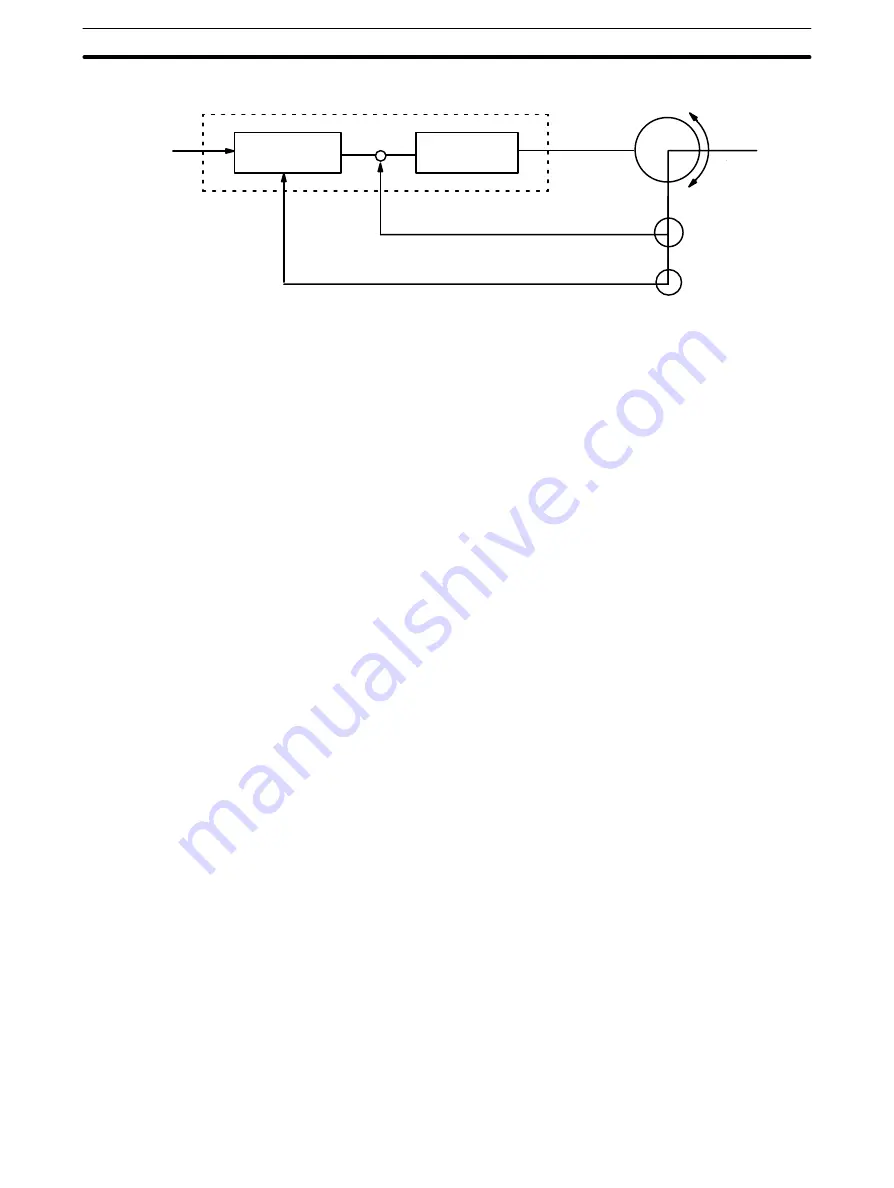
9
Rotary encoder
Tachogenerator
Servomotor driver
Servomotor
Position output
Error counter
Power amplifier
Position feedback (feedback pulses)
Speed feedback
Target position
1, 2, 3... 1.
First, the target position is transmitted to the error counter in units of en-
coder pulses. The servomotor driver must be able to handle digital input.
2.
The motor rotates at a speed corresponding to the speed voltage. The
rotary encoder connected to the motor axis rotates in sync with the mo-
tor, generates feedback pulses, and decrements the error counter.
3.
Consequently, the encoder rotation is equivalent to the target position,
and the motor stops rotating when the error counter count and the
speed voltage become zero.
4.
While the motor is stopped, the rotary encoder constantly maintains the
stopped position through correction. In the event that the motor axis
moves slightly, the error counter receives a feedback pulse from the
rotary encoder, causing a rotation voltage to be emitted in the reverse
direction from which the rotary encoder moved. This makes the motor
rotate toward its original position. This operation is called servolock or
servoclamp.
5.
In order to execute positioning with acceleration and deceleration, target
positions are set consecutively in the error counter for processing.
6.
The target position becomes the count for the error counter and controls
the motor by conversion to a speed voltage for the servomotor driver.
The position thus equals the total count of target positions and the
speed will depend on the target position per unit time.
Positioning System Principles