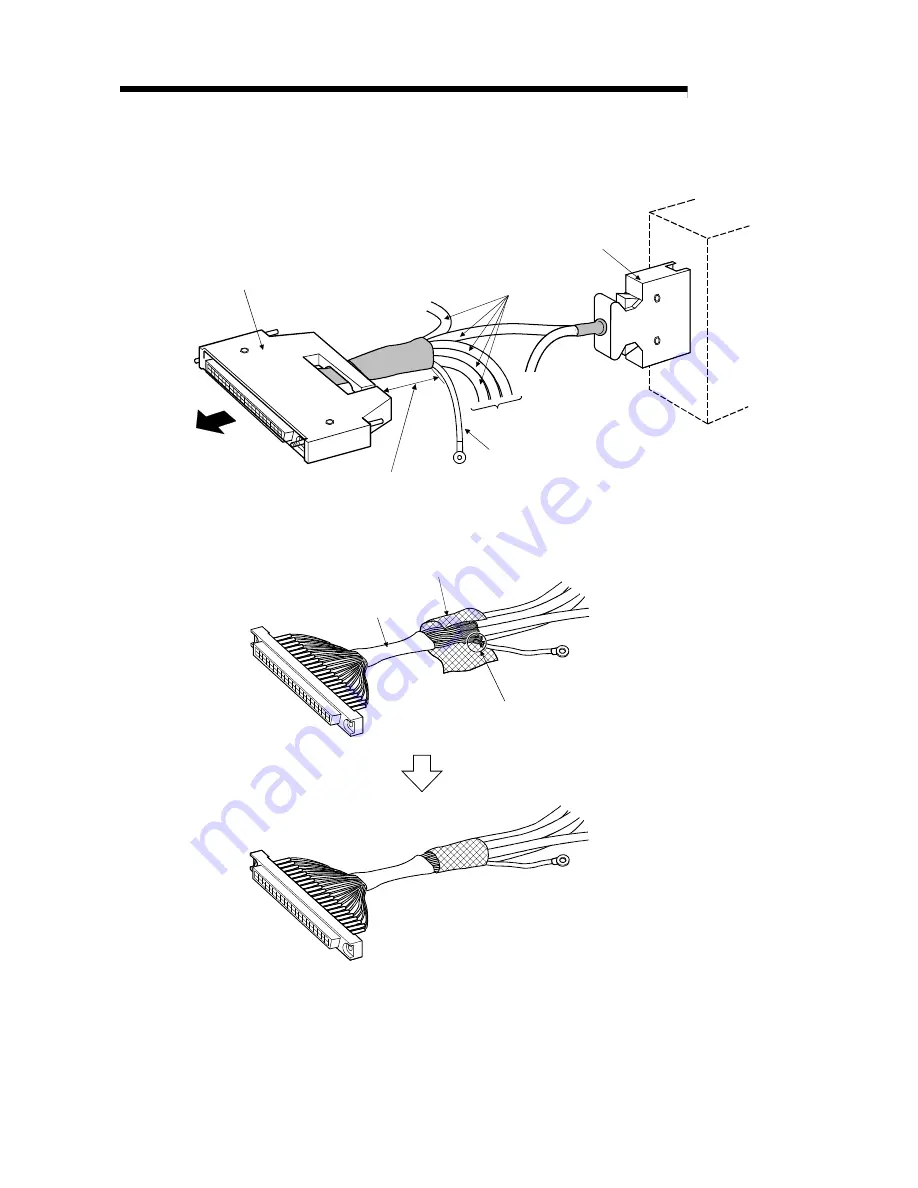
5 - 8 5 - 8
MELSEC-Q
5 SETUP AND PROCEDURES BEFORE OPERATION
[Wiring example using shielded cables]
The following are wiring examples for noise reduction.
To external
devices
Connector
Shielded
cable
Drive
unit
Connector
(A6CON1/A6CON2)
To drive units
Use the shortest posible ingth to
graound the 2mm or more FG wire.
(The shield must be grounded on
the QD70 side)
The length between the connector and the shielded
cable chould be the shortest possible.
To QD70
To external
device
2
[Processing example of shielded cables]
Coat the wire with
insulaing tape
Remove the coverring from all shielded cables and bind
the apperared shield with a conductive tape.
Solder the shield of any one of the
shielded cables to the FG wire.
Содержание GX Configurator-PT
Страница 13: ...MEMO SECTION 1...
Страница 127: ...7 20 7 20 MELSEC Q 7 SEQUENCE PROGRAM USED FOR POSITIONING CONTROL MEMO...
Страница 129: ...MEMO SECTION 2...
Страница 221: ...Index 5 Index 5 MEMO...