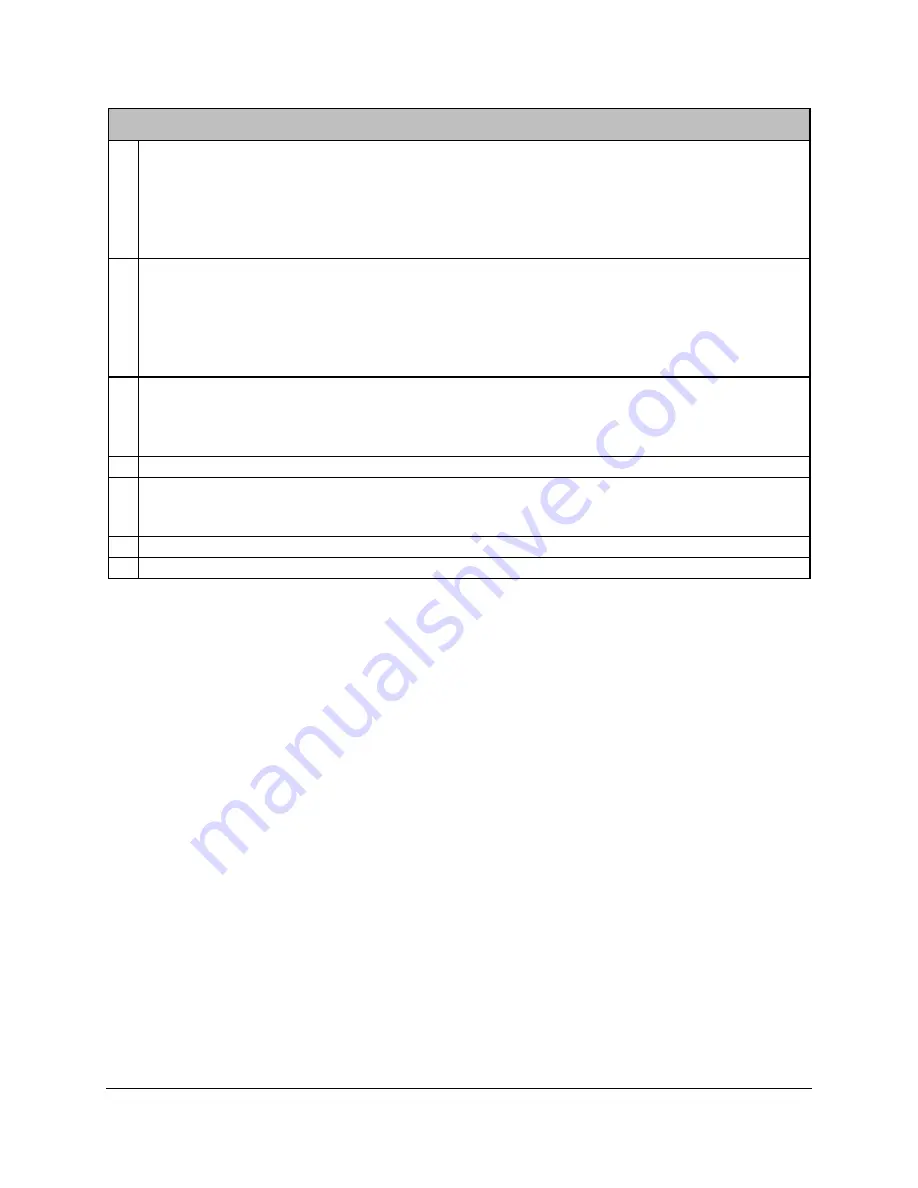
37
TRAK Machine Tools
Southwestern Industries, Inc.
TRAK TMC Mills with ProtoTRAK RMX CNC Safety, Installation, Maintenance, Service & Parts List
Installation Checklist
39. Spindle head test
Run spindle at 1000 RPM for 5 minutes
Run spindle at 8000 RPM for 5 minutes. Must be in Production Ops.
Run spindle at 500 RPM increments for a few seconds per increment.
Please note any of the following: Head noise, excessive heat on spindle, vibration, spindle fan
noise.
40. Make sure the
“ATC Tool Detect Sensor” is working and seeing a tool in the location.
Reference section 4.4.3 in manual. It is recommended to add 3 tools side by side in ATC to verify
it only sees the tool for the spot that is in front of it.
Check the tool in spindle sensor is working properly. Load a tool in the spindle when the tool
status bar says NO TOOL and you should see the status bar change to say TOOL #? and be
highlighted in yellow. Remove tool and it should go back to NO TOOL.
41. In production ops, run one of the axis rapid test programs in the TMC Inspection Programs
folder called AXIS RAPID TEST TMC5 OR 7 or 10.PT10. This will run machine at maximum rapid
speed. Confirm machine runs with no issues. See NOTES section of program for how to set up
program.
42. If the user ordered an RSG, plug it in and verify it works.
43. Assemble the tool measurement cart and tool measurement gage if this option was ordered.
Make sure to align the tool measurement gage per the instructions included with the kit. Make
sure to attach the SWI logo that comes in the hardware kit to the cart.
44. Remove front door sill protective material
.
45. Wipe down machine.
2.12
Lubrication
2.12.1
Way Lubrication
The auto lube system provides centralized automatic lubrication for the linear guides and ballscrews. The
lube pumps 1-liter reservoir is serviced with ISO VG 32/SAE 10W slideway oil. The pump is factory set to
distributor 2.7 ml of oil for every cycle of the lube pump. The lube pump cycles automatically 1 time upon
initial startup of the control and then 1 cycle for every 30 minutes of axis movement time. Each cycle of
the lube pump lasts for 5 seconds or so, once the lube pump is turned off, oil is then discharged from the
spring loaded oil manifolds to the linear guides and ballscrews.
Discharge Pressure - Approximately 200 psi
To adjust the amount of Discharge Pressure displayed on the lube pump gauge, turn the adjustment
screw clockwise to increase the pressure. 1 turn of this screw will raise the pressure about 100 psi.
At the beginning of each day, check the oil level in the Auto Lube system. If low, fill with ISO VG 32/SAE
10W slideway oil. If the lube pump runs dry or has low pressure, a flashing message will appear on the
screen that says LOW OIL or LOW PRESSURE. The control will allow the machine to complete its current
cycle and not allowing it to run the next part until the lube oil gets replenished.