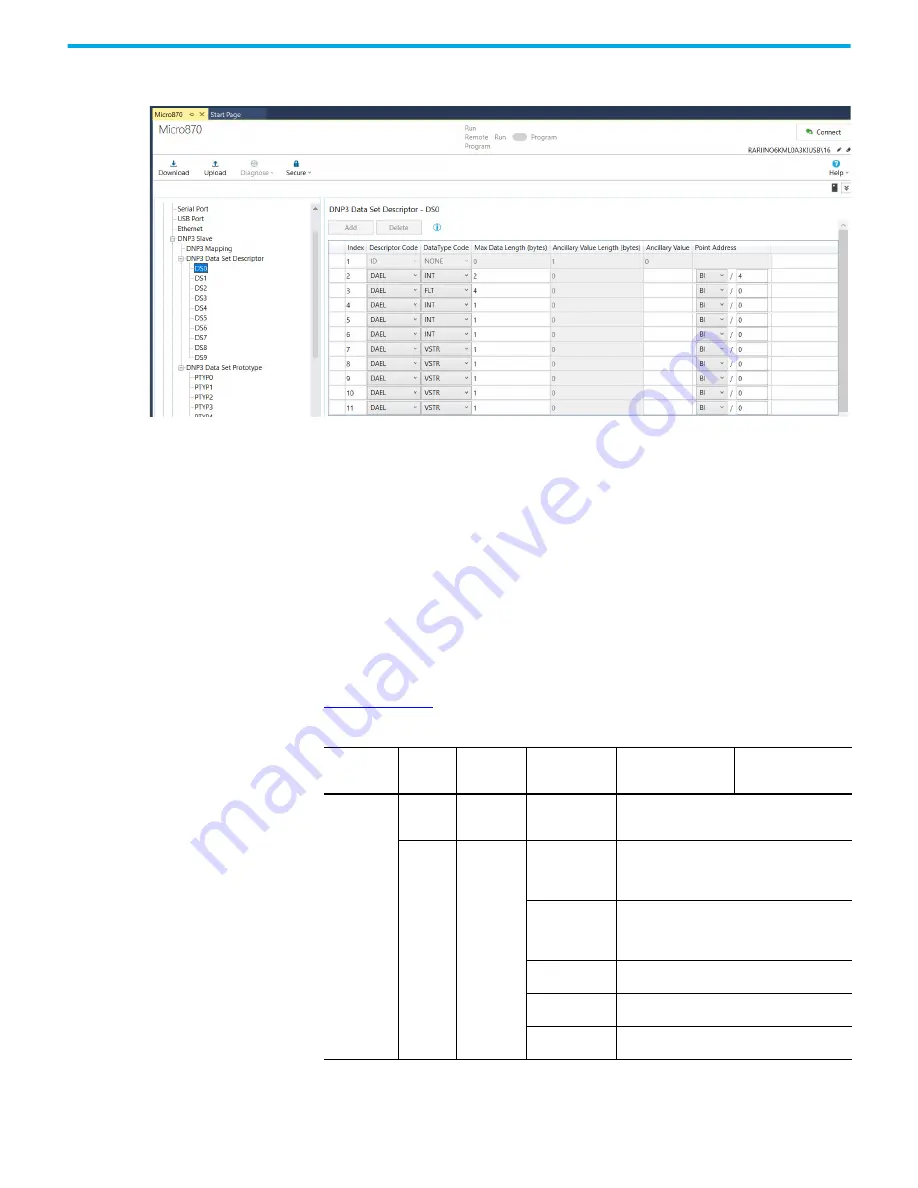
Rockwell Automation Publication 2080-UM002N-EN-E - November 2022
103
Chapter 6 Micro870 Controller Distributed Network Protocol
Descriptor Element Configuration: Each Descriptors element is configured by clicking on the
individual DSX under the DNP3 Data-set Descriptor. Add new index by clicking Add in each DSX.
Descriptor Code: NAME, DAEL, PTYP
Data Type Code: VSTR, UINT, INT, FLT, OSTR, BSTR, TIME
Max Data Length (bytes): 0…255
Ancillary Value: Any string. This can be a binary array or ASCII string, up to 32 bytes.
Point Addressing under Descriptor Element Configuration: Data-Set value for each Data-Set
element is configured by:
• Point Address Type
• Point Index
When these values are configured properly according to the supported data files, the
controller responds with a Group 87, Variation 1 object filled with the value in the data file.
shows the supported data files for the Point Addressing.
Table 9 - Point Address Type — Standard DNP3 Point
Point Address
Type
Data Type
Code
Maximum
Data Length
(bytes)
Point Type
Point Index Low Byte Point Index High Byte
Standard
DNP3 Point
NONE = 0 0
NONE = 0:
No point type is
associated.
0
NONE = 0
UINT = 2
INT = 3
OSTR = 5
BSTR = 6
TIME = 7
0
0, 1, 2, or 4
0, 1, 2, or 4
0…255
0…255
0…6
BI = 1:
Binary input
0…4095 max
When the Data Types other than OSTR and BSTR
are used, the Point Index must be set to a point
offset that is divisible by 16.
B2I = 3:
Double-bit input
0…2047 max
When the Data Types other than OSTR and BSTR
are used, the Point Index must be set to a point
offset that is divisible by 8.
CI = 20:
Counter
0…511 max
AI = 30:
Analog input
0…767 max
BCD = 101:
BCD point
0…255 max
Содержание 2080-L50E-24AWB
Страница 14: ...14 Rockwell Automation Publication 2080 UM002N EN E November 2022 Notes ...
Страница 54: ...54 Rockwell Automation Publication 2080 UM002N EN E November 2022 Chapter 4 Wire Your Controller Notes ...
Страница 128: ...128 Rockwell Automation Publication 2080 UM002N EN E November 2022 Chapter 7 Program Execution in Micro800 Notes ...
Страница 156: ...156 Rockwell Automation Publication 2080 UM002N EN E November 2022 Chapter 8 EtherNet IP Network Notes ...
Страница 198: ...198 Rockwell Automation Publication 2080 UM002N EN E November 2022 Chapter 9 Motion Control Notes ...
Страница 232: ...232 Rockwell Automation Publication 2080 UM002N EN E November 2022 Chapter 11 Controller Security Notes ...
Страница 260: ...260 Rockwell Automation Publication 2080 UM002N EN E November 2022 Chapter 12 Using microSD Cards Notes ...
Страница 266: ...266 Rockwell Automation Publication 2080 UM002N EN E November 2022 Appendix A Modbus Mapping for Micro800 Notes ...
Страница 275: ...Rockwell Automation Publication 2080 UM002N EN E November 2022 275 Appendix B Quickstarts 10 Click Finish to complete ...
Страница 332: ...332 Rockwell Automation Publication 2080 UM002N EN E November 2022 Appendix E PID Function Blocks Notes ...
Страница 352: ...352 Rockwell Automation Publication 2080 UM002N EN E November 2022 Appendix G Connect to Networks using DF1 Notes ...
Страница 388: ...388 Rockwell Automation Publication 2080 UM002N EN E November 2022 Index Notes ...