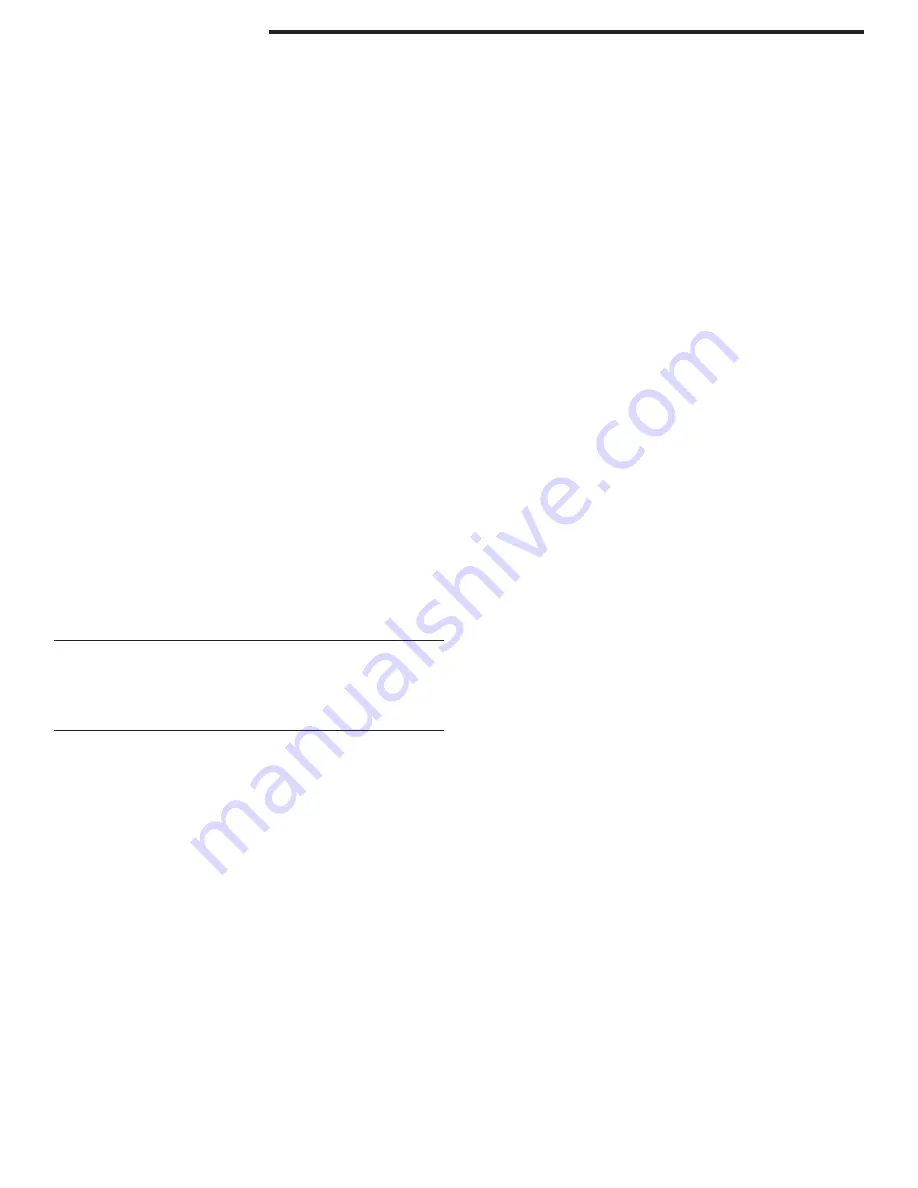
Parts Replacement
82
40-5648-51B
3. Reconnect all cable and wire connections on the
main board. These include:
• Keypad ribbon cables at J10.
• Motor cable at J3.
• Position pot cable at J6.
• Display cable at J12.
• Ear clip sensor cable at J2.
• Barrel clamp flex circuit at J4.
• Plunger cable at J11. Install the cable clamp over
the exposed braid of the plunger cable and se
-
cure with small pan head screw. Torque screw to
16 in oz (0.2 Nm).
4. If a 2nd fiber optic tail is present on the
backlight,
connect its cable to J8 on the main board. If you
are replacing an older main board (with a black
connector at J8), you can discard the backlight
adapter cable. After completing the next step, an
-
chor both fiber optic tails to the main board with a
wire tie.
5. Insert the backlight wires into the main board
terminal block. Screw the terminal connector onto
the leads with the flat edge of the LED lens toward
the outside edge of the board. Torque terminal
block screws to 32 in oz (0.4 Nm).
Note:
If you reverse the leads during installation, the
backlight will not turn on. You may wish to loosely
reassemble the case halves, plug in the battery, and
power up pump to check the backlight.
6. Close and secure the two halves of the housing
and reinstall the battery pack.
7. Complete recalibration and reconfiguration is
required when replacing main board.
Follow retest guidelines listed in the Calibration and
Adjustment section to verify pump functionality be
-
fore returning it to use.
Drive train assembly
Tools Needed
For this disassembly procedure you will need:
• Torque screwdriver with a Phillips head & ¼”
nut drive
• ¼” wrench
• .002” (.051mm) shim
Always work at an electrostatic-controlled work sta-
tion
when disassembling the pump.
Motor unit (motor, worm, worm
gear)
Removal
1. Open pump housing per pump housing section
above, and set up the case top section with the
handle down and main board facing up.
2. Remove the main board per section above.
3. Squeeze the plunger lever and fully extend the
plunger head away from the case.
4. Remove pan head screws and standoffs holding
the extrusion (drive train assembly). Remove pan
head screws and Nylock nuts holding barrel clamp
assembly to extrusion.
5. Partially slide extrusion out of case until motor
mount screws are accessible.
Disassemble motor unit as required:
1. For motor or worm, remove two pan head screws
and Nylock nuts holding the motor. Remove mo
-
tor and worm. Worm pulls straight off of motor
shaft.
2. For worm gear (plastic gear on leadscrew), remove
e-clip. Pull gear straight off of leadscrew shaft.
Replacement
Reassemble motor unit
1. For motor/worm, slide worm onto motor shaft.
Rotate motor to align mounting holes with holes
in motor plate. Ensure the motor is positioned for
the wires to properly reach the main board. Secure
motor with two pan head screws and Nylock nuts.
Torque to 100 in oz (1.2 Nm).
Содержание Medfusion 3000 Series
Страница 1: ...s Medfusion 3000 Series Technical Service Manual ...
Страница 2: ...Table of Contents ii 40 5648 51B ...
Страница 20: ...Introduction 14 40 5648 51B ...
Страница 32: ...Scheduled Maintenance 26 40 5648 51B ...
Страница 80: ...Troubleshooting 74 40 5648 51B ...
Страница 116: ...Calibration Adjustment 110 40 5648 51B ...
Страница 158: ...Assembly Drawings Parts Lists 152 40 5648 51B Medfusion 3000 series main pump assembly See Note 1 ...
Страница 160: ...Assembly Drawings Parts Lists 154 40 5648 51B Case bottom assembly Medfusion 3500BC ...
Страница 162: ...Assembly Drawings Parts Lists 156 40 5648 51B Case top assembly w plunger ...
Страница 164: ...Assembly Drawings Parts Lists 158 40 5648 51B Case top assembly without plunger ...
Страница 167: ...Assembly Drawings Parts Lists 161 40 5648 51B Barrel clamp assembly GREASE SILICONE III SOLDER NO CLEAN ...
Страница 172: ...Assembly Drawings Parts Lists 166 40 5648 51B Accessories parts list Poleclamp assembly ...
Страница 182: ...Index 176 40 5648 51B ...
Страница 183: ......