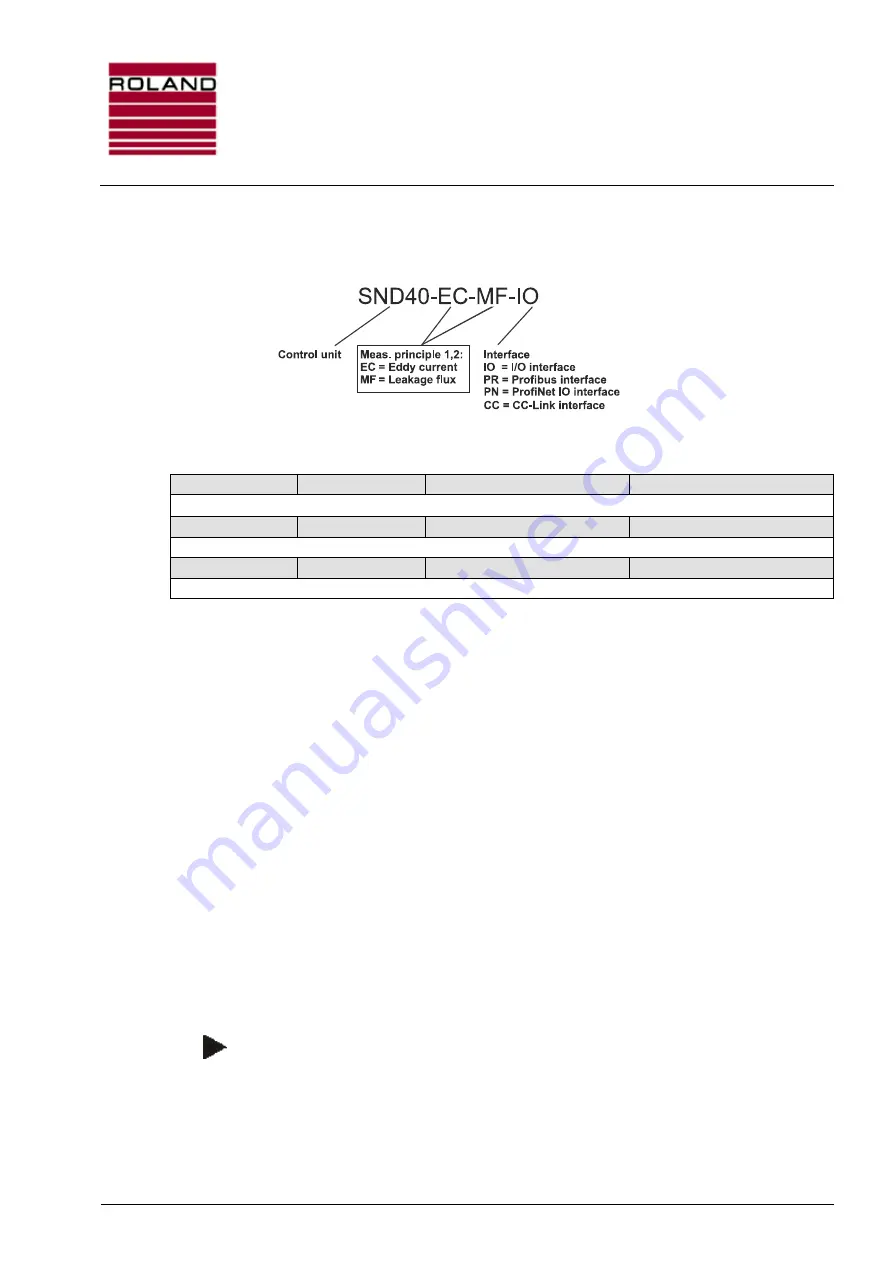
Manual
Weld Seam Detection System R4000 SND40
for Tubes, Cans and Drums
B0059001 / Rev. 2.3
Technical data
ROLAND ELECTRONIC GmbH · Otto-Maurer-Str. 17 · DE 75210 Keltern · Phone +49 (0)7236-9392-0 · Fax +49 (0)7236-9392-33
89
9.1.1 Versions of control unit SND40
The equipment designation is coded as follows:
From this code key the following versions of the control unit result:
SND40-EC-IO
SND40-EC-PR
SND40-EC-PN
SND40-EC-CC
for Eddy current sensors, Eddy current probes, Encircling coil systems
SND40-MF-IO
SND40-MF-PR
SND40-MF-PN
SND40-MF-CC
for Leakage flux sensors
SND40-EC-MF-IO
SND40-EC-MF-PR
SND40-EC-MF-PN
SND40-EC-MF-CC
for Eddy current sensors, Eddy current probes, Encircling coil systems, Leakage flux sensors, Combo sensors
The SND40 control unit is delivered in different versions.
A version property is the measuring principle. Three versions are available:
−
The combination unit
„EC-MF“
works with eddy current
and
leakage flux
principle
−
The eddy current unit „
EC“
works only with the eddy current principle
−
The leakage flux unit
„MF“
works only with the magnetic leakage flux principle
The combined unit "EC-MF" represents with its combined sensors the future-proof solution for
sophisticated Weld Seam Detection. The combination sensors are designed for both eddy current
and magnetic flux leakage. The other two versions "EC" and "MF" are for special cases only. The
matching sensors support only the respective principle.
A specimen examination in the application laboratory of Roland Electronic GmbH clarifies which
measuring principle is suitable for a process-safe detection. We strongly recommend not to make a
selection of one certain measuring principle without a specimen report.
Another important version consists in the interface for control. There is the parallel I/O interface, via
which the signal is exchanged. The usage of a fieldbus interface reduces the amount of wiring.
Additionally, fault messages can be also read out. At present, Profibus DP and Profibus IO are
available.
Note
Using the fieldbus interface may require to pass the time-critical
signal "weld seam detected" through the I/O interface to ensure
accurate positioning. This is a way to avoid unpredictable
latencies of the fieldbus communication, which may manifest in
visible changes of accuracy positioning.