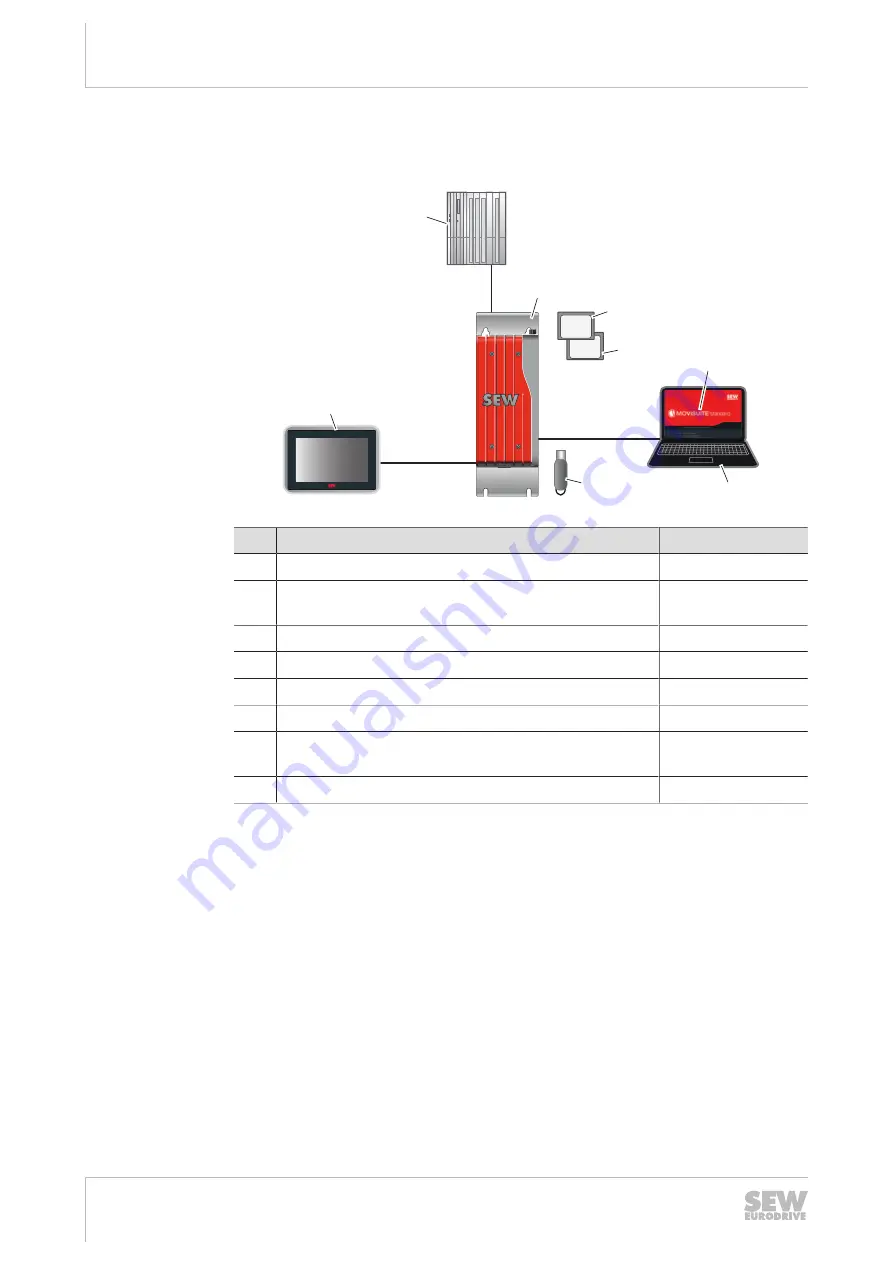
3
Application
Control and visualization
Assembly and Operating Instructions – Parallel Arm Kinematics Kit
18
3.5
Control and visualization
3.5.1
Technical diagram
[1]
[2]
[7]
[8]
[4]
[3]
[5]
[6]
20451967883
No.
Component
Part number
[1]
Higher-level controller (PLC) (optional)
–
[2]
MOVI‑C
®
CONTROLLER power UHX85A-R
(PROFINET) control cabinet controller
Configured
[3]
Windows memory card OMW72A (optional)
28208331
[4]
CFast memory card OMH85A
Configured
[5]
Software
–
[6]
Laptop
–
[7]
Runtime Licence Dongle ORV71C. USB-Dongle for
HMI-Builder PRO (optional)
17974305
[8]
Monitor (optional)
Configurable
3.5.2
Functional principle
The MOVI-C
®
CONTROLLER power control cabinet controller coordinates the axes
and thus the movements of the robot.
The data of the application is visualized on a monitor.
Components
The used components depend on the design of the robot:
•
Stand-alone: A MOVI-C
®
CONTROLLER power control cabinet controller controls
several MOVIDRIVE
®
system drive inverters.
•
Integrated: A MOVI-C
®
CONTROLLER power control cabinet controller controls
one or several MOVIDRIVE
®
modular application inverters.
The control cabinet controller can control up to 32 interpolating axes and 32 auxiliary
axes. The parameterization and startup of the devices are performed in the
MOVISUITE
®
software.
25797530/EN – 04/2018