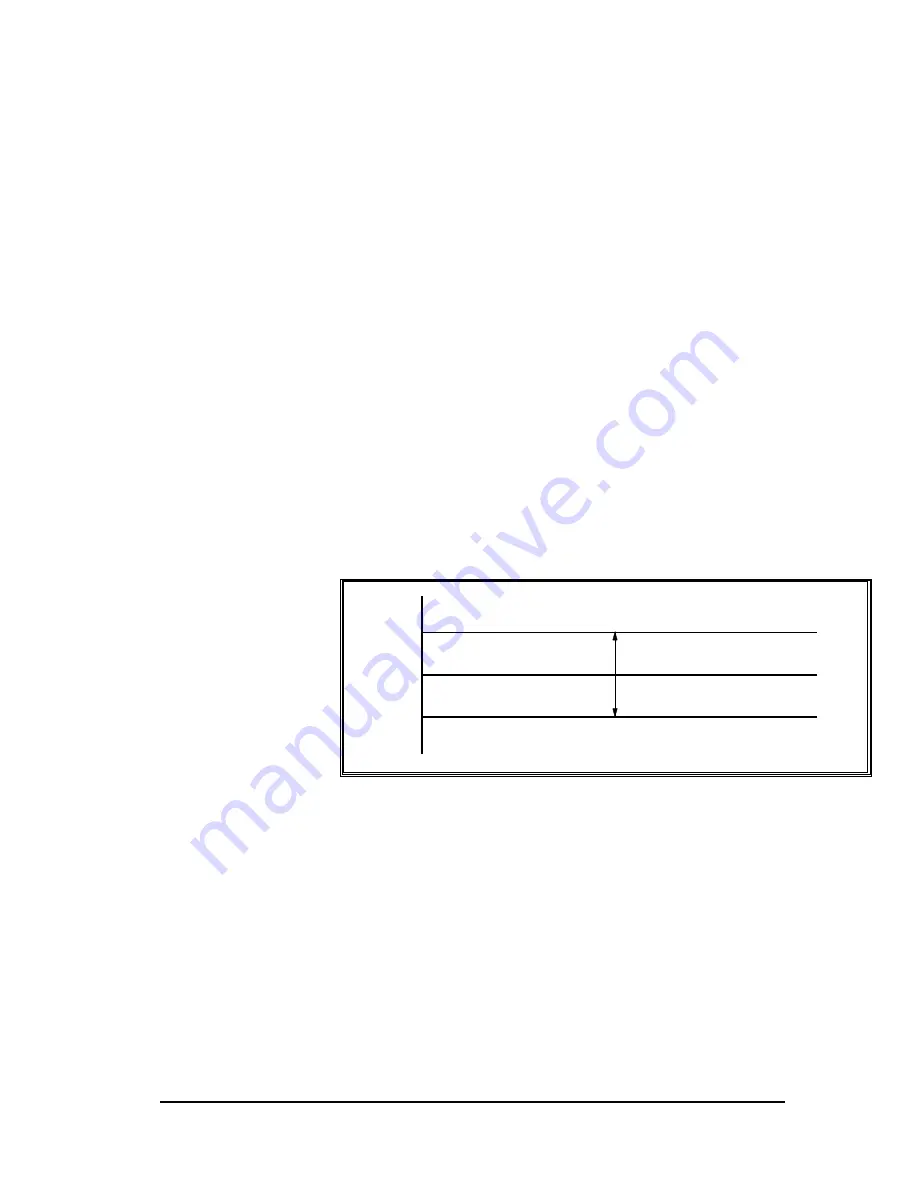
Simatic 505 SoftShop
9 - PID Loops
••••
165
The PID algorithm consists of three components: the Proportional, the
Integral (Reset), and the Derivative (Rate). Each component impacts the
output to address the varied characteristics of the process variable. The
PID expression is:
Output = P_Gain * Error + I_Gain *
⌡
⌠
0
t
Error (dt) + D_Gain * Error (d / dt)
where,
Error =
Setpoint - Process Variable
P_Gain =
Proportional Gain
I_Gain =
Integral Gain
D_Gain =
Derivative Gain
The Proportional Component
Temperature control with PID has two regions of operation, the
proportional band, and the saturated region. The proportional band is the
region above and below the setpoint where the controller output is less
than 100%. The heat or cooling output is time proportioned as
determined by the PID output. The proportional gain value determines
the proportional band.
A typical proportional band might be around ±30
°
F for a given
machinery temperature control, as shown in Figure 9-7. For example,
with a setpoint of 300
°
F, a proportional band of ±30
°
F would equate to
the region between 270
°
F and 330
°
F, where the controller would be in
the proportional band. Outside of this region, on either side, is the
saturated region where the controller output would be 100%, which
equates to 100% heating or cooling.
330°F
300°F
270°F
100% Output
Setpoint
100% Output
Proportional Band
Output = Proportional Gain * Error
Figure 9-7 Proportional Band
A temperature controller using only the proportional component of the
PID expression may experience a steady state error, as shown in Figure 9-
8. This error is induced by thermal loading on a temperature zone. As the
thermal loading on a temperature zone increases, the magnitude of the
steady state error is increased.