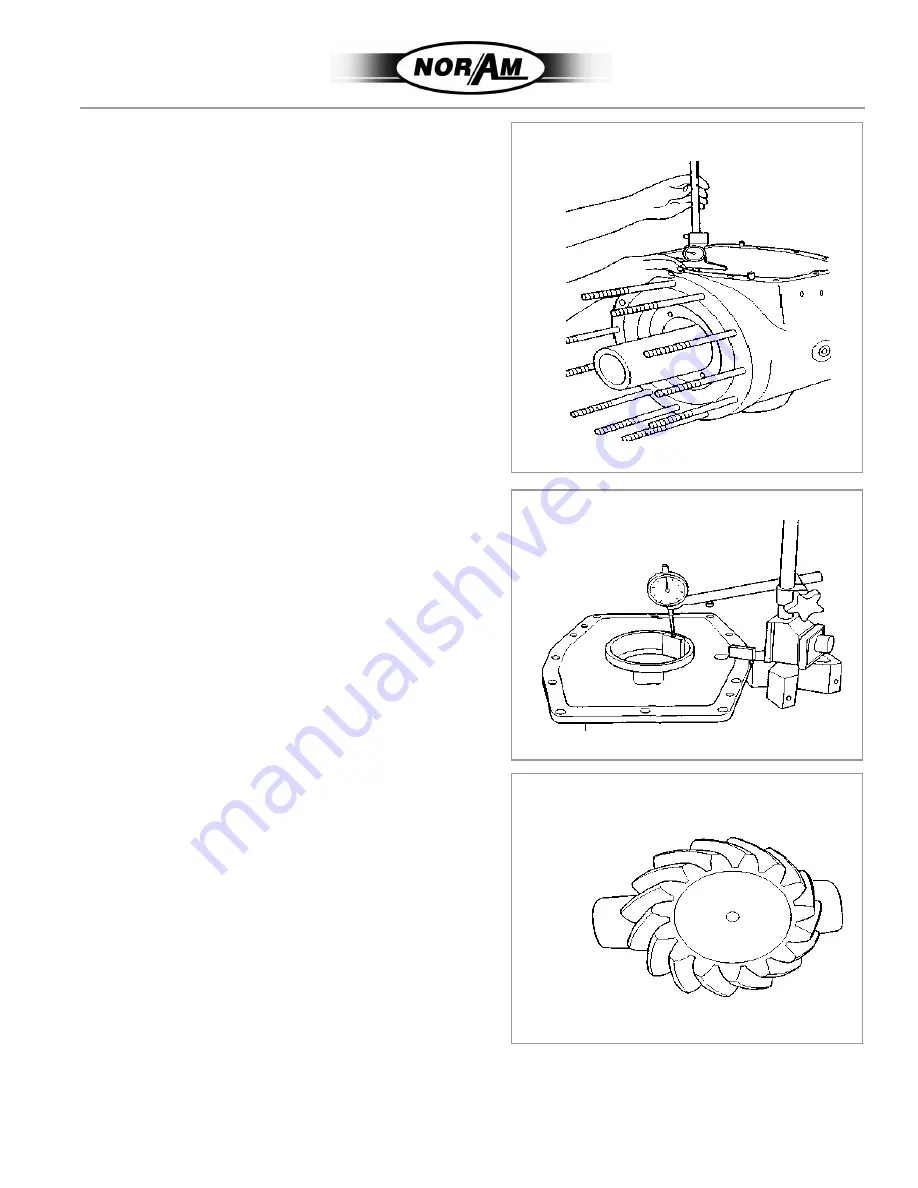
65E Turbo Motor Grader
Service Manual
Service 1.00_2006.03
Section 5
Rear Axle and Tandems
5-41
NOTE:
Some dimensions should be recorded prior to
assembly to determine thickness of shims for axial
position of bevel pinion.
Step 10:
Computation of dimension from seating surface
of pinion support to ring gear axis on center section
case, "A". Place a cylinder of know diameter "D" on
differential support seats. Measure dimension from
upper edge of cylinder to seating surface of pinion, "B".
A = B + D - DIFFERENTIAL SEAT RADIUS
Step 11:
Measure depth of under pinion bearing seat on
pinion support with respect to seating surface of
support on center section case, "C". Now we are able to
determine the distance from ring gear axis to seating
surface of pinion under head bearing on support, "E".
E = A + C
Step 12:
A number with a sign (+ -) is printed on the front
face of each bevel pinion head. Such a number is
expressed in tenth of millimeter and indicates the
displacement from the theoretical dimension from
pinion under head surface to ring gear axis,
i.e.: -1 = -0.1 mm. Therefore, the true dimension, "F",
will be (pinion theoretical dimension 162 mm).
F = 162-0.1 = 161.9
Содержание 65E Turbo
Страница 6: ...Service Manual Section 1 Engine Service 1 00_2006 03 ...
Страница 7: ......
Страница 30: ...Service Manual Section 2 Operator s Platform and Controls Service 1 00_2006 03 ...
Страница 31: ......
Страница 45: ...65E Turbo Motor Grader Service Manual Section 2 Operator s Platform and Controls Service 1 00_2006 03 2 4 Cab ...
Страница 47: ...65E Turbo Motor Grader Service Manual Section 2 Operator s Platform and Controls Service 1 00_2006 03 2 6 ...
Страница 76: ...Service Manual Section 3 Transmission Service 1 00_2006 03 ...
Страница 77: ......
Страница 122: ...ZF Friedrichshafen AG description of fault codes for ERGO Control 97 09 18 Seite 29 von 30 ...
Страница 124: ......
Страница 125: ......
Страница 126: ......
Страница 127: ......
Страница 128: ......
Страница 129: ......
Страница 130: ......
Страница 131: ......
Страница 132: ......
Страница 133: ......
Страница 134: ......
Страница 135: ......
Страница 136: ......
Страница 137: ......
Страница 138: ......
Страница 139: ......
Страница 140: ......
Страница 141: ......
Страница 142: ......
Страница 143: ......
Страница 144: ......
Страница 145: ......
Страница 146: ......
Страница 147: ......
Страница 148: ......
Страница 149: ......
Страница 150: ......
Страница 151: ......
Страница 152: ......
Страница 153: ......
Страница 154: ......
Страница 155: ......
Страница 156: ......
Страница 157: ......
Страница 158: ......
Страница 159: ......
Страница 160: ......
Страница 161: ......
Страница 162: ......
Страница 163: ......
Страница 164: ......
Страница 165: ......
Страница 166: ......
Страница 167: ......
Страница 168: ......
Страница 169: ......
Страница 170: ......
Страница 171: ......
Страница 172: ......
Страница 173: ......
Страница 174: ......
Страница 175: ......
Страница 176: ......
Страница 177: ......
Страница 178: ...Order No 5871 146 002 ZF ERGOPOWER 6 WG 115 ZF Passau GmbH Donaustr 25 71 D 94 034 Passau ...
Страница 306: ...Service Manual Section 4 Front Axle Service 1 00_2006 03 ...
Страница 307: ......
Страница 315: ...65E Turbo Motor Grader Service Manual Section 4 Front Axle Service 1 00_2006 03 4 x This page intentionally left blank ...
Страница 347: ...65E Turbo Motor Grader Service Manual Section 4 Front Axle Service 1 00_2006 03 4 30 This page intentionally left blank ...
Страница 348: ...Please reference Eaton Publication C STCU TS002 pdf on this CD for further information on the Steering Control Unit ...
Страница 349: ...Service Manual Section 5 Rear Axle and Tandem Service 1 00_2006 03 ...
Страница 350: ......
Страница 421: ...Service Manual Section 6 Electrical Service 1 00_2006 03 ...
Страница 422: ......
Страница 430: ...65E Turbo Motor Grader Service Manual Section 6 Electrical Service 1 00_2006 03 6 x This page intentionally left blank ...
Страница 453: ...65E Turbo Motor Grader Service Manual Service 1 00_2006 03 Section 6 Electrical 6 21 Instrument Panel Group ...
Страница 456: ...65E Turbo Motor Grader Service Manual Section 6 Electrical Service 1 00_2006 03 6 24 Starter Relay Neutral Start Relay ...
Страница 457: ...65E Turbo Motor Grader Service Manual Service 1 00_2006 03 Section 6 Electrical 6 25 Brake Differential Pressure Switch ...
Страница 460: ...65E Turbo Motor Grader Service Manual Section 6 Electrical Service 1 00_2006 03 6 28 Injection Pump Relay ...
Страница 461: ...65E Turbo Motor Grader Service Manual Service 1 00_2006 03 Section 6 Electrical 6 29 Park Brake Switch ...
Страница 470: ......
Страница 471: ...Service Manual Section 7 Hydraulics Service 1 00_2006 03 ...
Страница 472: ......
Страница 480: ...65E Turbo Motor Grader Service Manual Section 7 Hydraulics Service 1 00_2006 03 7 x This page intentionally left blank ...
Страница 484: ...65E Turbo Motor Grader Service Manual Section 7 Hydraulics Service 1 00_2006 03 7 2 This page intentionally left blank ...
Страница 485: ...65E Turbo Motor Grader Service Manual Service 1 00_2006 03 Section 7 Hydraulics 7 3 HYDRAULIC SCHEMATIC ...
Страница 576: ...Please reference Eaton Publication 06 623 pdf on this CD for further information on the L2 Series Gear Pump ...
Страница 577: ...Please reference Eaton Publication 07 145 pdf on this CD for further information on the T Series Geroler Motor ...
Страница 578: ...Service Manual Section 8 Moldboard and Implement Service 1 00_2006 03 ...
Страница 579: ......