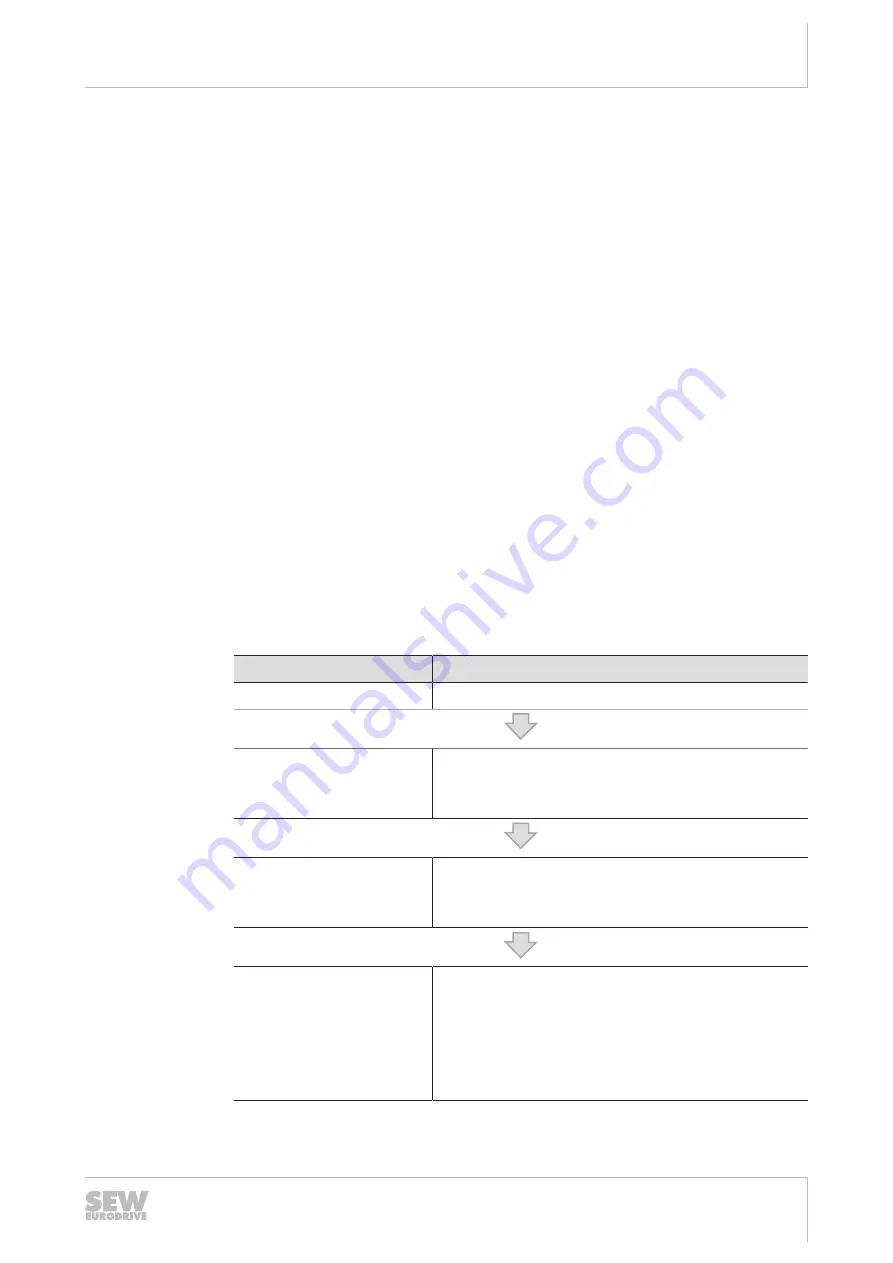
4
Assembly and installation
Sequence
Assembly and Operating Instructions – Parallel Arm Kinematics Kit
29
4.3.4
Cable routing
Observe the following rules:
•
To connect the power supply and the communication, use suitable cables.
•
Route power cables and signal cables in separate cable ducts.
•
Choose the greatest possible distance between power cables and signal cables.
•
Avoid using long cables running parallel to one another.
4.3.5
Shielding
Observe the following rules:
•
The power signals and electronics signals (motor and control leads) are installed in
shielded cables.
•
The shield against capacitive coupling is applied to at least one end.
•
A shield end is applied using a capacitor to avoid excessive loop currents.
•
For cables with single shielding, the shield to the connector housing is applied on
both ends over a wide area.
•
For cables with double shielding (e.g. hybrid cables), the outer shielding is applied
to the unit side and the inner shielding to the other side (e.g. on the motor).
•
For external buses, the bus-specific installation instructions apply.
4.4
Sequence
Install the components in the following order:
Component
Required documentation
Robot mechanics
Documentation of the robot mechanics
Drives robot arms
Drive tool/gripper
"CMP40 – CMP112, CMPZ71 – CMPZ100 Synchron-
ous Servomotors" operating instructions
Chapter "Installation"
MOVI-C
®
CONTROLLER
power control cabinet con-
troller
"MOVI-C
®
CONTROLLER power UHX85A and power
eco UHX84A" operating instructions
Chapter "Installation notes"
MOVIDRIVE
®
drive inverters •
Stand-alone: "MOVIDRIVE
®
system application in-
verter" operating instructions
Chapter "Installation"
•
Integrated: "MOVIDRIVE
®
modular application in-
verter" operating instructions
Chapter "Installation"
25797530/EN – 04/2018