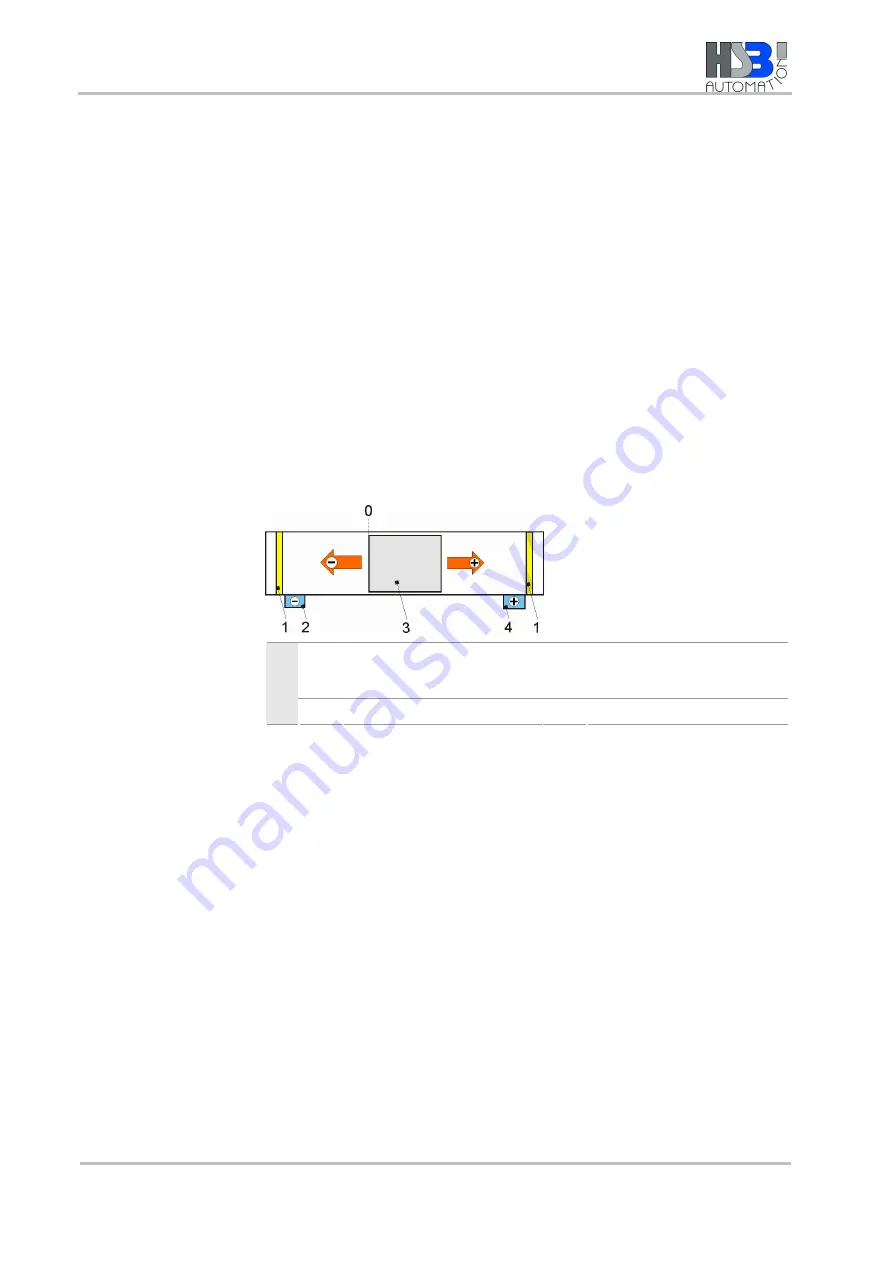
Installation and adjustment
24
2010-09-15
FM 239 MuW Beta Type Z Rev.01
Procedure
1.
Connect the power to the limit switches.
2.
Slacken the bracket fixing screw (figure 5).
3.
Run the carriage as far as the safety zone.
4.
Move the limit switch until it trips.
5.
Tighten the bracket fixing screw.
6.
Check the correct position of the limit switch: Move the carriage
manually and observe the switching operation.
If the braking distance is too short, repeat the set-up.
6.4
Mounting a drive unit
Make sure the direction of rotation of the external drive unit takes into
account the direction of the spindle or timing belt so that the limit
switches work correctly.
1
Safety zone
3
Carriage with positive and
negative directions from
reference point 0
Key
2
Negative limit switch
4
Positive limit switch
Figure 7: Example of travel direction and limit switch configuration
Содержание RPE 100
Страница 24: ...24 01 RPE en 2011 08 04 SK CW ...
Страница 25: ...Appendix 1 Linear axis Beta ...
Страница 26: ...2 01 LPE de 2011 03 18 SK CW ...
Страница 27: ......
Страница 28: ......
Страница 29: ......
Страница 30: ......
Страница 31: ......
Страница 33: ......
Страница 71: ......
Страница 110: ...Appendix 2 Drive MSK ...
Страница 111: ...2 01 LPE de 2011 03 18 SK CW ...