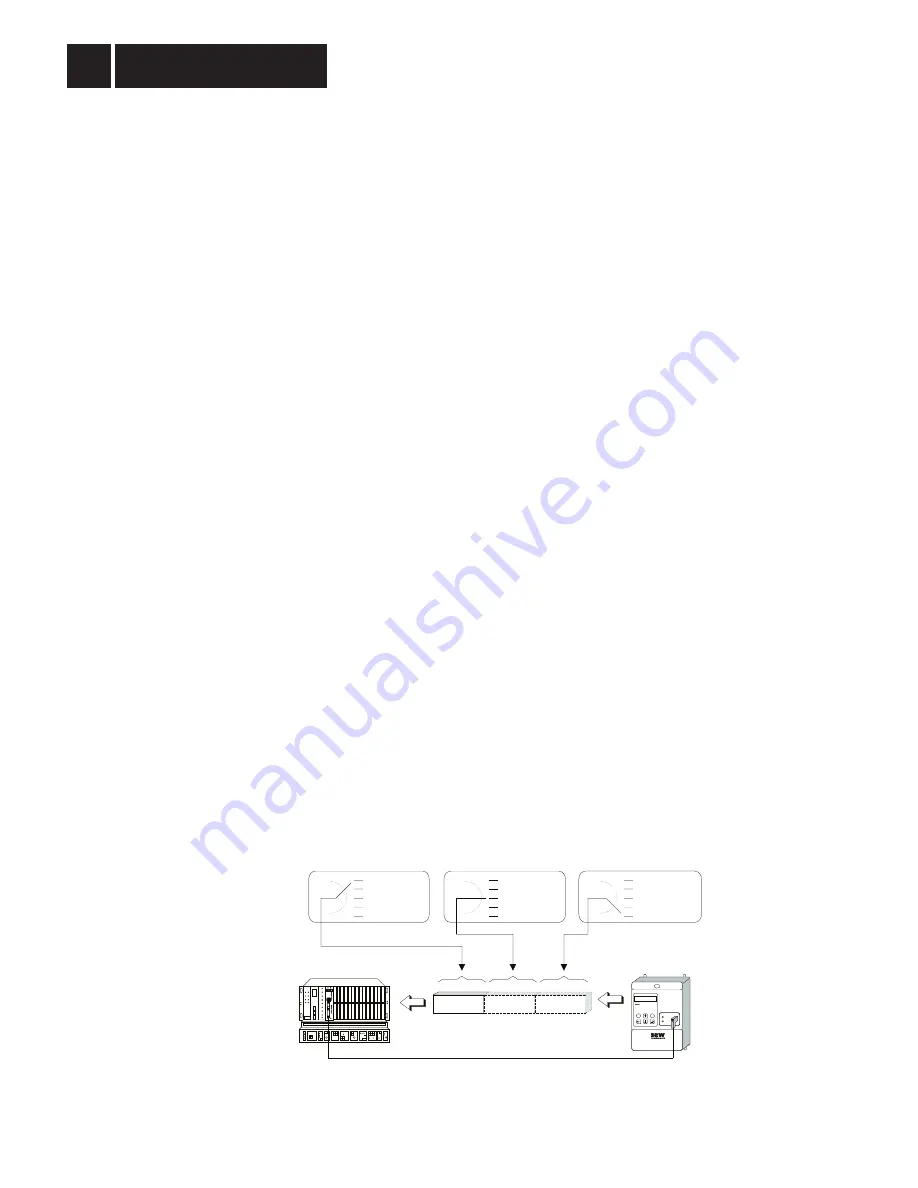
Duplicate Usage of the Process Output Data Channel
If several process output data words contain the same setpoint description, only the process output
data word which is read first will be valid. The processing sequence in the inverter is PO1 - PO2 -
PO3, i.e. if PO2 and PO3 contain the same setpoint description, only PO2 will be effective. The content
of PO3 will be ignored.
Example: Duplicate usage of PO2 and PO3
Process output data words PO2 and PO3 both contain the SPEED setpoint.
P560
PO1 Setpoint Description = CONTROL WORD 1
P562
PO2 Setpoint Description = SPEED
P564
PO3 Setpoint Description = SPEED
The speed setpoint is transmitted twice within the process output data channel (duplicate usage of
process output data words). As the inverter processes the process output data words in the order
PO1 - PO2 - PO3 and recognizes duplicate usage of the process output data channel, the speed
setpoint transmitted in PO3 will never become effective.
Simultaneous Transmission of Control Word 1 and Control Word 2
If control words 1 and 2 are transmitted simultaneously, the inverter is controlled in the same way
via the basic control block of control word 1 and the basic control block of control word 2. In this
case you must make sure that both basic control blocks are coded the same. The inverter will only
be enabled, if both the digital input terminals and control words 1 and 2 give the enable command.
The virtual terminals of control word 2 are evaluated directly only if they do not correspond to a
control word 1 function.
32-Bit Process Output Data
Process data which are longer than 16 bits and therefore occupy more than one process data word
will only be processed by the inverter if they are completely mapped to the process data channel. The
position setpoint, for example, will only become effective if completely mapped to the process output
data channel. Consequently both POSITION HI and POSITION LO must be specified in the process
output data channel.
3.3.3
Actual Value Description of the PI Data
The
PI1 - PI3 Actual Value Description parameters define the content of the process input data words
which are transferred from the inverter to the higher level automation unit through the fieldbus system
(Fig. 8). Each process data word is defined by its own parameter, so altogether three parameters are
required to describe the process input data.
M
O
VI
TRAC
®
841
E
Q
RUN
BUS
FAULT
PD1
PD2
PD3
P565: PI3 ACT. VALUE DESCRIPT.
P563: PI2 ACT. VALUE DESCRIPT.
P561: PI1 ACT. VALUE DESCRIPT.
Status word 1
Status word 2
Speed actual value
App. current value
etc.
Status word 1
Status word 2
Speed actual value
App. current value
etc.
Status word 1
Status word 2
Speed actual value
App. current value
etc.
Fieldbus
CONTROL MODE
Process intput data (PI)
00318AEN
Fig. 8: Actual value description of the process input data (PI)
Inverter Control
with Process Data
3
18
MOVITRAC
®
31.. Fieldbus Unit Profile
Phone: 800.894.0412 - Fax: 888.723.4773 - Web: www.clrwtr.com - Email: [email protected]