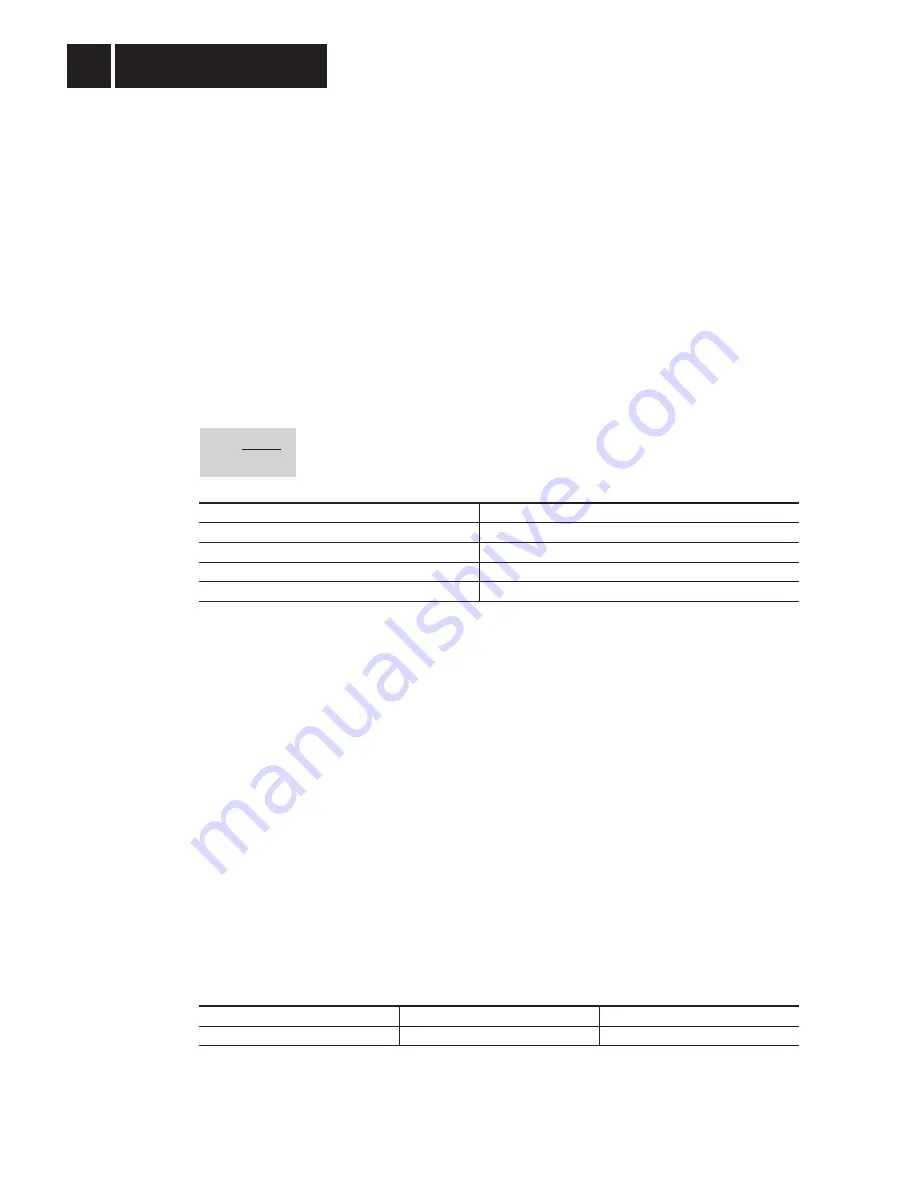
Slip Compensation (SLIP) (not for MOVITRAC
®
31.., size 0)
The
SLIP setting causes the MOVITRAC
®
31.. inverter to interpret the transmitted process output
data word as slip compensation value. Scaling of the slip compensation value in the unit [1/min] see
Section 3.3.5.
Entering the slip compensation via the fieldbus will automatically deactivate parameters
P323 SLIP 1
and P343 SLIP 2.
Entering the slip compensation via the process data channel only makes sense for applications which
operated under speed control as a change in the slip compensation will also have an indirect effect
on the torque.
The range of values for this slip compensation value is identical with the range of values for parameter
P323 SLIP 1 and corresponds to a frequency range of 0-10 Hz. When specified via the process data
channel, the slip compensation will be in the unit [1/min], you will therefore have to take account of
the pole pair number of the connected motor. To calculate the range of values for the slip speed use
the following formula:
The value ranges for motors with different pole pair numbers determined from the above formula.
Motor pole pair number
Value range
1
0 - 600 1/min
2
0 - 300 1/min
3
0 - 200 1/min
4
0 - 150 1/min
If the slip specified in the process data is outside this range of values, the minimum or maximum will
become effective if the specified slip is lower or higher than the given value range.
Process Ramp (RAMP)
The
RAMP setting causes the MOVITRAC
®
31.. inverter to interpret the transmitted setpoint as
acceleration or deceleration ramp. Depending on the drive function specified in the control word, the
unit will interpret the process ramp as acceleration ramp when an enable signal is given and as
deceleration ramp when a stop is to be executed. The specified figure is the time in milliseconds and
relates to a frequency change of 50 Hz. The rapid stop function is not affected by this process ramp.
When the process ramp is transmitted through the fieldbus system, ramp generators T11, T12, T21
and T22 will become inactive.
Scaling of the
Process Ramp in the unit [ms] see Section 3.3.5.
Control Word 1 / Control Word 2
Assigning control word 1 or control word 2 to the process output data allows you to activate nearly
all drive functions via the fieldbus system. For a description of control words 1 and 2 see Section 3.4.
Factory Setting for the
PO1-PO3 Setpoint Description
When the factory setting has been activated, the following process output data are defined for the
MOVITRAC
®
31.. inverter:
PO 1 Setpoint Description:
PO 2 Setpoint Description:
PO 3 Setpoint Description:
CONTROL WORD 1
SPEED
NO FUNCTION
n
S
= slip speed specified
f
S
= slip frequency
p = pole pair number of the motor
f
s
• 60
n
s
=
p
Inverter Control
with Process Data
3
16
MOVITRAC
®
31.. Fieldbus Unit Profile
Phone: 800.894.0412 - Fax: 888.723.4773 - Web: www.clrwtr.com - Email: [email protected]