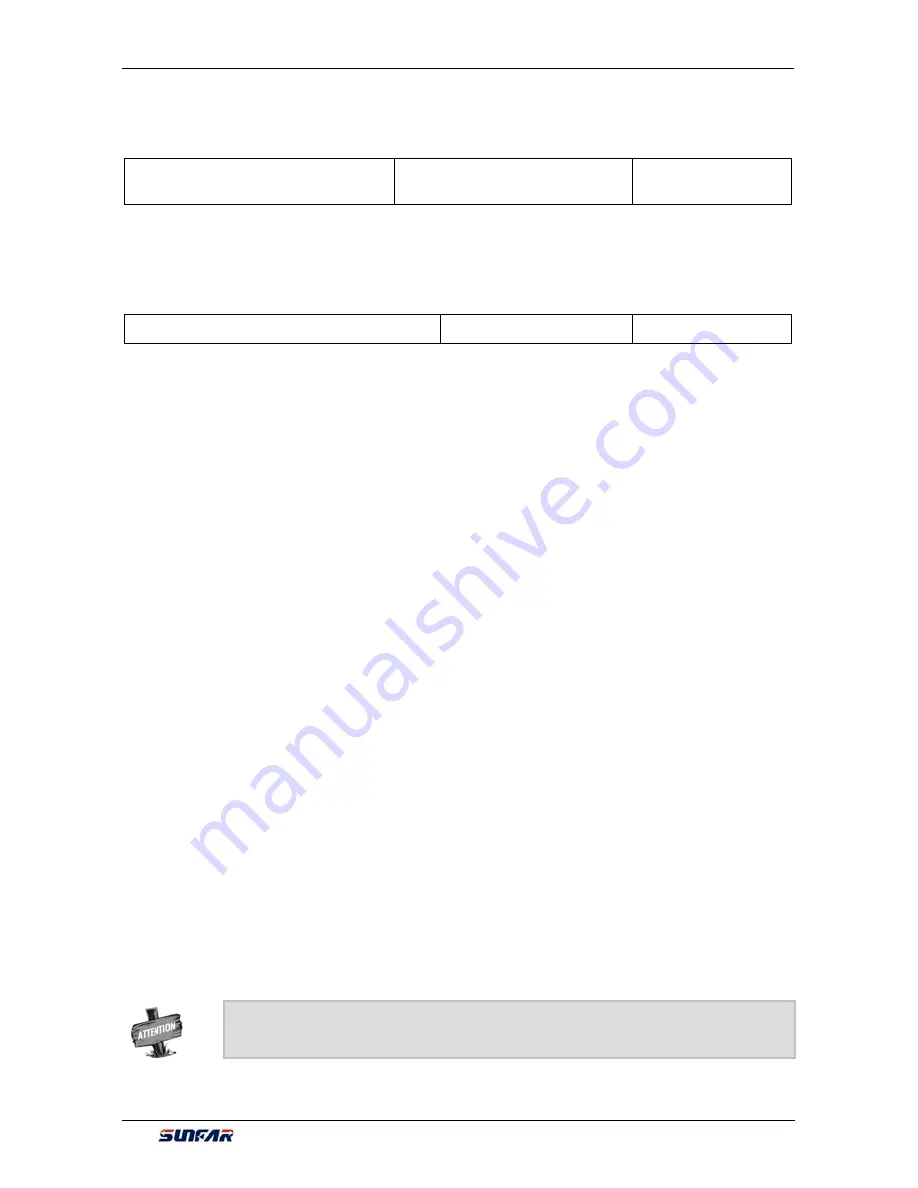
132 Description Of Specific Functions
V260 Series High Performance Closed-Loop Vector Inverter User Manual
7.12 PARAMETER MEASUREMENT AND PRE-EXCITATION (GROUP
F2.2)
F2.2.52 Excitation time for vector
mode
Setting range: 0.02~2.50Sec.
Factory default:
☆
This parameter is valid with vector operation; the pre-excitation action must be conducted prior to start of
motor, to build air gap flux to obtain enough starting torque. This excitation process shall be conducted after
action defined of parameter F0.4.42, excitation current shall be calculated automatically as selected time.
The shorter the excitation time is, the larger the current is.
F2.2.53 Motor parameter measurement
Setting range: 0, 1, 2, 3
Factory default: 0
Motor parameter measurement function must be started when vector control mode is selected (tens of
F0.0.09 is set as 0 or 1).
When this function (when F2.2.53 is set as 1~3) is operated, there will be a identification operation when the
frequency inverter is start. After parameter identification is over, F2.2.53 will automatically reset. Obtained
motor parameters will be stored in internal storage of frequency inverter, and value of parameter F2.0.05 ~
F2.0.09 will be automatically updated.
Before identification operation, please confirm that:
y
Nameplate parameter of motor (F2.0.01~F2.0.04) has been input correctly;
y
The motor is in stopped condition.
0: Closed
1: Static identification
During the process of parameter measurement, motor shall be kept in stopped condition. There is no
requirement for the connection relationship of motor shaft, but with lower measurement precision.
2: operating parameter identification
Frequency inverter will conduct static identification previously, and then automatically start operation
identification process. During operation identification process, stop order can be input to forcedly terminate
identification process. It won't be eliminated of application of identification then. When restarted, identification
process will be operated again.
Top operating frequency of operation identification will reach 80% of rated frequency of motor. Before
identification starts, please be sure to confirm the equipment safety, and it will automatically stop operating
when identification ends.
Operation identification can obtain accurate parameters, but it must be operated when the motor is complete
no-load. Otherwise, unpredictable parameter value may be obtained.
3: operating parameter identifi revolution ratio identification
Operation process under this setting is totally the same as that of 2, as well as identification result of motor
parameters. However, when there’s no installation of PG encoder on the motor shaft, the transfer ratio of
motor shaft and speed measurement shaft must be obtained to realize closed loop vector control. This
setting will not only automatically identify motor parameters, but also will measure the transfer ratio of motor
shaft: speed measurement shaft, and result can be stored automatically in parameter F8.0.17.
¾
During the process of operation identification of motor parameter, it must sure that no load
of motor during the whole process, otherwise, incorrect motor parameters will be obtained.