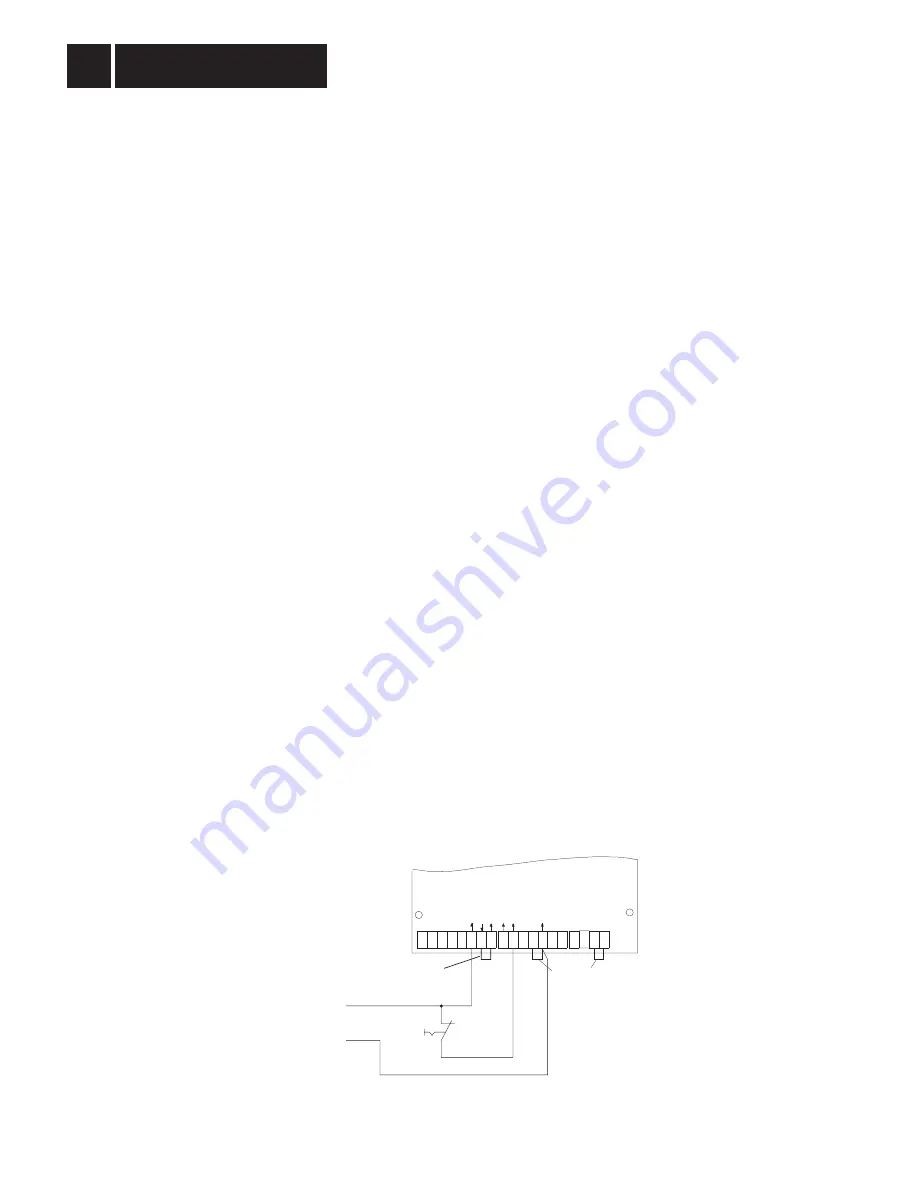
7.2.1
Objective
The inverter is to be controlled by means of three process data words. The process output data
Control
Word 1, Speed Setpoint and Ramp are to be specified by the higher-level control unit. Conversely,
the inverter is to return the process input data
Status Word 1, Speed Actual Value and Apparent
Current Actual Value to the higher-level control unit.
The application program is to control the following inverter functions:
1) The digital input E1.1 is to trigger the control commands
Enable and Stop.
E1.1 = 1: Enable
E1.1 = 0: Stop
2) The digital input E1.2 is to trigger the control commands
Enable and Rapid Stop.
E1.2 = 1: Enable
E1.2 = 0: Rapid stop
3) The digital input E1.3 is to specify the speed setpoint.
E1.3 = 1: 750 1/min CCW
E1.3 = 0: 1000 1/min CW
4) In the application, the acceleration and deceleration ramp generators are continually
recalculated by another function module and temporarily stored in the flag words
MW 100: current acceleration ramp generator
MW 102: current deceleration ramp generator.
Only parameter set 1 and ramp generator set 1 are used. The drive is to be accelerated or decelerated
with the ramp that is specified via the fieldbus and that can be continually varied. The rapid stop shall
take place within 200 ms.The inverter is also to recognize a bus error that lasts longer than 100 ms
and to use the rapid stop to bring the drive to a standstill. In an emergency stop situation, the inverter
is to carry out a rapid stop independently of the fieldbus, directly via the input terminals.
7.2.2
Commissioning
We recommend using the following method to implement this application example:
1. Wire the inverter in accordance with the installation and operating instructions. To operate with
the fieldbus, connect the inverter to an external 24 V supply (terminals 30 and 40). Insert a jumper
between terminals 41 and 44 in order to enable the inverter on the terminal side (Fig. 43). Connect
the emergency stop switch with input terminal 43 (Enable) on the inverter, in order to enable the
emergency stop function to operate independently of the fieldbus.
31
34
35
0
65
40
44
41
42
43
47
60
30
61
62
48
49
60
30
X2
X3
X14
+24V
0V24
24 V
+
-
+24V (external)
Jumpers installed when supplied
Use this jumper to enable
the inverter on the
terminal side
1/0 ENABLE/
RAPID STOP
1/0 CCW/STOP
1/0 CW/STOP
EMERGENCY
STOP
00350AEN
Fig. 43: Wiring of the inverter with emergency stop function
Application Examples
7
62
MOVITRAC
®
31.. Fieldbus Unit Profile
Phone: 800.894.0412 - Fax: 888.723.4773 - Web: www.clrwtr.com - Email: [email protected]