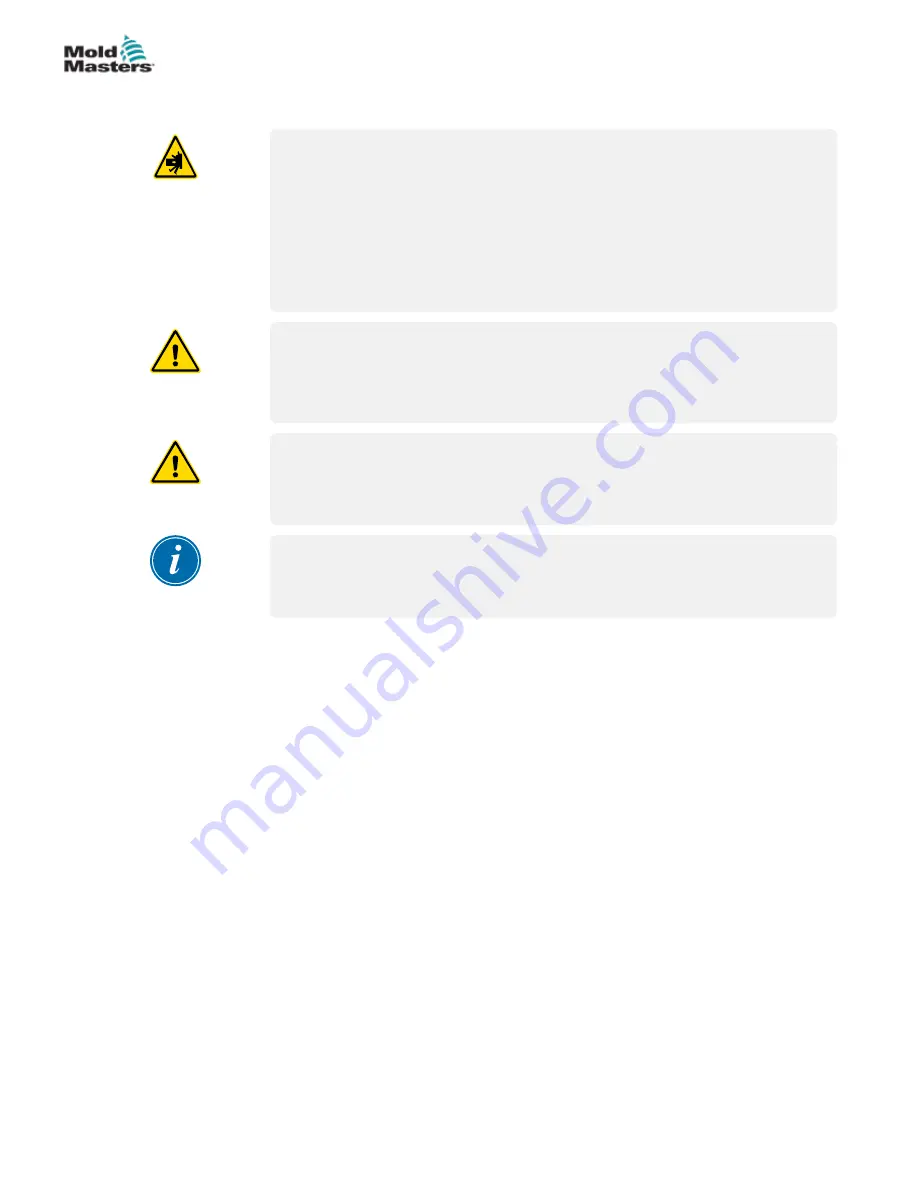
6.1 Attach E-Multi Injection Unit to the Mold /
Machine
WARNING - BODY CRUSH HAZARD
The end of the injection motor moves back 210 mm (8 in.) max stroke
during hold or recovery. A hazard may exist between the end of the injection
unit motor assembly and a nearby solid obstacle. Suitable safety guarding
must be installed by the integrator to prevent a crush hazard.
During installation of the E-Multi injection unit onto a mold, a crushing
hazard exists between the adapter plate and the mounting surface of the
mold.
WARNING - CUT HAZARD
For horizontally-mounted machines with a high centerline height, a person’s
head could hit the end of the injection unit presenting a cut hazard. Suitable
guarding / warning should be installed by integrator.
WARNING
The screws securing the adapter plate to the E-Multi injection unit and the
adapter plate to the Injection molding machine must be tightened to the
correct torque. See “Screw Torque Specifications” on page 9-1.
IMPORTANT
Please refer to the installation drawing supplied with unit for complete
information on services and connections.
1. Clean the molding machine and mold where the E-Multi injection unit will
be mounted. Any plastic residue on the manifold inlet must be removed
to ensure proper nozzle contact.
2. Install adapter plate onto E-Multi injection unit. See “Adapter Plate
Removal and Installation” on page 9-10.
3. Verify that E-Multi carriage is retracted to prevent bending the carriage
link.
4. Install the E-Multi injection unit horizontally or vertically as described
below
a) For vertical installations, lift the E-Multi injection unit into place above
the manifold inlet and install screws. Torque in a crosswise pattern.
b) For horizontal installations, move the E-Multi injection unit into place
beside the manifold inlet. Verify the stand is at the correct height and
install screws. Torque in a crosswise pattern. See “E-Multi Stands” on
6-2
E-Multi User Manual
INSTALLATION
© 2020 Mold-Masters (2007) Limited. All Rights Reserved.