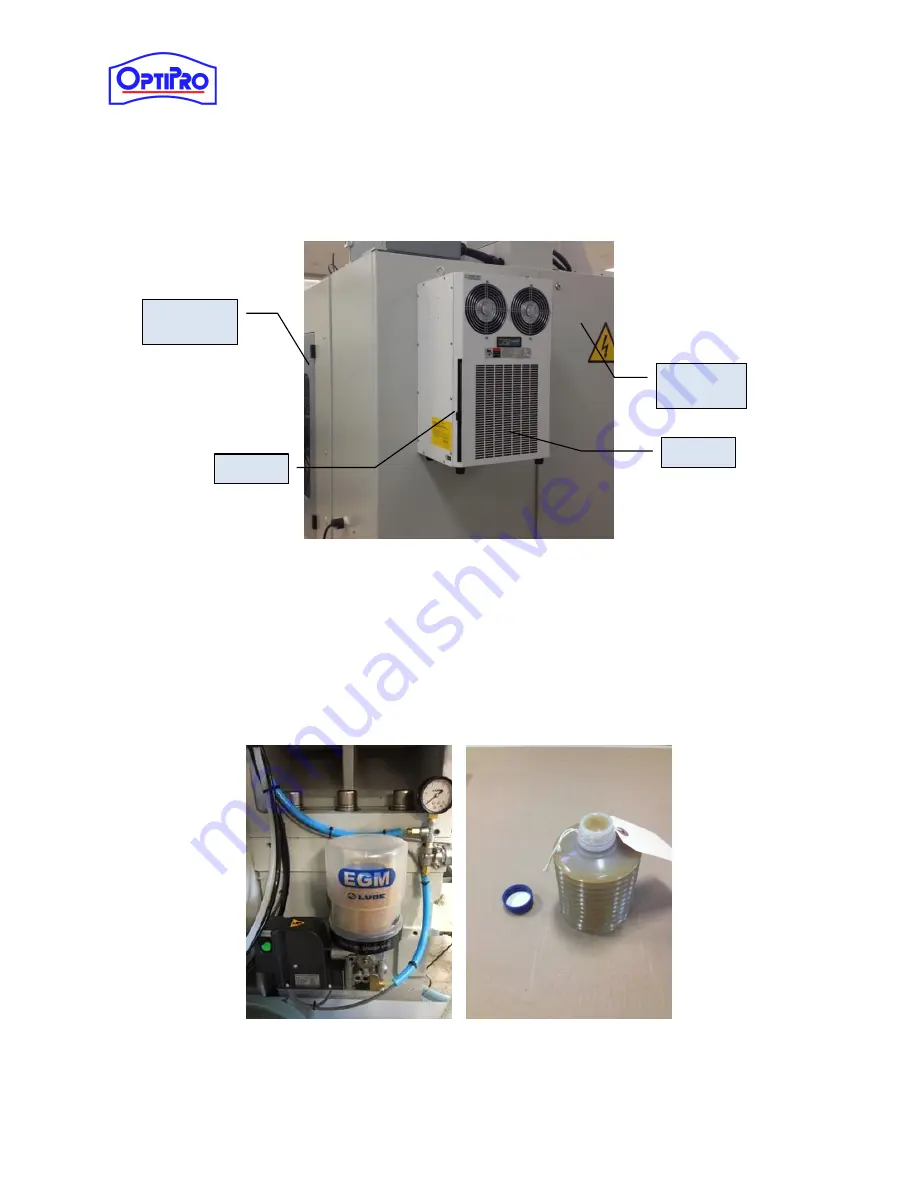
User Manual – ePX 200
OptiPro Systems, LLC.
Page 23 of 60
Last Modified: 7/30/2014
5.7
Electrical Cabinet A/C Unit
The air conditioner attached to the electrical cabinet is factory set to 25°C and is not to be changed.
Doing so could result in damage to the machine.
Figure 5-18: Electrical Cabinet Temperature Control
5.8
Pneumatic Automatic Axis Greaser
The ePX is equipped with an automatic pneumatic greaser that will provide the proper amount of
lubrication to the machine’s X- Y- and Z-axes. Replace the grease cartridge whenever necessary (see
Section 10.3 for part number). The greaser is located on the base of the Z-axis column, near the slurry
valve assembly. The outer plastic cover is attached by a partial-turn twist lock. The grease cartridge
must be unscrewed and the new one screwed in.
Figure 5-19: Pneumatic Automatic Greaser and Replacement Grease Cartridge
A/C Unit
Electrical
Cabinet
Right Side
Machine Door
A/C Filter