Motor Stall
The motor stall protection protects the motor from short time overload situations such as one
caused by a stalled shaft. The reaction time of the stall protection can be set shorter than that of
motor thermal protection. The stall state is defined with two parameters, P3.9.3.2 (
)
). If the current is higher than the set limit and the output frequency
is lower than the set limit the stall state is true. There is actually no real indication of the shaft ro-
tation. Stall protection is a type of overcurrent protection.
7.1.10.4
Group 3.9.4: Motor Underload
The purpose of the motor underload protection is to ensure that there is load on the motor when
the drive is running. If the motor loses its load there might be a problem in the process, e.g. a bro-
ken belt or a dry pump.
Motor underload protection can be adjusted by setting the underload curve with parameters
P3.9.4.2 (
Underload protection: Field weakening area load
) and P3.9.4.3 (
Zero frequency load
).
P3.9.2.6
0
3
2
777
The estimated temperature rise
is added to a motor ambient tem-
perature set by the parameter
P3.9.2.2 MotAmbientTemp.
0 = Disabled
2 = Last value
3 = Real time clock
P3.9.2.7
MotTempInitialAdjust
0.0
100.0
%
33.0
778
Motor thermal memory adjust
[%].
Depending on the parameter
P3.9.2.6 MotTempInitialMode, this
parameter is used as a constant
or scaling coefficient.
NOTE!
If you use long motor cables (max. 100 m) together with small drives (
≤
1.5 kW)
the motor current measured by the drive can be much higher than the actual motor
current due to capacitive currents in the motor cable. Consider this when setting up
the stall protection functions.
Table 88. Motor stall protection settings
Code
Parameter
Min
Max
Unit
Default
ID
Description
P3.9.3.1
MotorStall Flt
0
3
0
709
0 = No action
1 = Alarm
2 = Fault (Stop according to stop
mode)
3 = Fault (Stop by coasting)
P3.9.3.2
0.00
5.2
A
3.7
710
For a stall stage to occur, the cur-
rent must have exceeded this
limit.
P3.9.3.3
1.00
120.00
s
15.00
711
This is the maximum time
allowed for a stall stage.
P3.9.3.4
Stall Freq. Limit
1.00
Hz
25.00
712
For a stall state to occur, the out-
put frequency must have
remained below this limit for a
certain time.
Table 87. Motor thermal protection settings
13006.emf