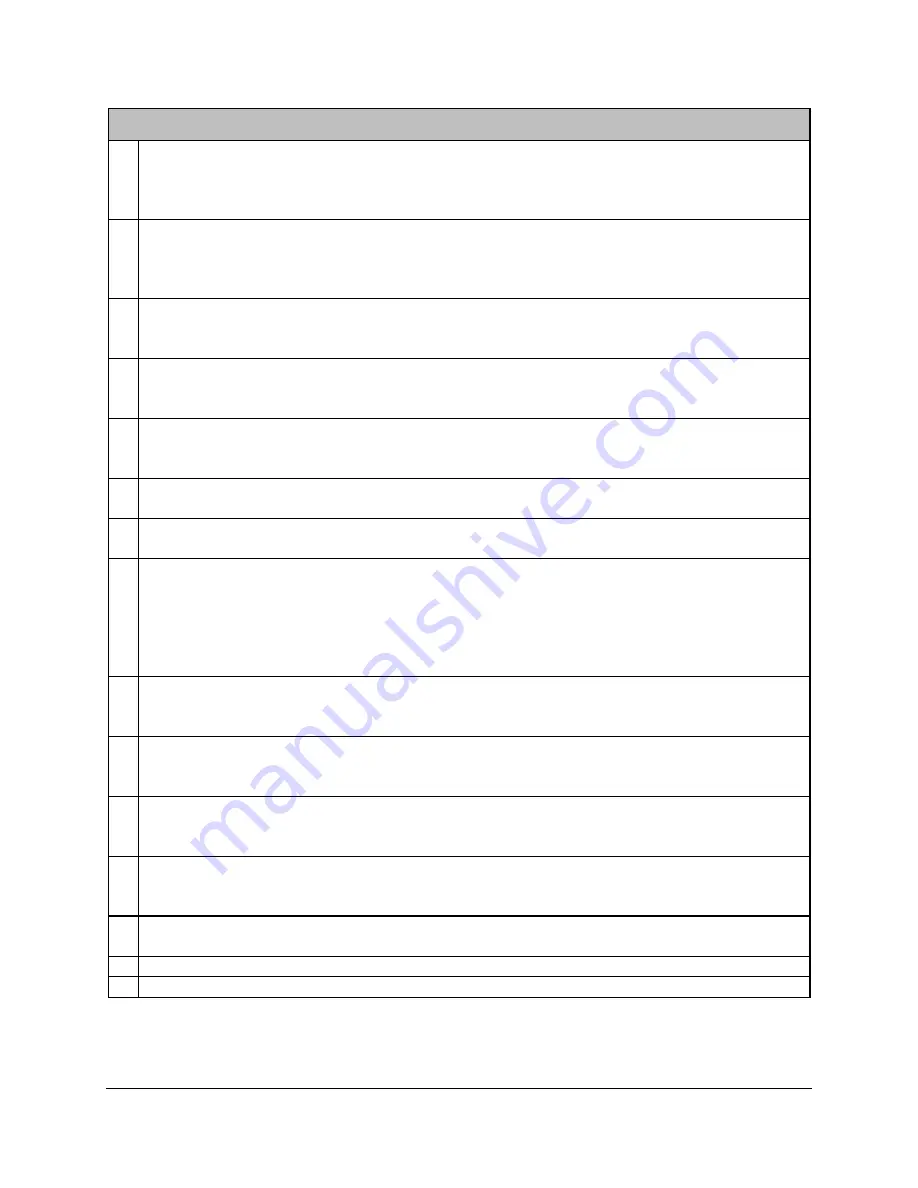
36
TRAK Machine Tools
Southwestern Industries, Inc.
TRAK TMC Mills with ProtoTRAK RMX CNC Safety, Installation, Maintenance, Service & Parts List
Installation Checklist
24. Check to make sure that the E-Stop button is functioning correctly. Turn spindle on and power
feed an axis. Press the E-stop button during this operation and verify the spindle and axis stops.
You will need to press the POWER RESET button once this is done. Make sure the Z axis does not
move when the E-stop is pressed. The brake on the Z axis motor will hold the head.
25. Turn the auger (chip conveyor) (an option on TMC5) on in the forward and reverse directions
and make sure it turns in the correct direction. You need to hold the REVERSE key down for the
auger to turn in reverse. FWD should cause the auger motor to turn CCW when viewing from the
rear of the motor.
26. Turn the coolant wash pump on and make sure it rotates in the correct direction (Clockwise).
Note -
Coolant coming out of the wash down nozzles is not an indication that the pump is turning
in the proper direction. Observe the direction of the motor fan.
27. Install the coolant and the air hoses to the front of the machine. Confirm the bracket to hold
these hoses is installed on the right side of the pendant enclosure. Confirm both hoses work and
do not leak.
28. Turn the coolant pump on by pressing the coolant ON button and make sure it rotates in the
correct direction (Clockwise).
Note -
Coolant coming out of the nozzles is not an indication that
the pump is turning in the proper direction. Observe the direction of the motor fan.
29. Turn the AIR blast on by pressing the Air ON button. Open and close the valves and make
sure there are no leaks.
30. Is the spindle motor fan running? Is it turning in the correct direction? Air should be blowing
up and away from the motor.
31. Close the door and make sure the control recognizes the door as being closed when in
production ops. When the door is open a DOOR OPEN message should be on the screen when in
DRO mode. It goes away when the door is closed.
In tool room ops, there should be no DOOR OPEN message since you can run with the door open.
Press the DOOR LOCK button to enable the door lock, powerfeed an axis and make sure the door
is locked when the machine is moving
while in production ops.
32. Press the manual tool change button on the head (GREEN button) and make sure air is coming
down through the spindle. Adjust as required.
Put a tool in the spindle and verify the tool clamps once the green button is released.
33. Move the ATC completely around all 16 stations using the ATC LOC # button in the tool table.
The door must be closed and you must be in Production Ops. Also make sure the ATC is rotating
in the correct direction.
34. Double check the tool change height with service code 501. Once verified, check to make sure
that the tools load and unload properly into the tool carousel, the tool should not deflect as the
tool is being loaded automatically into the spindle
35. Physically load a tool in and out of the carousel to make sure the orientation angle and tool
change height are correct. This can be done by assigning a library tool to the ATC. Use CALL
TOOL to bring it back to the spindle.
36. Turn off air to the machine (in-line switch) and verify the control recognizes low air pressure.
There should be a warning message on the screen.
37. Run spindle in DRO in forward and reverse at low speeds.
38. Run the 10-minute warm up program.