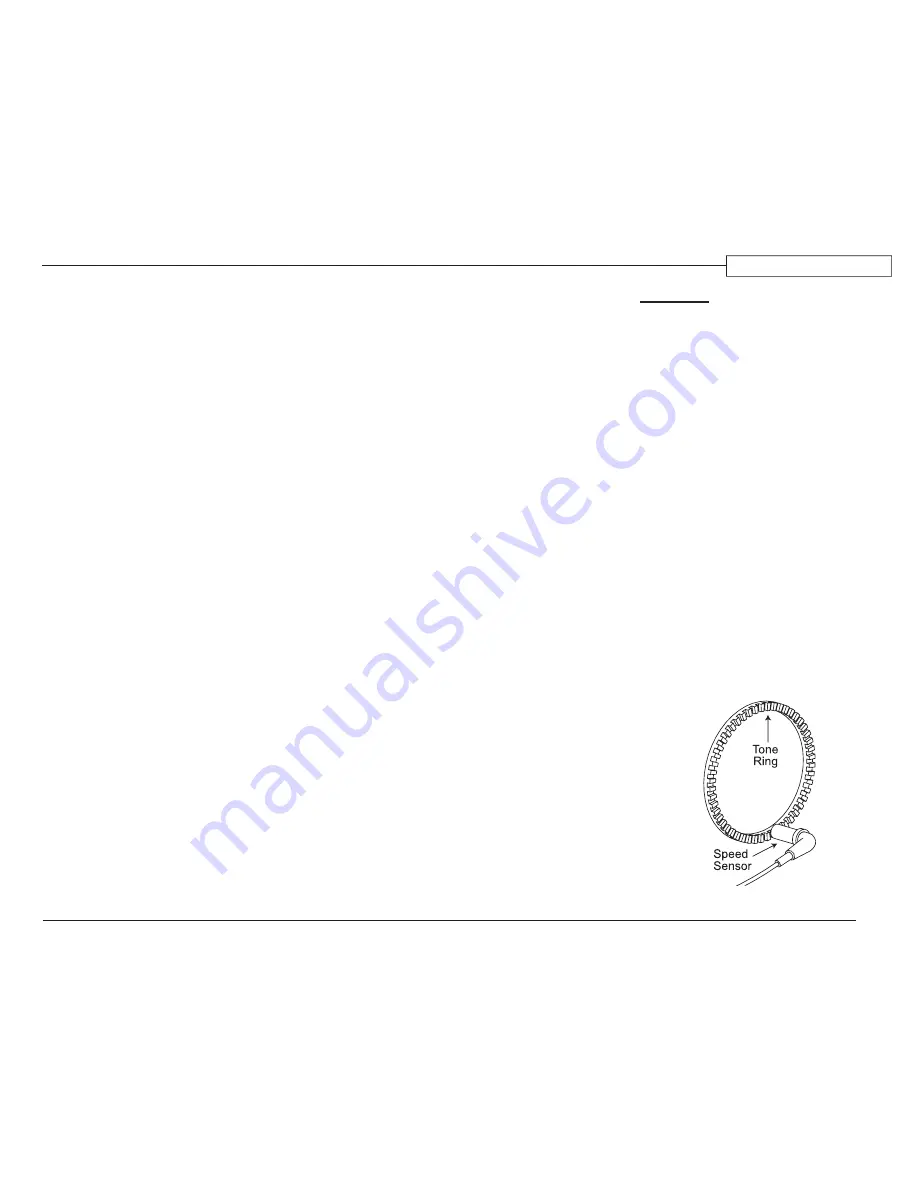
2 0 0 8 K n I G h t
chassIs InformatIon — 10
19
Another backup safety is the air system
separation of the front and rear brakes,
implemented by using two air tanks. One tank
is located in the front and the other is located
in the rear. This separation allows the front air
tank to operate the front brakes; the rear tank
operates the rear drive axle brakes. This tank
division gives reassurance in case one tank
experiences a failure of an accessory air item
allowing the compressed air to escape.
Accessory air items are other pneumatically
operated items such as the air horn, vacuum
generator, etc. The accessory air items operate
only when air tank pressures exceed 65 psi.
This is done with pressure protection valves.
Should an accessory air item fail, the pressure
protection valve (PPV) reserves the remaining
air pressure of 65 psi for braking. This will leave
the motorhome with one air tank fully charged
for safety backup.
The rear air tank also has a safety backup
- the safety inversion valve. The inversion
valve senses the absence of rear air tank
pressure. In this case the inversion valve
will allow the operator to make a modulated
spring brake application, made in conjunction
with the emergency spring brake relay valve.
The inversion valve allows the front air tank
pressure to recharge the rear brake chambers
after the modulated spring brake application
has been made.
This backup system implements
use of all the brakes, allowing the operator to
bring the motorhome a safe stop. In case of all
compressed air charge escaping from the front
air tank, the operator will still have full use of
the rear brakes.
aBS/atc SyStem (antI-lock BrakeS)
The motorhome is equipped with an anti-
lock braking system (ABS) and automatic
traction control system (ATC). The ABS system
monitors wheel rotation speeds by using a 100-
tooth magnetic tone ring mounted to the hub.
Revolving with the wheel, the magnetic tone
ring is polarized giving positive and negative
pulsations. A stationary sensor is mounted
adjacent to the tone ring to monitor magnetic
pulses. The pulses are monitored by the ABS
electronic control unit (ECU).
The ECU monitors all wheel sensors at the
rate of 100 times per second. The ECU controls
Pressure Modulator Valves. Pressure Modulator
Valves have two electric-over-air solenoids,
a hold solenoid and a release solenoid. The
modulator valves are open under normal
braking, allowing a straight through air signal
from the treadle valve to the brake chamber.
Should a wheel lose traction under a braking
application, the ECU will energize the hold
solenoid of the Pressure Modulator Valve to
interrupt the air signal from the treadle valve to
the brake chamber. The release solenoid vents
the existing air signal, at the brake chamber
to the atmosphere, allowing the skidding tire
to regain traction. Skidding tires have less
tractive efficiency. It is possible, under certain
conditions, to have the wheel(s) skid with a
normal functioning ABS system.
The ABS itself does not apply additional
braking power. The purpose of the ABS is to
limit wheel lock and decrease stopping distance.
Cautious driving practices and maintaining
adequate safe distance when following vehicles
is the key to safe vehicle operation.
WARNING
The ABS/ATC system is designed to
increase tire to road surface traction but
cannot overcome naturally occurring
laws of physics. The ABS/ATC system,
combined with safe driving practices,
will reduce the possibility of wheel skid
and loss of lateral stability.
ABS Component Function:
Speed sensors and tone rings on each
wheel monitor wheel rotation.
Each speed sensor communicates wheel
rotation pulses to the Electronic Control
Unit.
The ECU receives the speed sensor
signal pulses to calculate speed and
acceleration rates of each wheel.
Based on the speed sensor input, the
ECU detects impending wheel lock
and operates the ABS Modulator
Valves required for proper control. The
Modulator Valves are operated in the Air,
Release or Hold modes to regulate air
pressure to the brake chambers.
090307
Содержание 2008 Knight
Страница 12: ......
Страница 14: ......
Страница 16: ......
Страница 46: ...driving safety 2 42 2008 Knight Weighing Procedure Worksheet Example Worksheet 020255b conv...
Страница 47: ...2008 KNight 43 driving safety 2 Weight Record Sheet Actual Worksheet 020255b...
Страница 52: ...driving safety 2 48 2008 Knight Notes...
Страница 76: ...exterior interior care 3 72 2008 Knight Notes...
Страница 190: ...electrical systems chassis 9 186 2008 Knight engine no start flow chart...
Страница 233: ...2008 KNight chassis information 10 229 Notes...
Страница 237: ...2008 KNight chassis information 10 233 Battery Specification Charts...
Страница 246: ......