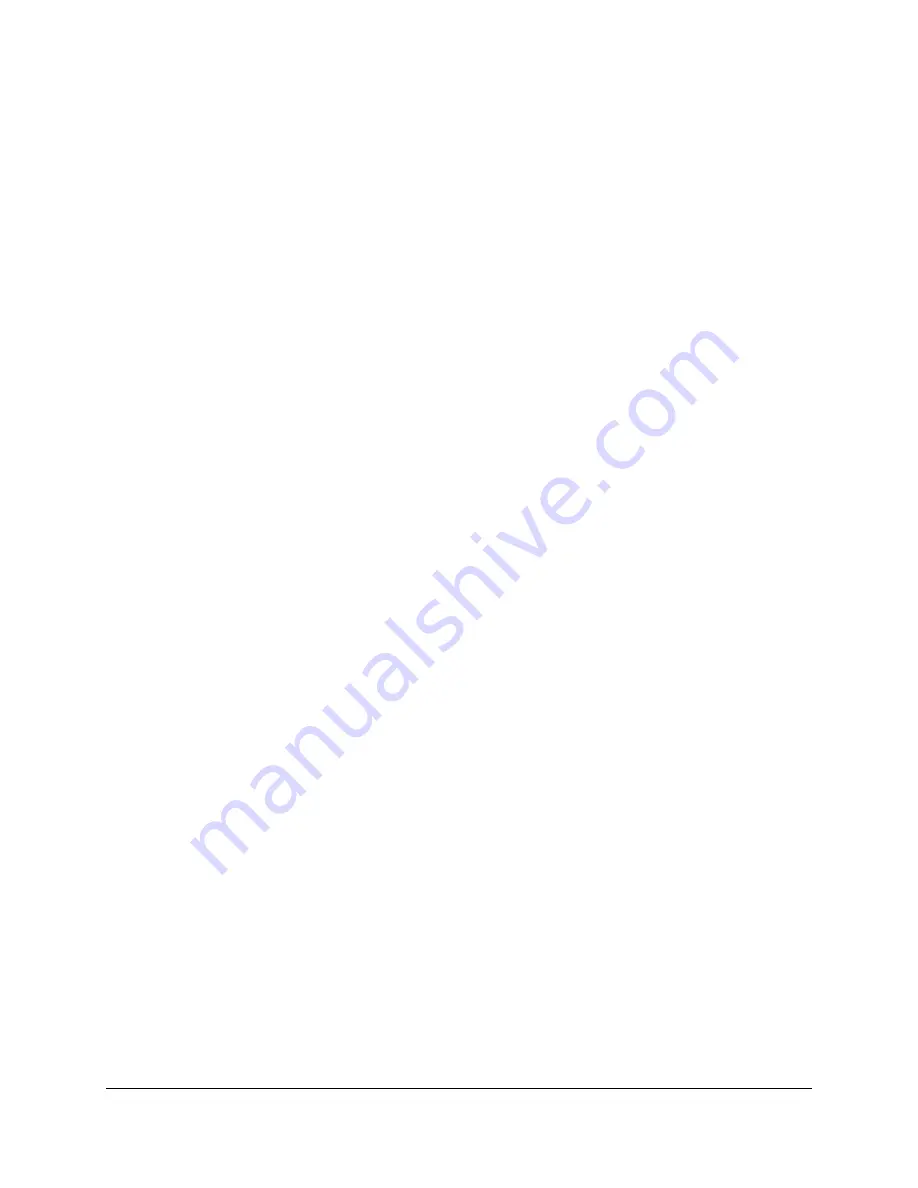
59
TRAK Machine Tools
Southwestern Industries, Inc.
TRAK TMC Mills with ProtoTRAK RMX CNC Safety, Installation, Maintenance, Service & Parts List
4.0
Automatic Tool Changer Operation and Service Codes
4.1
Tool Changer Operation
The Automatic Tool Changer or the ATC, as it is referred to throughout this manual, consists of two
major assemblies, the ATC Assembly, Upper and the ATC Assembly, Lower.
The ATC Assembly, Upper is responsible for the ATC movement toward the spindle (In) as well as the
movement away from the spindle (Out). This movement is achieved by the means of a double acting
pneumatic (air) cylinder. The ATC’s movements In and Out are
also cushioned at the end of travel by
means of hydraulic cushioning cylinder.
The ATC Assembly, Lower is responsible for the ATC indexing from tool location to tool location by means
of a Geneva mechanism, which consists of an indexing carousel, an indexing pin, a locking segment and
a geared indexing motor.
4.2
Spindle Orientation
An automatic tool change requires that many components of the TMC work in concert with one another.
These components include the ATC (Position relative to the centerline of the spindle), the spindle
(Orientation of the spindle drive dogs relative to angle of the tool holder held in the ATC), the Z-axis (tool
change height) and the Automatic Draw Bar (being in state of clamped or unclamped).
Let’s start with spindle orientation. S
pindle orientation is like any other setting regarding the ATC, it is a
critical one, as a crash would be the result of an improper setting. Spindle orientation centers the drive
dogs of the spindle for proper engagement of the CAT40 tool holder when it is held in the tool carousel of
the ATC. Service code 510 will safely walk you through this procedure. Make sure to follow the procedure
precisely.
4.3
Tool Change Height
Service code 501 will take you through the procedure for setting the tool change height. This will set the
position where the Z-axis will clamp or unclamp the tool by the automatic draw bar. Like the spindle
orientation, this setting is also critical.
During this procedure you will hear the “air through the spindle”, this is not a nuisance,
but rather a
valuable tool for this procedure. As you near the proper tool change height while performing service code
501, you will hear the sound of the air slowly being blocked off, simply creep down at .010” jog feed rate
until the sound of the air just disappears, then back it off one click and the slight sound of air will once
again be heard. That is the proper tool change height.
It should be noted, that the tool clamping mechanism will give the CAT40 tool holder a slight bump at
“Unclamp”, to disl
odge the tool holder from the spindle. Likewise, it will give the tool holder a slight tug
at “Clamp”. This action is both normal and proper.
Any improper setting of the tool change height would result in unnecessary stresses on the gripper
assemblies and the tool carousel.