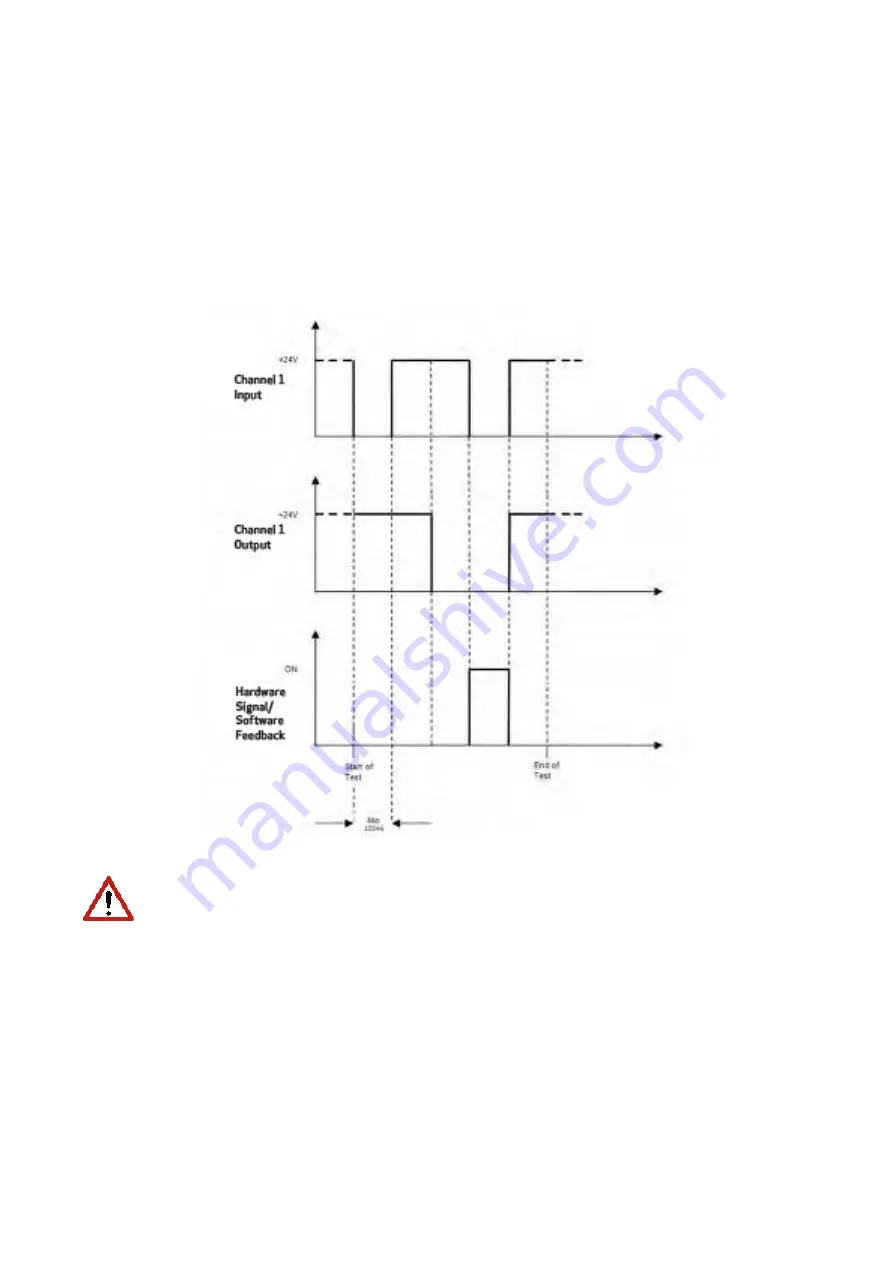
7.8. Safe Torque Off
Installation and maintenance procedures
The following installation and maintenance procedures must always be carried out as indicated by qualified personnel who
adopt the safety measures required by current regulation:
•
on start-up
•
on restart in case a fault has been detected and removed
•
in any case at least every 8 hours
Run the activation / deactivation switching sequence shown in the figure below by sup 24Vdc and 0V on the two input
channels connected to connector X1 and perform a plausibility check with the monitoring signals:
•
Hardware feedback : on connector X1 check closed electrical contact (ON) or open contact (OFF)
•
Software feedback :
check the value of the "INTERLOCK STATUS" parameter object 60FD (digital inputs) bit3 defined by
the IEC61800-7-201 standard, CIA 402
•
Stop Category1
Disable the protection devices, for example opening the guards while the motor is operating, and check that the
motor stops.
•
If the stop is category 1 according to EN 60204-1: 2006, check that the motor has stopped in a controlled mode,
and that the Safe Torque Off function is enabled after the stop. This must not cause hazardous situations.
7.10. Assembly and production testing
The Safe Torque Off (STO) circuit is assembled and tested at Moog-Casella.
7.11. Identification of the STO function on the drive's side plate
The new Safe Torque Off (STO) circuit is identified by the legend “Safe Torque Off” on the plate.
Mandatory sequence of STO circuit test
WARNING
If one of the above conditions is not met, the STO function may not be used. After remedying the fault,
repeat the procedure.
AVERTISSEMENT
Si l'une des conditions précédentes n'est pas remplie, la fonction STO ne peut pas être utilisée. Après la
panne est réparée, répétez la procédure.
DR2020
MAR2-E-191
89