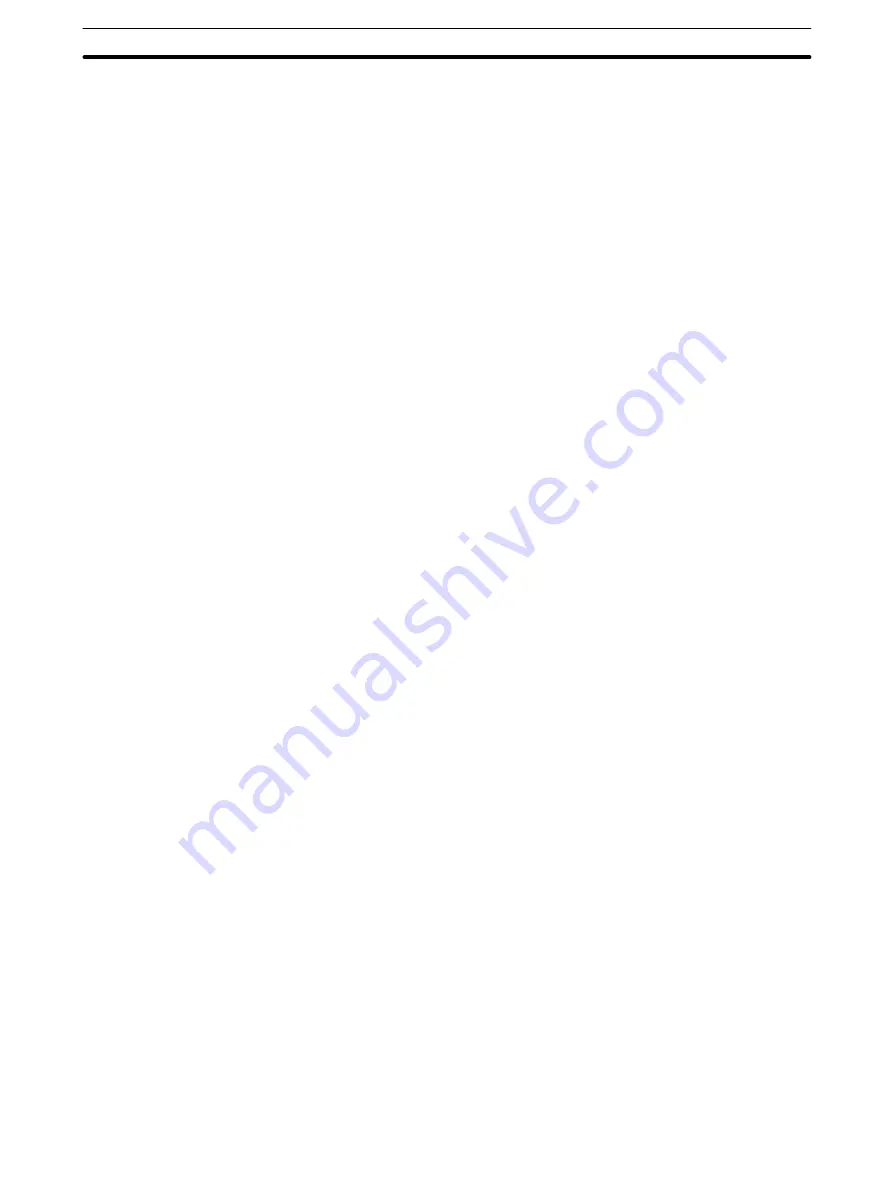
2
1–1
Features
The pulse train output can be easily connected to either of the following de-
vices:
1.
Stepping motor driver
2.
Servomotor driver designed for pulse train input
The Position Control Unit is designed to control a single axis and is capable
of controlling speeds and positions in accordance with data recorded in the
DM area of the C200H PC.
Three commands enable manual positioning control: HIGH-SPEED JOG,
LOW-SPEED JOG, and INCH.
PCU positioning actions, speeds, and other data can be stored in the DM
area or other areas of the PC and quickly transferred to the PCU via a
TRANSFER DATA command. This effectively increases the amount of
memory available to the PCU.
The TRANSFER DATA command can also be used to change the present
position to any desired value, including 0 (origin), any time the Position Con-
trol Unit is not outputting pulses.
The present position can be written into the memory of the PC as positioning
data whenever pulses are not being output.
The C200H-NC112 Position Control Unit can be operated in any of four
modes, which are selected via the mode switch on the Unit. Mode 0 is equiv-
alent to the C200H-NC111 Position Control Unit; the other three are for use
with servomotor drivers. Mode 3 is designed especially for use with the OM-
RON R88D-EP/SR (marketed in Japan) servomotor driver.
The method employed to detect the origin may be selected via the rear-panel
DIP switch.
The speed range has been expanded to enable settings anywhere from 1 to
250,000 pps (compared with 1 to 99,990 for the NC111). In addition, acceler-
ation and deceleration speeds between 2 and 2,000 pps/ms are now possi-
ble (compared with 1 to 999 pps/ms for the NC111).
The minimum switching capacity has been increased from 2.5 mA (in the
NC111) to 7 mA at 5 VDC.
In the NC111, the speed number currently being executed is always increm-
ented by one to obtain the subsequent target speed, but in the NC112, the
next speed number can be set in the DM area of the C200H PC. If desired,
speed numbers may be allowed to increment one by one as in the NC111.
Acceleration and deceleration have been made smoother by reducing each
incremental step from the NC111’s 10 ms to 4 ms.
In addition to the five completion codes possible with the NC111, the NC112
allows for a sixth, i.e., “extended with positioning”.
Applicable Motor Drivers
Number of Control Axes
and Controlling Capacity
Manual Operation
Data Transfer
Establishing Position
Teaching
Operation in Four Modes
Choice of Origin Detection
Method
Expanded Speed Range
Greater Switching Capacity
Optional Speed Numbers
Smoother Acceleration and
Deceleration
More Completion Codes
Features