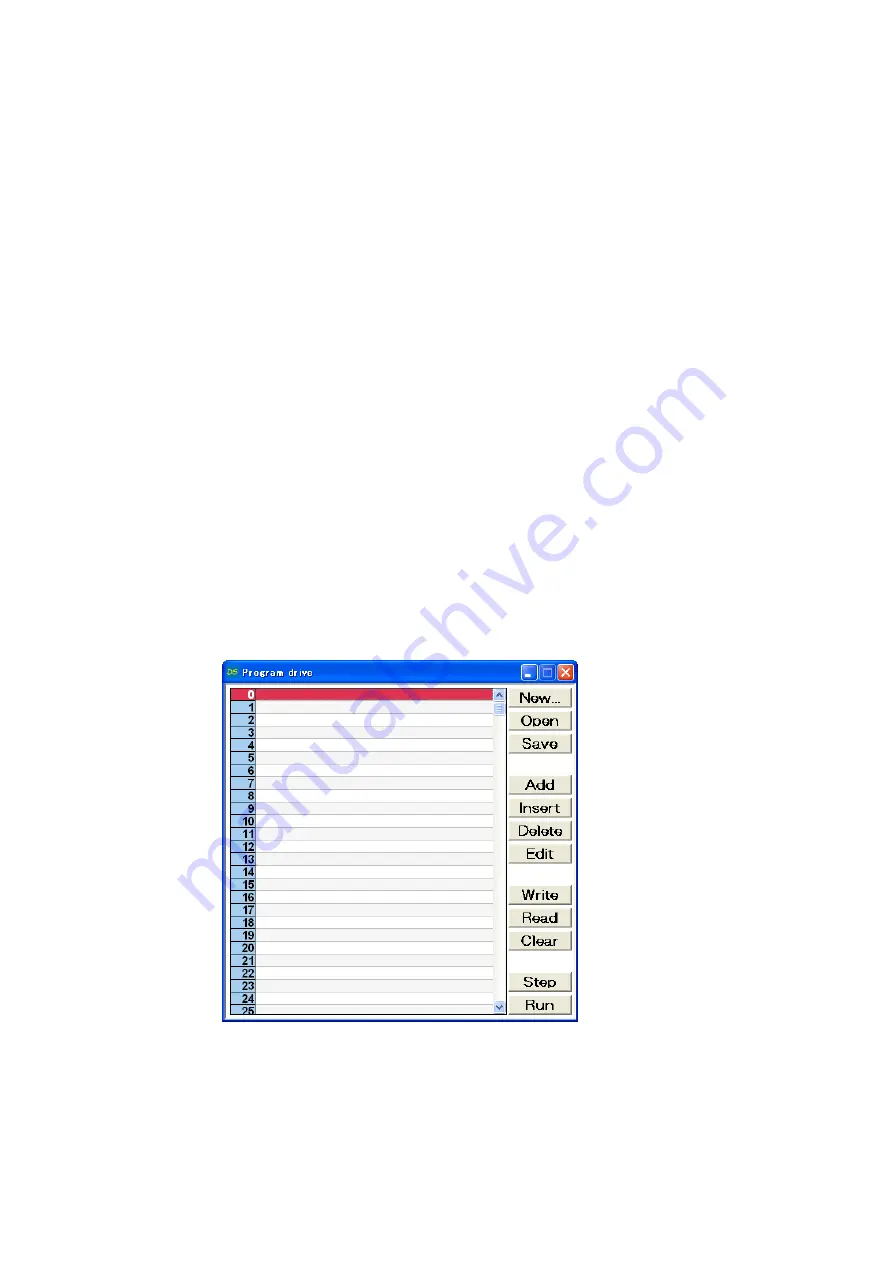
35
3) Connection
Connection of DS112
PC (DSCONTROL-WIN) is connected only when creating or editing program.
①
Connect USB connector to USB port in PC
(Connect RS232C to PC when using RS232C)
②
Connect X axis stage connector to X axis stage
③
Connect Y axis stage connector to Y axis stage
④
Connect control I/O connector to I/O unit in PLC
On control I/O,
P_BIT0~2:Select program #
P/T_START:Signal of movement to teaching point
STOP:Stop signal for all axes
PRG/TCH:Select mode (Start program / movement to teaching point)
※ P_BIT0~2: combined use for teaching point selection
4) Creating program
Creating [Origin return] of two axes.
①
Start DSCONTROL-WIN
②
Click
[Action]→[Program drive] on main menu.
Содержание DS102MS
Страница 166: ...166...