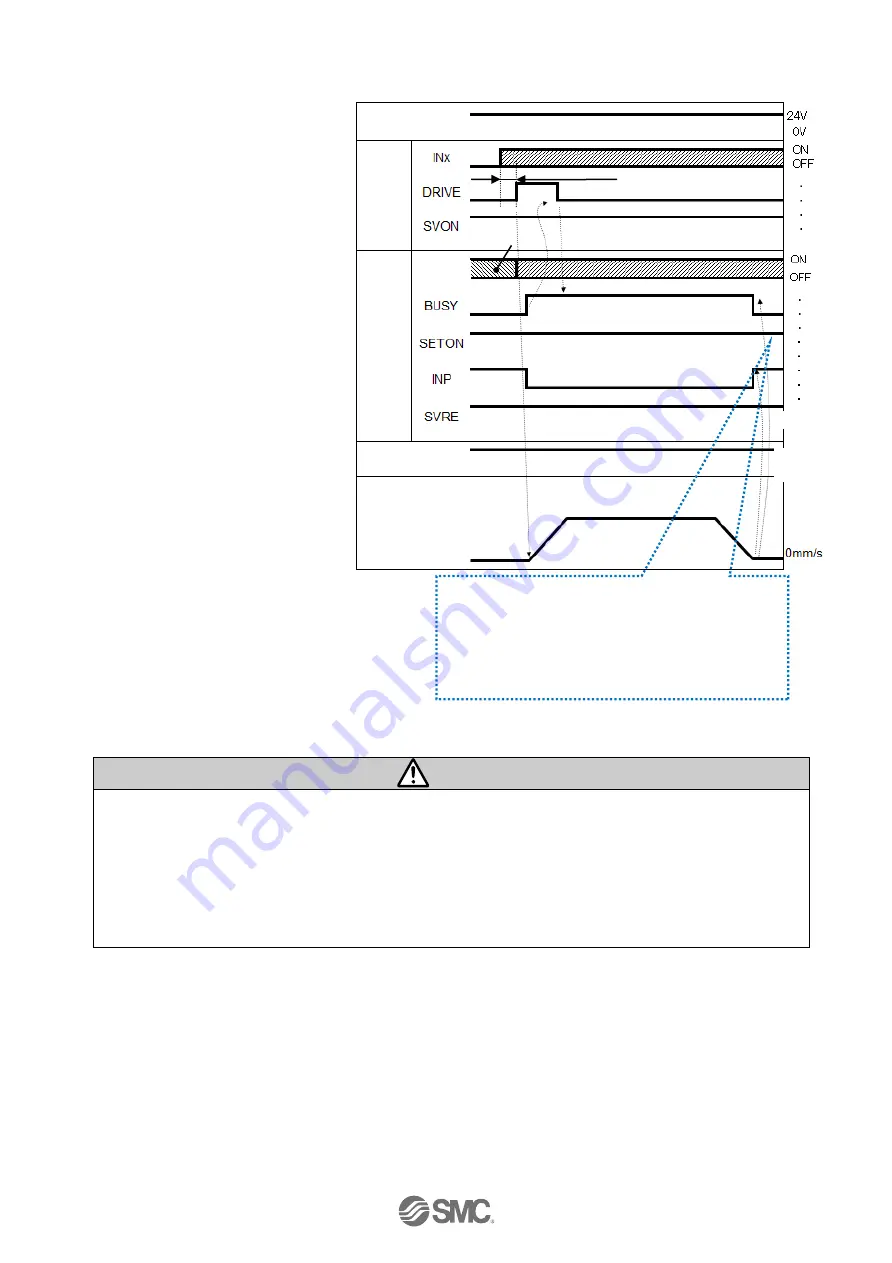
-75-
No. JXC
※
-OMT0002-C
(2) Positioning operation
- Procedure -
- Timing chart -
(a) Output the step data
No.(INx).
↓
(b)Turn the DRIVE is ON. The
step data No. (OUTx) will be
input.
↓
(c) The BUSY turns ON and INP
turns OFF. (The positioning
movement will start.)
↓
(d) When the INP is turned ON
and BUSY is turned OFF,
the positioning operation is
completed.
Caution
Design the system so that no obstacles exist adjacent to the target position which may stop
the actuators.
If the actuator is stopped by an obstacle adjacent to the target position during a positioning, the
positioning operation will be completed (INP: ON, BUSY: OFF). If an operation instruction follows this,
the positional offset from the target position of the previous operation will be reflected in the following
operation. However the offset is possible to be corrected by using the ABS instruction twice or more.
Power supply
External lock
Speed
Unlock
Holding
The INP signal is ON when all valid axes are
within the positioning range after the positioning
completion time (theoretical value) has lapsed.
The BUSY signal turns OFF when the
positioning completion time (theoretical value)
has lapsed.
Positioning
Current step No.
Previous step No.
OUTx
Min.15ms
In
p
u
t
O
u
tp
u
t