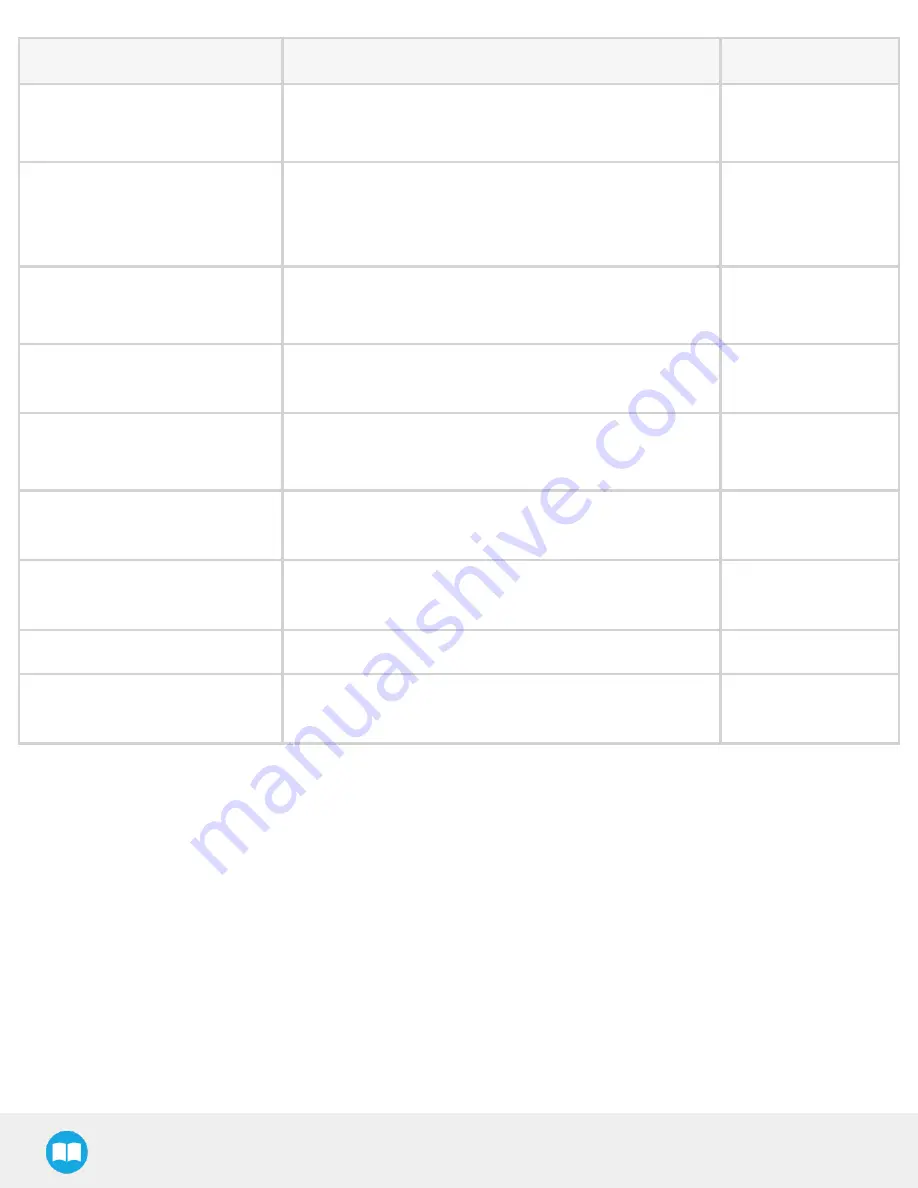
Robotiq CN C M achine Tending Kit Instruction M anual
Item
Description
Ordering Number
2F-85 Fingertips Conversion Kit
l
2 x Fingertip adapters
l
Screws
AGC-TIP-CONV-KIT
Machine Tending Copilot license
dongle
l
1 x USB license dongle
l
1 x Teach Pendant stylus
l
1 x UR wrist axis sticker
CP-MT-ES-UR-KIT
M8 splitter for dual coupling on
UR e-Series
l
Male to 2 female, with 1:1 wiring
l
Screws
ACC-SPLIT-M8-2:1
Adapter plate for dual- gripper
l
1 x 90-degree adapter plate (bolt pattern: ISO 9409-
1:2004 4 X M6 ø 50mm)
AGC-APL-159-002
Replacement Wrist Camera
l
1 x 10-m high flex cable
l
Screws
RWC-CAM-001
Replacement calibration board for
Wrist Camera
1 x calibration board
ACC-CALIB-BOARD
Color background for Wrist Camera
Vision System
1 x colored background
ACC-TEACH-BACK
4-port USB hub splitter
1 x 4-port USB hub splitter
ACC-USB-4-HUB
Replacement softw are license
USB dongle for Wrist Camera
1 x USB dongle
ACC-USB-DONGLE
132
Содержание CNC Machine Tending Kit
Страница 2: ...Robotiq CNC Machine Tending Kit Instruction Manual 2...
Страница 13: ...Robotiq CNC Machine Tending Kit Instruction Manual Fig 1 11 Wrist Camera hardware 13...
Страница 126: ...Robotiq CNC Machine Tending Kit Instruction Manual l Field of view l Part dimensions l Background contrast 126...
Страница 139: ...Robotiq CNC Machine Tending Kit Instruction Manual 1 3 3 IngressProtection Certificate 139...
Страница 141: ......
Страница 143: ...Robotiq CNC Machine Tending Kit Instruction Manual 1 5 2 IngressProtection Certificate 143...