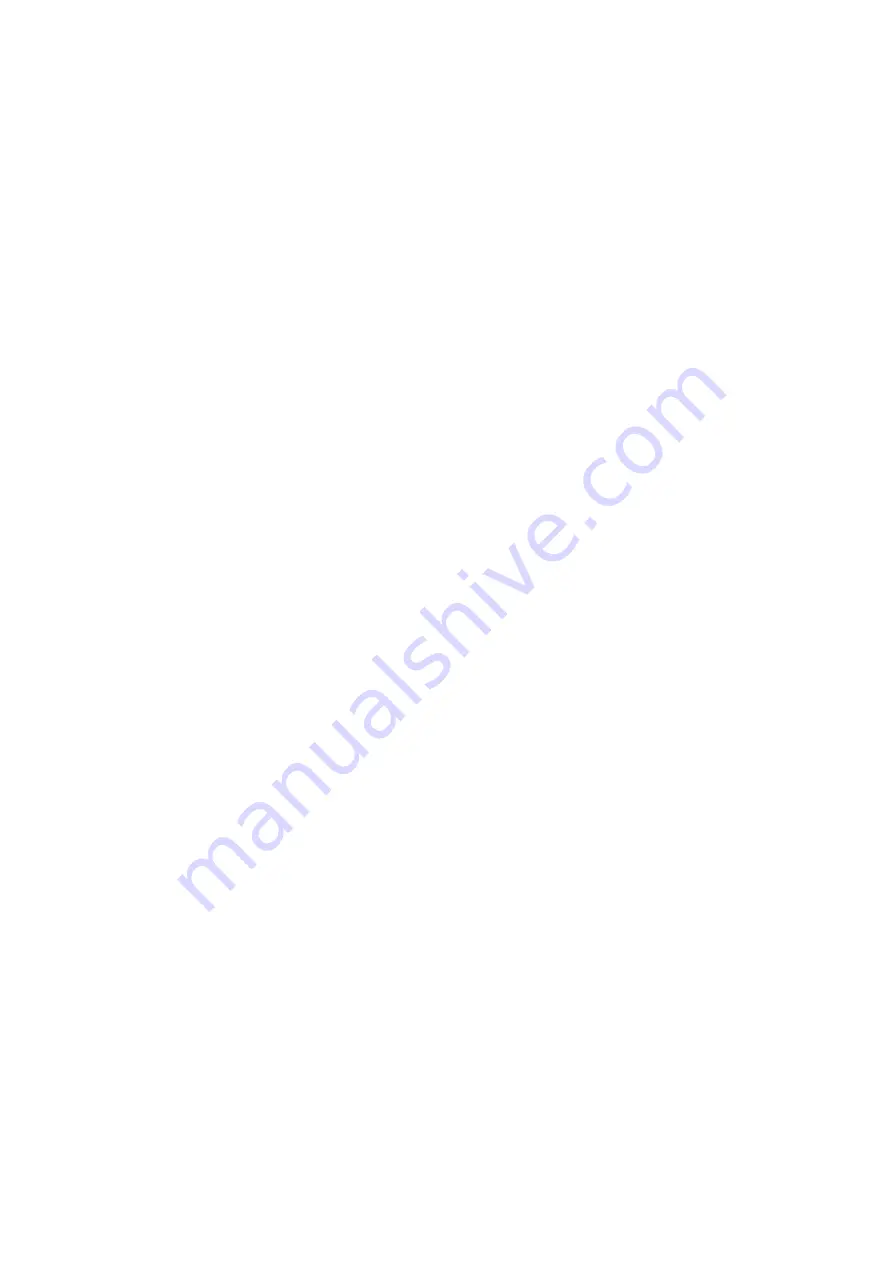
The subsystems:
• A1 safety PLC has a PL of “e”
• The DM2020 drive (STO circuit) has a PL of “e”
The safety system can attain a PL of “e”, and a category of 4.
According to UNI EN ISO 62061:2005, the subsystem relative to input and output devices can attain a PL of “3” because:
• All safety-related devices have a PFHd < 10
-7
The subsystems:
• The A1 safety PLC has a SIL of 3
• The DM2020 drive (STO circuit) has a SIL of 3
The safety system may attain a SIL of 3.
Requirements of the example
• Before activating the STO function, the motor must be stopped while maintaining the power supply (controlled stop)
• The delay of the A1 outputs that activate the Q1 and Q2 contactors must be > T (general time of the stop system)
• The A1 safety PLC must conform to PL requirements and to EN ISO 13849-1
• The Q1 and Q2 safety contactors must have linked contacts according to IEC 60947-5-2, Attachment L (“mirror contacts”)
• When a person is able to fully enter the hazardous area, guards must be installed in addition to a detection system, or restart
must only be possible after a separate restart which occurs after the guards have closed and ensured that no person remains in
the hazardous area, in line with risk analysis guidance
• A short circuit between conductors connected to 33-34 A1 and between conductors connected to 37-38 A1 and between
those connected to pins 1 and 2 of the drive must be prevented
• The signal paths must be physically separated
• Multi-strand cables connected to multi-pin connectors must terminate with a cable terminal or other appropriate device
• The test signal wiring of the two channels must be protected from short circuits to voltage sources; external voltage must
never be applied to the test signal, not even in the case of failure
• The safety system must be validated according to EN ISO 13949-2:2008
DR2020
MAR2-E-191
88