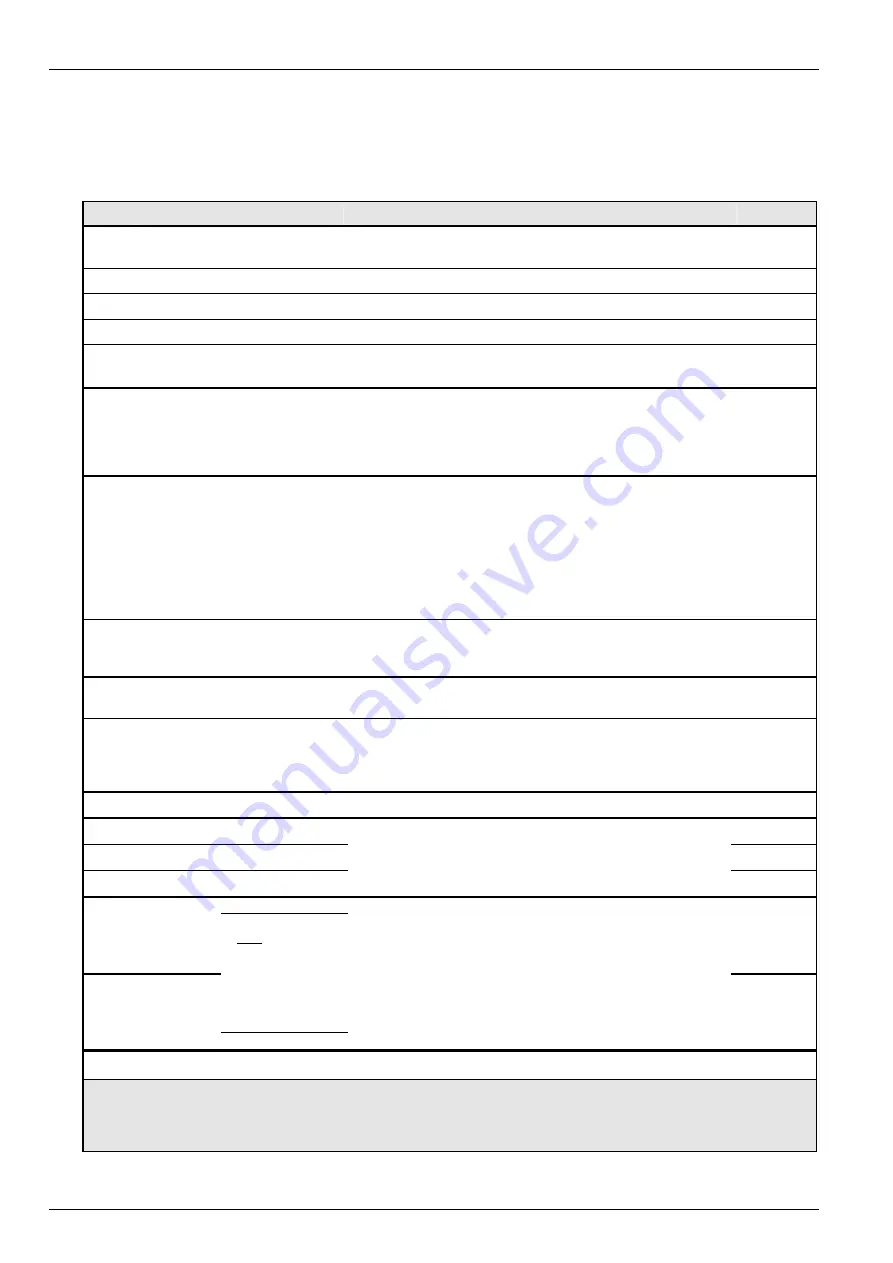
NORDAC SK 5xxE Manual
96
Subject to technical alterations
BU 0500 GB
Impulse input functions: 2...22kHz (only for DIN2 and DIN3 or 4)
For these functions the particular input evaluates the impulse frequency present. The frequency range 2kHz to 22kHz
thereby covers the range of values from 0 to 100%. The inputs operate up to a maximum impulse frequency of 32kHz. The
voltage level may be between 15V and 24V and the switch-on cycle between 50 and 80%.
Value
Function
Description
Signal
26
Torque current limit
2
Adjustable load limit, the output frequency is reduced when it
is reached.
→
P112
Impulse
27
Actual PID frequency
2 3
Possible feedback of actual value for the PID controller
Impulse
28
Frequency addition
2 3
Addition to other frequency setpoint values
Impulse
29
Frequency subtraction
2 3
Subtraction from other frequency setpoint values
Impulse
33
Current limit
2
Based on the set current limit (P536), this can be changed
using the digital/analog input.
Impulse
34
Maximum frequency
2 3
The maximum frequency of the FI is set in the analog range.
100% corresponds to the setting in parameter P411. 0%
corresponds to the setting in parameter P410. The values for
the min/max output frequency (P104/P105) cannot be
exceeded or undershot.
Impulse
35
Actual frequency of PID controller
limited
2 3
Needed to build up a control loop. The digital/analog input
(actual value) is compared with the setpoint (e.g. other analog
input or fixed frequency). The output frequency is adjusted as
far as possible until the actual value equals the setpoint. (see
control variables P413 – P416)
The output frequency cannot fall below the programmed
minimum frequency value in parameter P104. (No rotation
direction change!)
Impulse
36
Actual frequency of PID controller
monitored
2 3
As function 35, >Actual frequency PID< but the FI switches
the output frequency off when the >Minimum frequency<
P104 is reached.
Impulse
37
Torque servo mode
2
The motor torque can be set or limited via this function in
Servo mode.
Impulse
38
Torque precontrol
2
Function that enables a value for the anticipated torque
requirement to be entered in the controller (interference factor
switching) This function can be used to improve the load take-
up of lift equipment with separate load detection.
→
P214
Impulse
39
Multiplication
3
This factor multiplies the master setpoint value.
Impulse
40
PI process controller actual value
Impulse
41
PI process controller setpoint
Impulse
42
PI process controller lead
As for P400 = 14-16
further details regarding the process controller can be found in
Section 8.2
Impulse
43
Track A
HTL
encoder
Impulse
<10kHz
44
Track B
HTL
encoder
This function can
only be used for
the digital inputs 2
(P421) and 4
(P423)
only SW1.5 and
above
A 24V HTL encoder can be connected to
DIN 2
and
DIN 4
in
order to measure the speed. The maximum frequency at the
DIN is limited to 10kHz. Accordingly, a suitable encoder (low
pulse number) or suitable mounting (slow speed) SHOULD
BE USED.
The direction of counting can be changed by exchanging the
functions on the digital inputs.
Further settings are in P461, P462, P463.
Impulse
<10kHz
2
Also effective for Bus control (RS232, RS485, CANbus, CANopen, DeviceNet, Profibus, InterBus, AS-Interface)
3
The limits of these values are set by the parameters >Minimum frequency auxiliary setpoints< P410 and >Maximum frequency
auxiliary setpoints< P411.