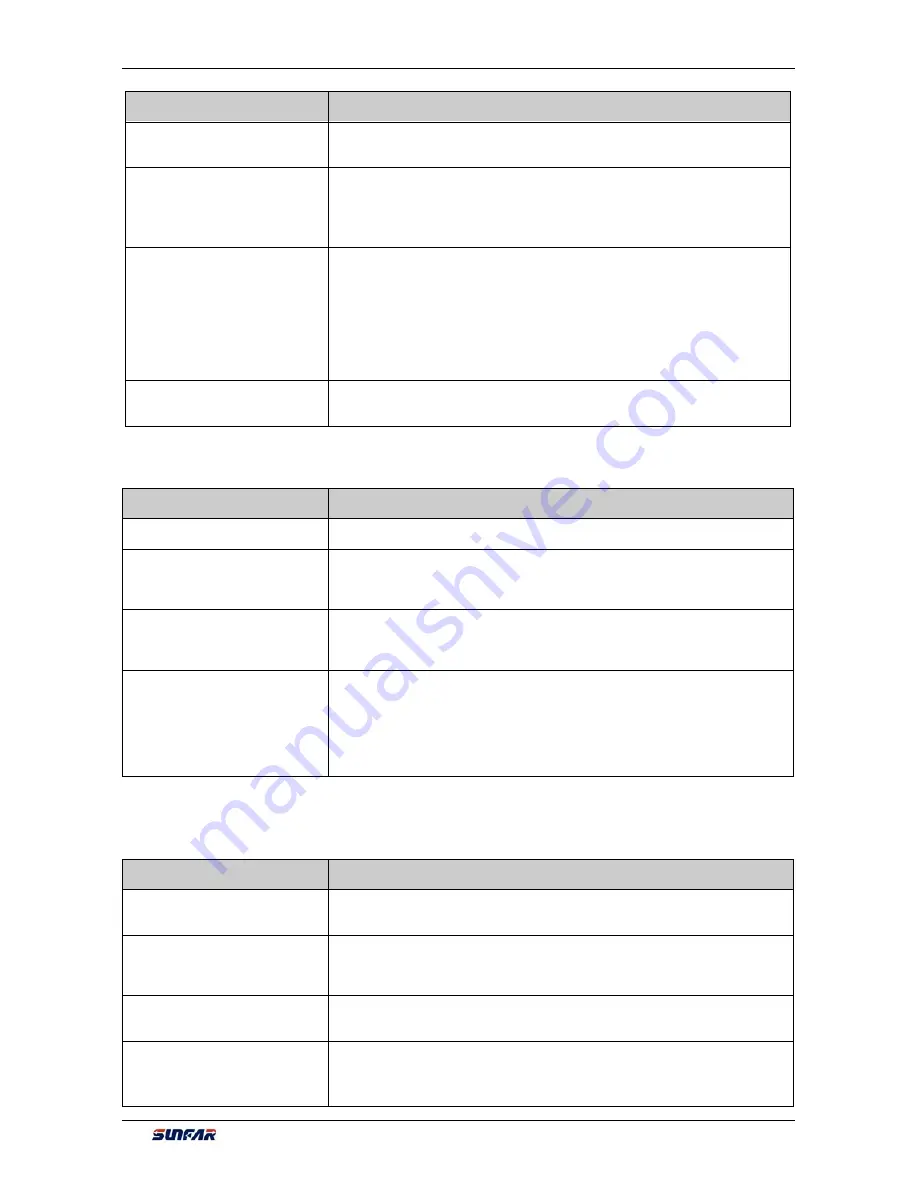
Warning, Alarm Diagnosis And Counter Measures 201
V260 Series High Performance Closed-Loop Vector Inverter User Manual
Possible causes
Solutions
The acceleration period is too
long.
Set appropriate acceleration time ([F1.0.03], [F1.0.05], [F1.0.07], [F1.0.09]).
The parameter values of motor
are set improperly
1. Confirm whether ([F2.0.00] ~ [F2.0.09]) is compatible with the parameters of
motor.
2. In vector control mode, make the motor re-self measured and get correct
internal motor parameters.
The output frequency is not rising
resulted from current limit
protection
1. According to the requirements on the site, reasonably configure the
acceleration/deceleration current limit level ([F1.4.39]), strong starting
current limit level (F1.4.40) and maintenance time ([F1.4.41]).
2. Restart after reducing torque and boosting voltage (F1.2.18) and observe
whether the output frequency is rising or not.
3. Confirm whether V/F setting ([F1.2.15], [F1.2.16], and [F1.2.17]) is
appropriate or not. Adjust V/F setting into rated value of motor.
The output frequency is not rising
resulted from torque setting limit
Confirm the torque setting limit ([F8.3.47], [F8.3.48]~[F8.3.51])sets correct
value.
3. THE DIRECTION OF ROTATION OF THE MOTOR IS OPPOSITE TO THE COMMAND
Possible causes
Solutions
Operation direction
Inspect the setting of operation direction ([F0.1.17]).
The F/R function code in
multifunctional input terminal is
wrongly selected
Inspect whether the multifunctional input terminal ([F3.0.00]~[F3.0.08])
correctly selects the function code of FWD operation command terminal, REV
operation command terminal and three wire operation control.
The action mode of external
control terminal is wrongly
selected
Inspect the action mode of external control terminal (F0.3.35).
Inspect the wiring connecting
with the motor
Exchange the connection of any two phases of U, V, and W of frequency
inverter or motor.
Inspect the connection of F/R
control terminal
Inspect the connection of multifunctional input terminal set as FWD operation
command terminal, REV operation command terminal and three wire
operation control.
4. ROTATING SPEED VARIATION AND CURRENT FLUCTUATION OCCURS IN CONSTANT
SPEED OPERATION
Possible causes
Solutions
The frequency setting varies
When the frequency is set by adopting analog input terminal, the analog input
filtering time constant can be increased. ([F4.0.06], [F4.0.07], [F4.0.08])
The carrier frequency is set
lower
Increase the carrier frequency of the frequency inverter ([F1.1.13]), change the
carrier characteristics ([F1.1.14]) and observe whether the oscillation is
disappeared.
The load type is set improperly
Set steady load operation in macro parameter ([F0.0.0]) and confirm whether
there’s vibration or not.
The motor parameters are set
inaccurately
1. Make sure the motor parameters ([F2.0.00~F2.0.09]) are set correctly or
re-self adjust the internal parameters of the motor.
2. Adjust motor speed closed loop PID parameter ([F8.2.25~F8.2.27]).