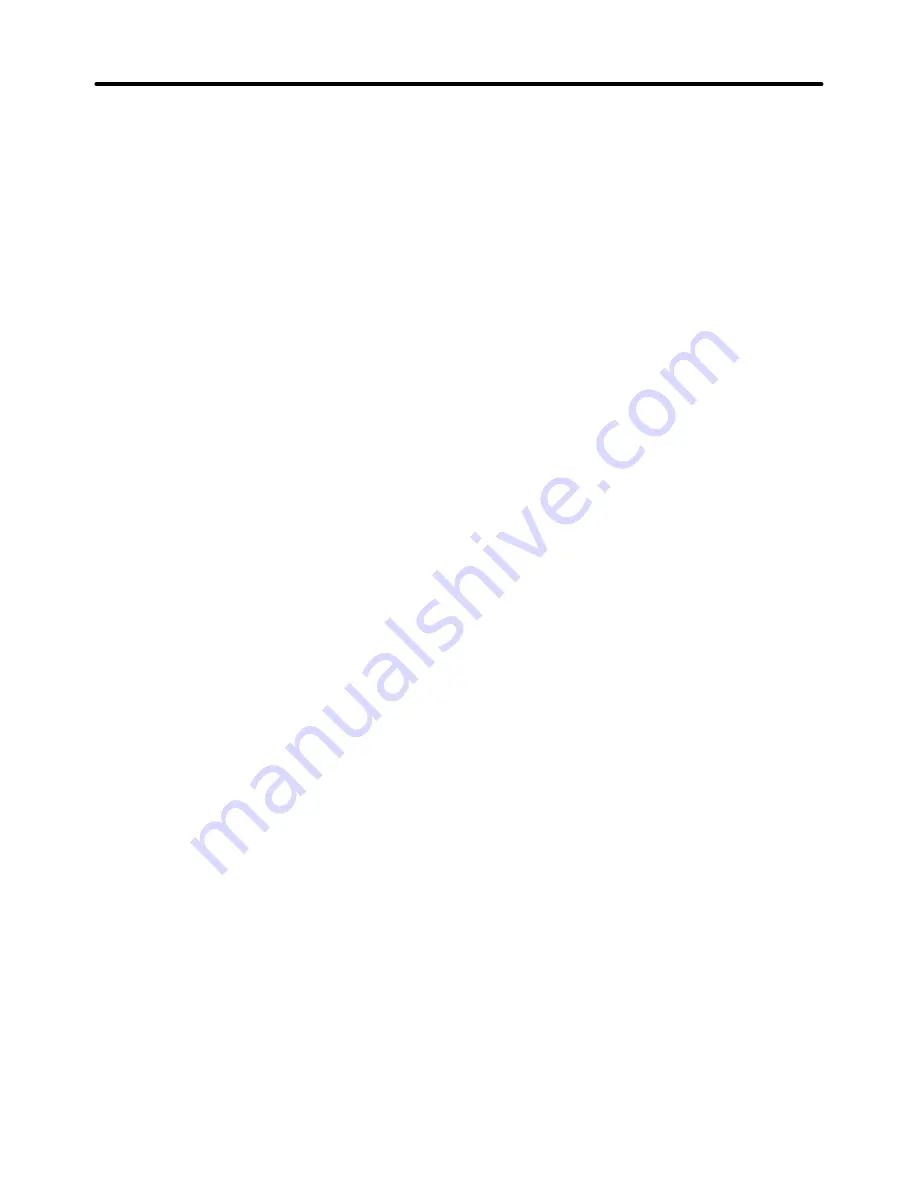
8-17
•
V/f Control Limit
Unlike vector control, the output torque of the Inverter in V/f control is low at low frequencies. Con-
sider the use of vector control if higher output torque at low frequencies is required.
8-2-5 Speed Accuracy of the Inverter Rotating at High Speed in
Vector Control is Low
•
The rated motor voltage is high.
The maximum output voltage of the Inverter is determined by the voltage of input into the Inverter. If
the input is at 200 V AC, for example, the maximum output voltage will be 200 V AC. The speed
precision of the Inverter will drop if the output voltage designated by vector control has exceeded the
maximum output voltage of the Inverter.
Use a motor with a lower rated voltage (e.g., a dedicated motor for vector control use).
8-2-6 Motor Deceleration Rate is Low
•
Stall prevention during deceleration is set.
When connecting the Braking Resistor Unit or a braking resistor as a braking option, set n092 for
Stall prevention during deceleration to 1 so that stall prevention will be disabled. If n092 is set to 0
(default setting), the Braking Resistor Unit or a braking resistor connected will not be used. There-
fore, there will be no reduction in the deceleration time.
•
The deceleration time setting is too long.
Check the deceleration time settings in n020 and n022.
•
Motor torque is insufficient.
If the parameter constants are correct and there is no overvoltage fault, the power of the motor will
be limited.
Consider increasing the motor capacity.
•
The Inverter in vector control is restricted by the torque compensation limit.
If the torque compensation limit in n109 is set to a value that is too small, the motor torque will be
limited to a low value and sufficient torque will not be available.
If no torque restriction is required, set the parameter to a range from 150% (default setting) to 200%.
8-2-7 Vertical-axis Load Drops when Brakes are Applied
•
The sequence is incorrect.
The Inverter goes into DC braking status for 0.5 s after deceleration is completed. This is the default
setting.
Check the sequence to make sure that the brake is applied with DC braking status or adjust the
value n090 for DC injection control time.
•
The DC injection braking is insufficient.
If the DC braking power is insufficient, adjust the value in n089 for DC injection control current.
•
An inappropriate brake is being used.
Use a brake intended for braking rather than holding.
Maintenance Operations
Chapter 8
Содержание SYSDRIVE 3G3MV-A2001
Страница 1: ...Cat No I527 E1 04 USER S MANUAL SYSDRIVE 3G3MV Multi function Compact Inverter...
Страница 2: ......
Страница 3: ...USER S MANUAL Multi function Compact Inverter SYSDRIVE 3G3MVSERIES...
Страница 18: ......
Страница 23: ...Chapter 1 Overview 1 1 Functions 1 2 Nomenclature 1 3 New Features 1...
Страница 32: ......
Страница 33: ...Chapter 2 Design 2 1 Installation 2 2 Wiring 2...
Страница 74: ......
Страница 75: ...Chapter 3 Preparing for Operation and Monitoring 3 1 Nomenclature 3 2 Parameter Copy and Verify Function 3...
Страница 93: ...Chapter 4 Test Run 4 1 Procedure for Test Run 4 2 Operation Example 4...
Страница 102: ......
Страница 142: ......
Страница 242: ......
Страница 268: ......
Страница 269: ...Chapter 9 Specifications 9 1 Inverter Specifications 9 2 Option Specifications 9...
Страница 293: ...9 25 D 3G3MV PRS2030V PRS3020V Four M4 holes for Inverter mounting use Three 5 dia holes Specifications Chapter 9...
Страница 294: ...9 26 D 3G3MV PRS2050V Four M5 holes for Inverter mounting use Three 6 dia holes Specifications Chapter 9...
Страница 297: ...9 29 D 3G3MV PRS1040V Three 5 dia holes Four M4 holes for Inverter mounting use Specifications Chapter 9...
Страница 303: ...Chapter 10 List of Parameters 10...
Страница 337: ...Chapter 11 Using the Inverter for a Motor 11...
Страница 343: ......
Страница 344: ...I527 E1 04...