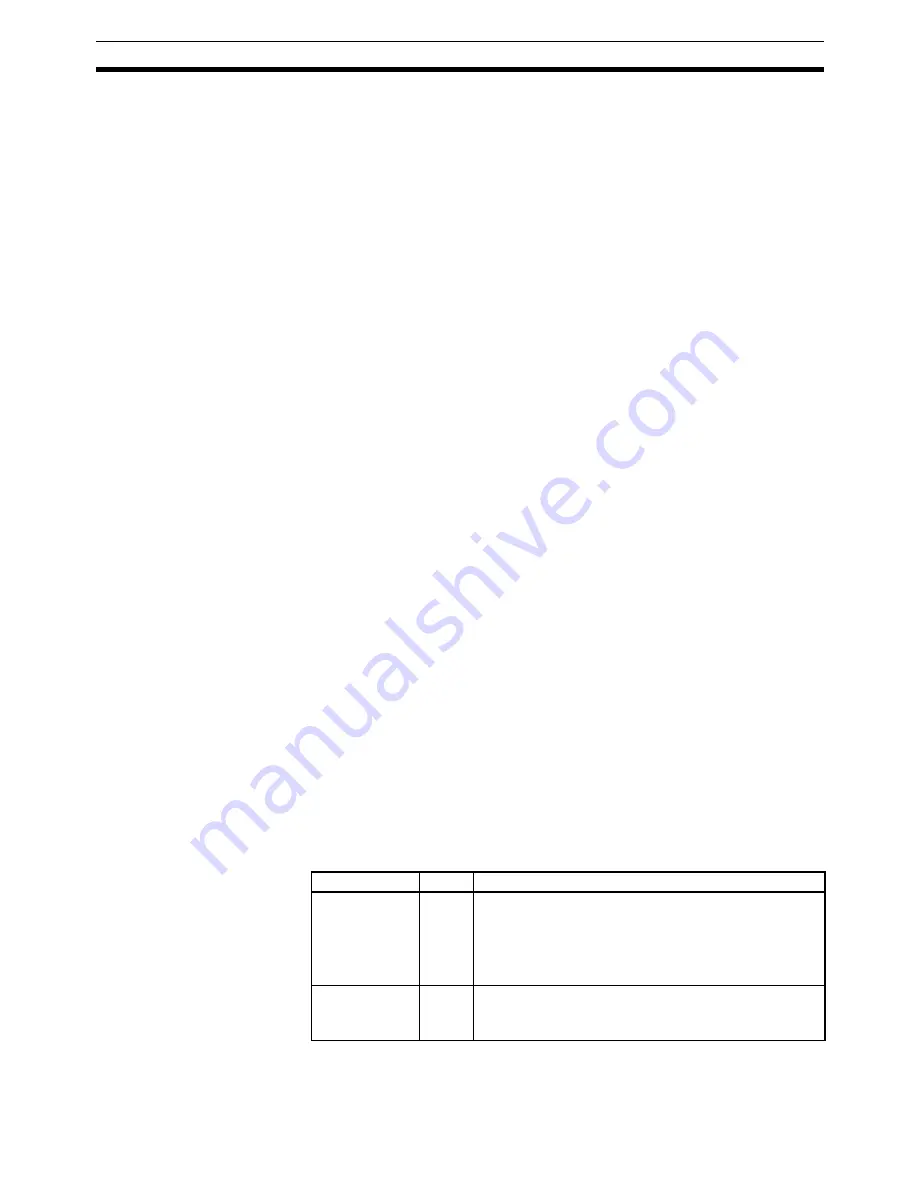
773
Data Control Instructions
Section 3-18
The direction of proportional operation can be designated as either forward or
reverse.
The upper and lower limits of the manipulated variable output can be desig-
nated.
The sampling period can be designated in units of 10 ms (0.01 to 99.99 s), but
the actual PID action is determined by a combination of the sampling period
and the time of PIDAT(191) instruction execution (with each cycle).
The timing of enabling changes made to PID constants can be set to either 1)
the beginning of PIDAT(191) instruction execution or 2) the beginning of PID
instruction execution and each sampling period. Only the proportional band
(P), integral constant (Tik), and derivative constant (Tdk) can be changed
each sampling cycle (i.e., during PID instruction execution). The timing is set
in bit 1 of C+5.
The same words cannot be used to store the PID parameters for more than
one PIDAT(191) instruction. Even if the same parameters are used, use differ-
ent words to store the PID parameters for different PIDAT(191) instructions.
When changing the PID constants manually, set the PID constant change
enable setting (bit 1 of C+5) to 1 so that the values in C+1, C+2, and C+3 are
refreshed each sampling period in the PID calculation. This setting also allows
the PID constants to be adjusted manually after autotuning.
Of the PID parameters (C to C+38), only the following parameters can be
changed when the execution condition is ON. When any other values have
been changed, be sure to change the execution condition from OFF to ON to
enable the new settings.
• Set value (SV) in C
(Can be changed during PID control only. An SV change during autotun-
ing will not be reflected.)
• PID constant change enable setting (bit 1 of C+5)
• P, I, and D constants in C+1, C+2, and C+3
(Changes to these constants will be reflected each sampling period only if
the PID constant change enable setting (bit 1 of C+5) is set to 1.)
• AT Command Bit (bit 15 of C+9)
• AT Calculation Gain (bits 0 to 14 of C+9) and Limit-cycle Hysteresis
(C+10) (These values are read when autotuning starts.)
Note The PIDAT(191) instruction is the same as the PID(190) instruction with the
added autotuning (AT) function, so the PID control operations are identical.
Refer to
3-18-1 PID CONTROL: PID(190)
for details on PID control operations
and examples.
Flags
Name
Label
Operation
Error Flag
ER
ON if the C data is out of range.
ON if the actual sampling period is more than twice the
designated sampling period.
ON if an error occurred during autotuning.
OFF in all other cases.
Greater Than
Flag
>
ON if the manipulated variable after the PID action
exceeds the upper limit.
OFF in all other cases.
Содержание SYSMAC CS Series
Страница 2: ......
Страница 4: ...iv ...
Страница 30: ...xxx ...
Страница 186: ...146 List of Instructions by Function Code Section 2 4 ...
Страница 194: ...154 3 35 4 MOVE BIT MOVBC 568 1273 3 35 5 BIT COUNTER BCNTC 621 1275 3 35 6 GET VARIABLE ID GETID 286 1277 ...
Страница 1320: ...1280 Model Conversion Instructions Unit Ver 3 0 or Later Section 3 35 ...
Страница 1390: ...1350 CJ series Instruction Execution Times and Number of Steps Section 4 2 ...
Страница 1391: ...1351 Appendix A ASCII Code Table ASCII SP Four leftmost bits Four rightmost bits ...
Страница 1392: ...1352 ASCII Code Table Appendix A ...
Страница 1404: ...1364 Revision History ...