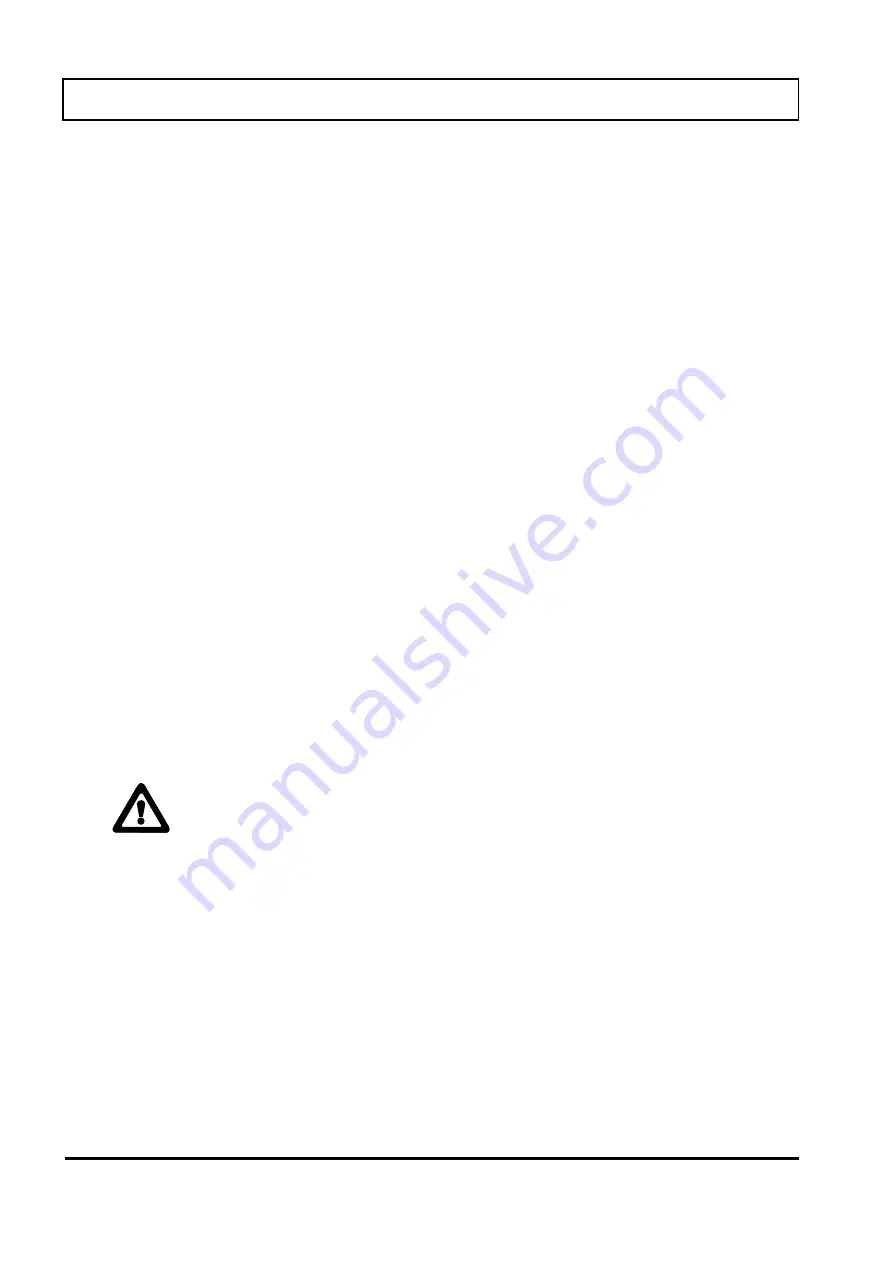
hard surfaces (see photo 7 in the appendix).
The damage described in paragraph D points 1, 2, 3 is not considered fatal for the
track, and the track can continue to be used, even if with gradual and progressive
damage.
The progression of the damage indicated in point 3 leads to the exposure of the
metal cores, and if such exposure covers more than half of the circumference of the
track, then the track should be replaced. It can in any case still be used.
E)
Cracks due to external factors
Cracks on the outside surface of the track (the part in contact with the ground) are
very often due to contact with gravel, sharp stones, sharp materials such as metal
sheet, nails and glass, which cause cuts as shown in photo 10 (see the appendix).
Considering the properties of rubber, this is unavoidable, even if it depends on the
operating conditions.
Cracks on the inside surface of the circumference and on the edge of the rubber are
due to the contact of the track with the structure of the undercarriage or with sharp
concrete edges, as shown in photos 12 and 13 (see the appendix).
The increase in the extent of the cracks is relatively small.
Even if it seems in bad conditions, the track can still be used for heavy‐duty applica‐
tions.
5.3.4
R
EPLACING THE RUBBER TRACKS
The grease contained in the hydraulic track is under pressure.
For this reason, do not loosen the grease valve 1 more than one turn; if the valve is
too loose, the grease may be released due to pressure, placing the operator at risk.
Never loosen the grease nipple 2.
When gravel or mud gets stuck between the cogwheel and the links of the track,
remove it before loosening the track.
O
O
P
P
E
E
R
R
A
A
T
T
I
I
O
O
N
N
A
A
N
N
D
D
M
M
A
A
I
I
N
N
T
T
E
E
N
N
A
A
N
N
C
C
E
E
M
M
A
A
N
N
U
U
A
A
L
L
TP2000
36
MUTP2000171893021216
PERICOLO
DANGER