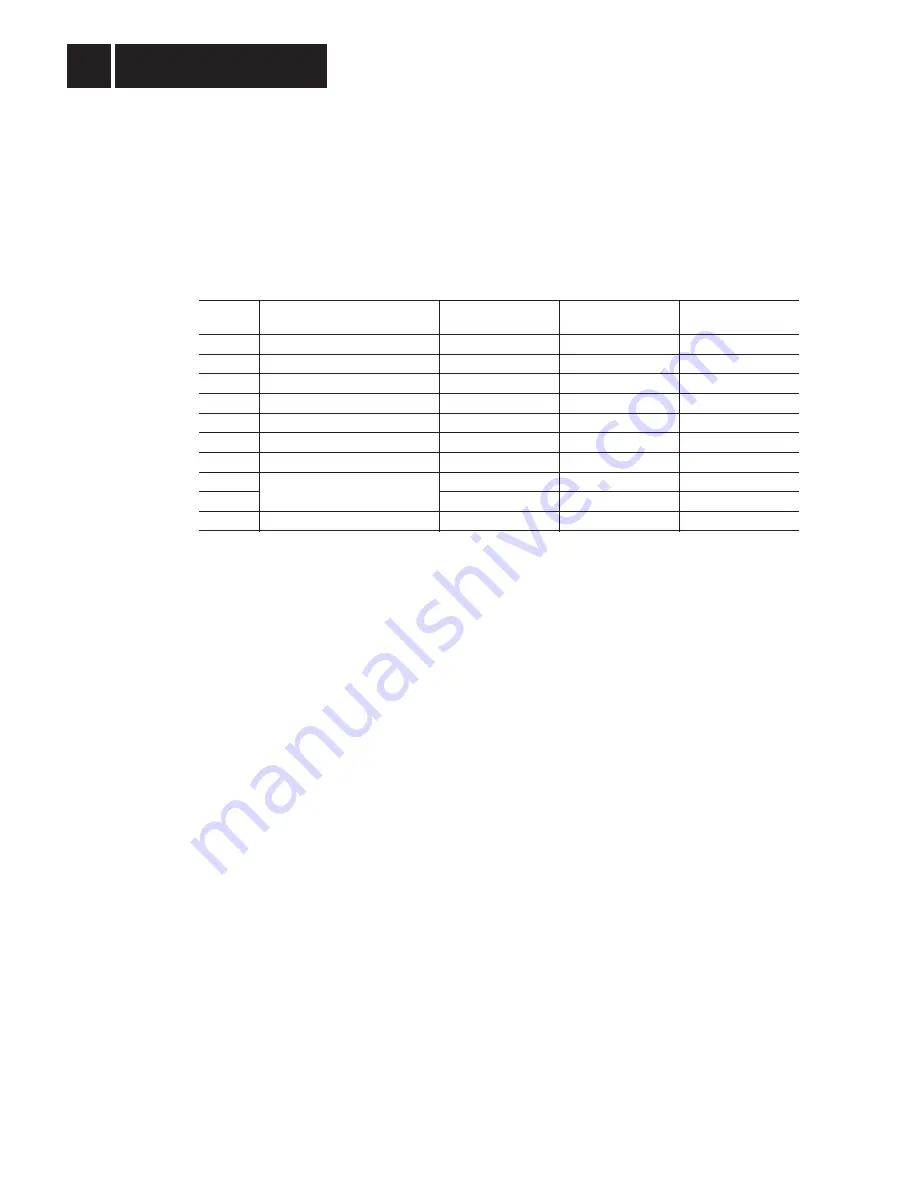
7.2.4
Start-up Parameter Setting via a Fieldbus
The manual configuration procedure described in section 7.2.2. can also be carried out automatically
by the higher-level fieldbus master, i.e. all the drive parameters can be set automatically via the
fieldbus when the control system starts up. In order to automatically set start-up parameters, please
consult the
MOVITRAC
®
31.. Parameter List to establish the fieldbus index and the coding for the
relevant setting from the menu numbers given in section 7.2.2.
The following table shows the indices and codings for start-up parameter setting taken from the
Parameter List.
Menu no. Parameter name
Setting
Fieldbus index
(decimal)
Coding
(4 byte hex)
830
FACTORY SETTING
YES
1203
00 00 01 00
841
CONTROL MODE
FIELDBUS
1205
00 00 03 00
564
PO3 SETP. DESCRIPT.
RAMP
1603
00 00 08 00
565
PI3 ACT. VALUE DESCRIPT.
APPARENT CURRENT 1606
00 00 02 00
570
ENABLE SETPOINTS
YES
1607
00 00 01 00
571
FIELDBBUS TIMEOUT
0.10
1608
00 00 00 10
572
TIMEOUT RESPONSE
RAPID STOP
1609
00 00 00 00
...
drive-specific parameters
...
...
...
...
...
...
...
140
T13 RAMP STOP
0.20
1028
00 00 00 20
The parameters listed in the table can now be transferred to the inverter in the required order, e.g.
via individual write services or via the download parameter block if supported by the option pcb.
However, please note that all other parameters can only be written once the factory settings have
been completely activated.
7.3
Relative speed / I/O-module functionality
The following application example shows how the inverter is controlled via the relative speed setting.
Additionally the I/O-module is used, so the higher-level automation unit reads 5 sensor signals via
the input terminals of the inverter and controls a relay via output terminal 62.
Therefore the inverter is controlled via two process data words. The process output data
control
word 2 and speed [%]-setpoint is specified by the higher-level control, in the opposite direction the
inverter returns the process input data
status word 2 and speed [%]-actual value to the higher-level
control. The control program is supposed to control the following inverter functions:
1) The digital input E1.1 is to trigger the control commands Enable and Stop.
E1.1 = 1: Enable
E1.1 = 0: Stop
2) The digital input E1.2 is to specify the speed [%]-setpoint.
E1.2 = 1: CW operation with 75 % of
P220 F-MAX 1
E1.2 = 0: CCW operation with 25 % of
P220 F-MAX 1
Application Examples
7
66
MOVITRAC
®
31.. Fieldbus Unit Profile
Phone: 800.894.0412 - Fax: 888.723.4773 - Web: www.clrwtr.com - Email: [email protected]