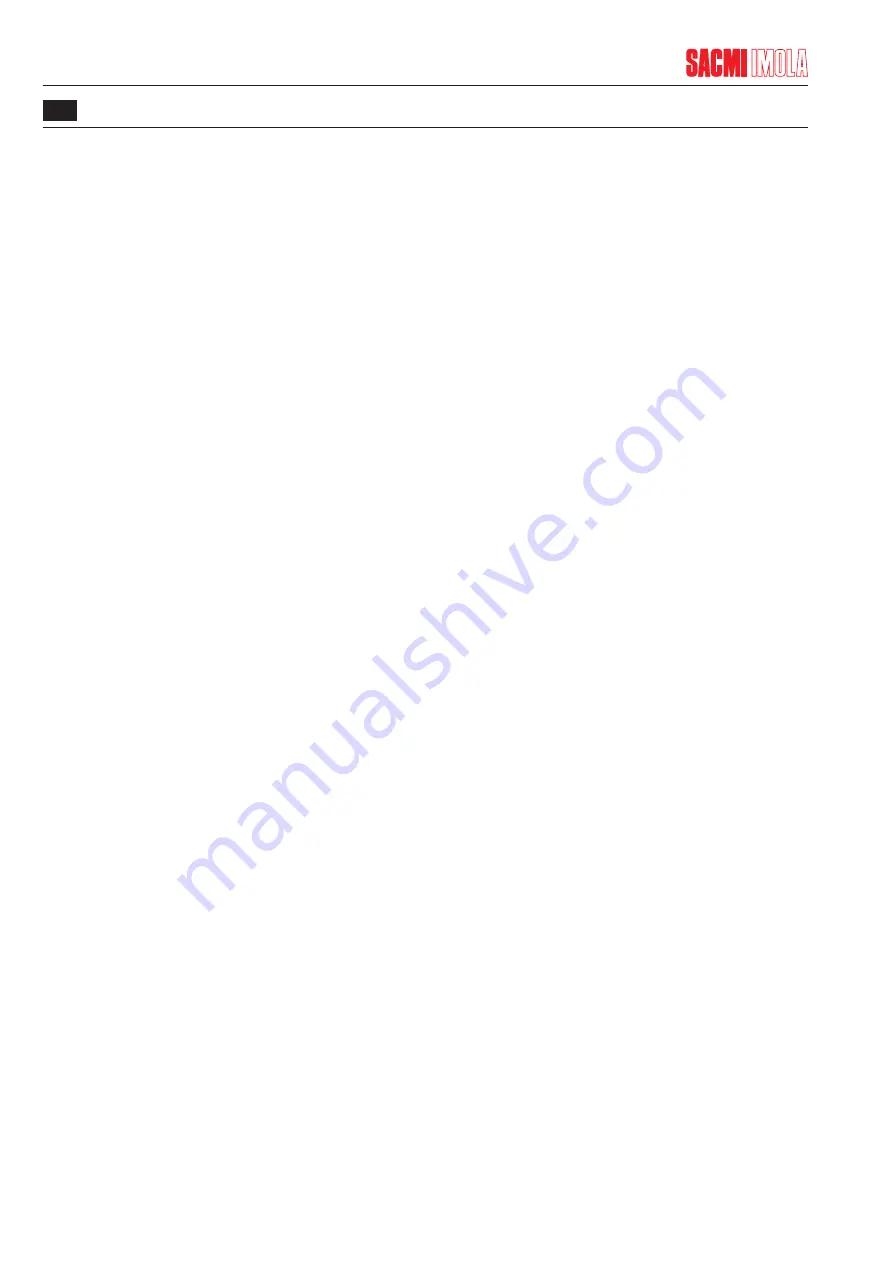
062AZ005A
7
ADJUSTMENTS
7-2
7.1.3
PROCEDURE FOR INSPECTING PRODUCTS
The following are needed to carry out the test procedure for the product in question:
- at least ten samples of each defect the vision system has to detect and reject;
- at least one hundred good quality sample pieces, in any case more good quality samples have to be provided than
defective ones. The percentage should be approximately 10% defective pieces and 90% good quality ones.
The samples should be selected as follows:
- they should all be produced on the line on which the vision system is installed and be for the same product;
- the defects have to be real defects that may be produced during production and not simulated with tools or
markers;
- the defects have to represent a panorama of all defects that may be found in the production line for the product in
question.
To aid in identifying the pieces, the defective pieces should be marked in an area in which inspection is not possible,
for example the side opposite the one used for piece inspection.
Proceed as directed below:
- Stop the production run and empty the conveyor belt.
- Turn on the vision system and select the correct inspection configuration.
- Use two empty containers, one for defective pieces and the other for good quality ones, to collect the pieces being
inspected on the conveyor belt.
- Mix the defective pieces and good quality ones together and feed them to the vision system. The normal operating
speed and spacing between the pieces should be used.
- Examine the results of the inspection, noting if:
- good quality samples were rejected, i.e. number of false rejects;
- defective samples were not rejected, i.e. number of false good quality pieces.
Repeat the procedure a few times and determine whether or not the number of false rejects and false good quality
pieces fall within the scope of the quality standards for that product.
If the results are not satisfactory, locate the trouble, remedy it and then repeat the procedure.
Содержание Imola CHS Series
Страница 2: ......
Страница 4: ...062AZ005A...
Страница 8: ...062AZ005A TABLE OF CONTENTS Page 0 8 9 DISMANTLING 9 1 9 1 DECOMMISSIONING 9 1 9 2 DISMANTLING 9 2...
Страница 15: ...062AZ005A GENERAL INFORMATION 1 1 7 FIGURE 1 8 B CHS200 MACHINE IDENTIFICATION PLATE T6864 E0206...
Страница 48: ...062AZ005A 2 FEATURES 2 32...
Страница 74: ...062AZ005A 4 INSTALLATION 4 8 FIGURE 4 3 2 1 B CONNECTING THE SPARK TESTER DEVICE ELECTRIC CABLES...
Страница 76: ...062AZ005A 4 INSTALLATION 4 10...