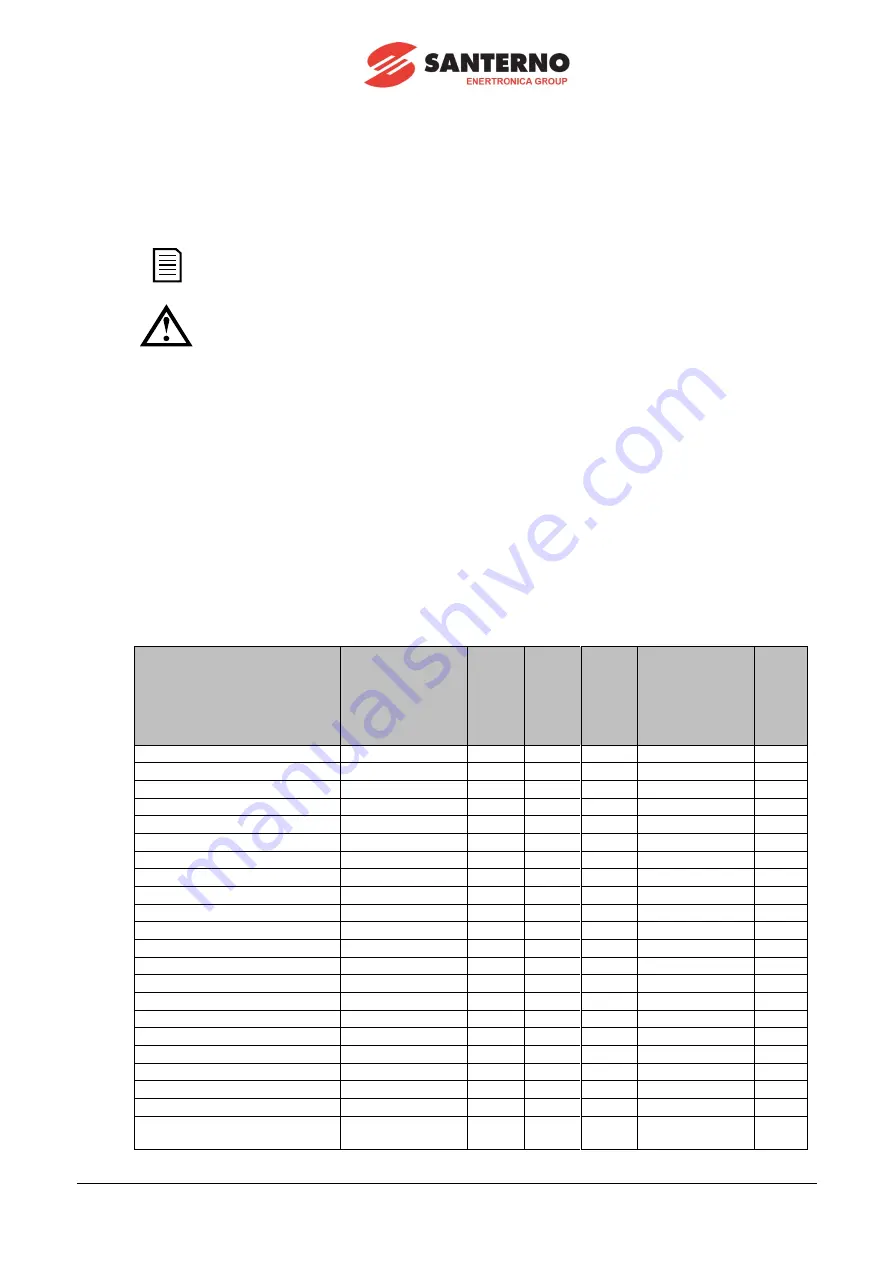
8.5
Emergency Mode
Emergency mode allows the ASA 4.0 Advanced to run the motor and ignore trip conditions.
Emergency mode is controlled via a programmable input (input A 13, 14 or input B 13, 15) and parameter 7A
Input A Function
/7E
Input
B Function
must be set to 'Emergency Mode'. A closed circuit across 13, 14 activates emergency mode. When the ASA 4.0 Advanced
receives a start command, it will continue to run until a stop command is received, ignoring all trips and warnings.
Emergency mode can be used in conjunction with any command source.
NOTE
Although emergency mode operation satisfies the functionality requirements of Fire Mode, Santerno does not
recommend its use in situations that require testing and/or compliance with specific standards as it is not certified.
CAUTION
Continued use of emergency mode is not recommended. Emergency mode may compromise the starter and/or motor life
as all protections and trips are disabled.
Using the starter in emergency mode will void the product warranty.
8.6
Auxiliary Trip
An external trip circuit (such as a low pressure alarm switch for a pumping system) can be used to trip the soft starter and stop the
motor. The external circuit is connected to a programmable input (input A 13, 14 or input B 13, 15). To control the behaviour of the trip,
set the following parameters:
•
Parameter 7A
Input A Function
: select 'Input Trip (N/O)'.
•
Parameter 7B
Input A Trip
: set as required. For example, 'Run Only' limits the input trip to when the soft starter is running
only.
•
Parameter 7C
Input A Trip Delay
: sets a delay between the input activating and the soft starter tripping.
•
Parameter 7D
Input A Initial Delay
: sets a delay before the soft starter monitors the state of the input, after the start signal.
For example, a delay may be required to allow time for pipeline pressure to build up.
•
Parameter 7J
Input A Name
: select a name, eg 'Input A Trip' (optional).
8.7
Typical Control Methods
The requirements of an application differ between each installation, but the methods listed below are often a good starting point for
common applications.
Application
Start Mode
Sta
rt
Ra
mp
T
ime
(seco
nd
s)
In
itia
l C
ur
re
nt
(%
FL
C)
Cur
re
nt
Li
m
it
(%
FL
C)
Stop Mode
St
op Ti
m
e
(seco
nd
s)
Bow thruster
Constant Current
5
100
400
Coast To Stop
n/a
Centrifuge (Separator)
Constant Current
1
200
450
Coast To Stop
n/a
Chipper
Constant Current
1
200
450
Coast To Stop
n/a
Compressor - reciprocating - loaded
Constant Current
1
200
450
Coast To Stop
n/a
Compressor - reciprocating - unloaded
Constant Current
1
200
400
Coast To Stop
n/a
Compressor - screw - loaded
Constant Current
1
200
400
Coast To Stop
n/a
Compressor - screw - unloaded
Constant Current
1
200
350
Coast To Stop
n/a
Conveyor - horizontal
Constant Current
5
200
400
TVR Soft Stop
10
Conveyor - inclined
Constant Current
2
200
450
Coast To Stop
n/a
Conveyor - vertical (bucket)
Constant Current
2
200
450
Coast To Stop
n/a
Crusher - cone
Constant Current
1
200
350
Coast To Stop
n/a
Crusher - jaw
Constant Current
1
200
450
Coast To Stop
n/a
Crusher - rotary
Constant Current
1
200
400
Coast To Stop
n/a
Debarker
Constant Current
1
200
350
Coast To Stop
n/a
Fan - axial (damped)
Constant Current
1
200
350
Coast To Stop
n/a
Fan - axial (undamped)
Constant Current
1
200
450
Coast To Stop
n/a
Fan - centrifugal (damped)
Constant Current
1
200
350
Coast To Stop
n/a
Fan - centrifugal (undamped)
Constant Current
1
200
450
Coast To Stop
n/a
Fan - high pressure
Constant Current
1
200
450
Coast To Stop
n/a
Mill - ball
Constant Current
1
200
450
Coast To Stop
n/a
Mill - hammer
Constant Current
1
200
450
Coast To Stop
n/a
Pump - bore
Adaptive Control
(Early accel.)
3
n/a
500
Adaptive Control
(Late decel.)
3
34/78
ASA 4.0 Advanced
Содержание ASA 4.0 Advanced
Страница 78: ...78 78 ASA 4 0 Advanced ...