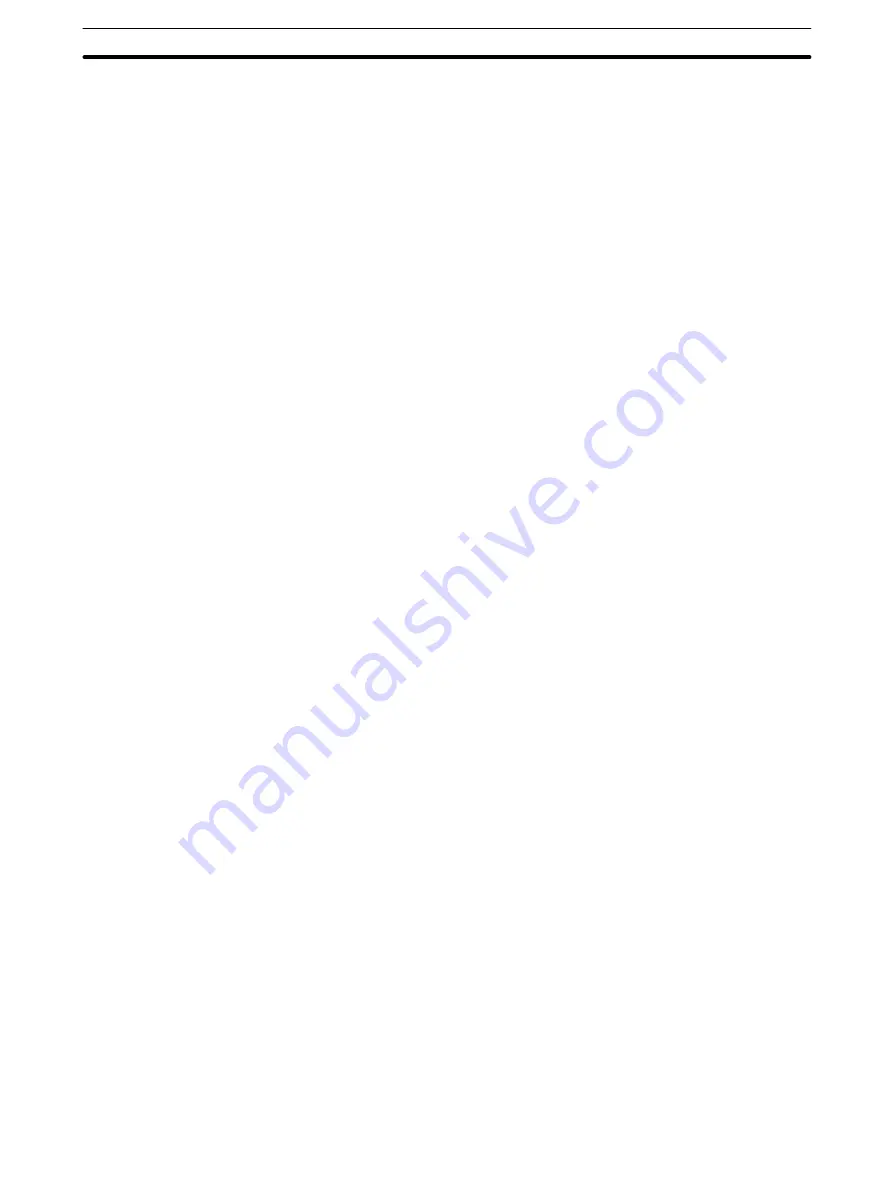
4
data stored in the DM area of the PC. This data includes directions, speeds,
positions, and other information necessary for effective control. Before the
Position Control Unit can be operated, you must first input the essential data.
This is generally done via the Programming Console, although you can also
input data with the TEACH command.
The way in which the Position Control Unit makes use of this data is deter-
mined by the program in the PC. The program does not control all of the Po-
sition Control Unit’s operations directly, but rather, executes the Unit’s com-
mands by turning command bits ON and OFF. The commands control such
functions as the starting and stopping of positioning, returning to the origin,
and so on. (The origin is simply the point which is designated as 0 at any giv-
en time.) Thus, while the Position Control Unit functions as an integral part of
your overall control system, it also exercises a good deal of autonomy. This
capability is essential to the concept of distributed control, whereby control of
each portion of an automated system is located near the devices actually
being controlled.
The fundamental unit of positioning is the positioning action. A particular po-
sitioning action moves the workpiece along the positioning axis in a direction,
at a speed, and to a position determined by the data which has previously
been set. The positioning action begins when the appropriate command bit
(START) is turned ON by the program.
A single positioning action may be executed by itself, or a bank of several
positioning actions may be executed in sequence. A particular bank of ac-
tions may be repeated again and again. Before beginning execution of posi-
tioning actions, it is necessary to define the origin as a reference point by, for
example, executing ORIGIN SEARCH.
1–4
I/O Configuration
The basic I/O configuration is shown on the following page. Position Control
Unit outputs are connected to a motor driver, either for a stepping motor or
for a servomotor (AC or DC) capable of receiving pulse train inputs. The Unit
is controlled by inputs from devices and/or a control panel. It, in turn, outputs
pulse trains and direction signals to control the motor driver.
The motor driver controls either a stepping motor or a servomotor, depending
on whether you choose to employ an open-loop or semiclosed-loop system.
(See
Section 1–5). The stepping motor or servomotor controls some type of
positioning device (such as a feed screw). An independent power supply
must be used for the motor driver. Some configurations also require an Input
Unit on a C200H Rack to control the motor driver.
A maximum of 10 Special I/O Units, including Position Control Units,
High-Speed Counters, etc., can be mounted under the same PC, regardless
of whether they are on the CPU Rack, an Expansion I/O Rack, or a Slave
Rack. No more than four of these can be mounted onto any one Slave Rack.
Refer to the
Remote I/O System Operation Manuals for further restrictions.
The Position Control Unit can be mounted to any slot on any Rack except for
the two rightmost CPU Rack slots. Mounting the Unit to either of these slots
will prevent you from mounting devices directly to the CPU. The back-panel
DIP switch must be set before the Unit is mounted. This switch is inaccessi-
ble on a mounted Unit. (See
Section 2–1.)
Although Unit operation can be indirectly controlled from a host computer,
Remote I/O Master Unit, or other control system or peripheral device, direct
Maximum Number of
Special I/O Units per PC
Mounting Location
Basic Configuration
I/O Configuration