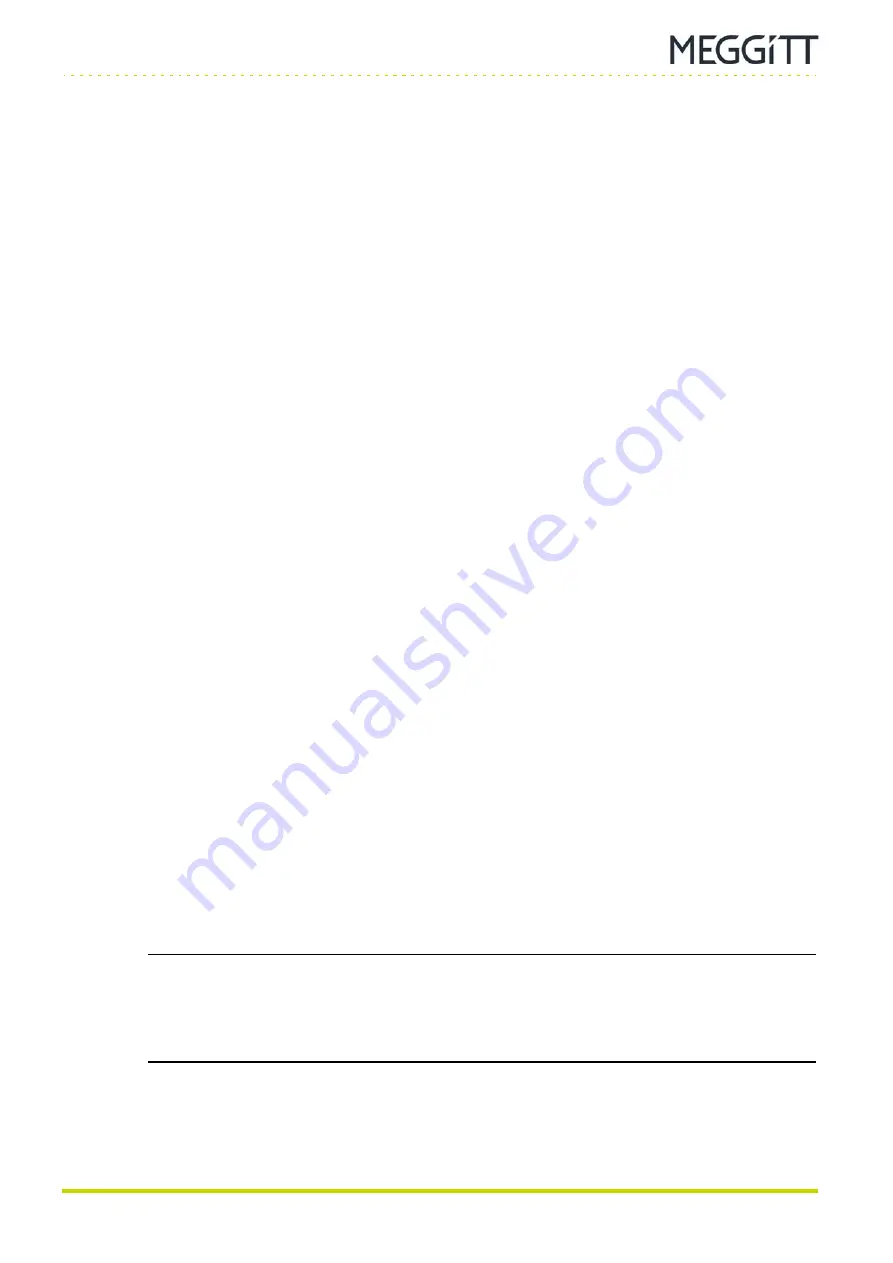
USER MANUAL
Document reference MAODS301/E
SpeedSys300 ODS301 overspeed detection system
Edition 4 - May 2022
1 - 4
System overview
INTRODUCTION TO THE SPEEDSYS300 ODS301 OVERSPEED DETECTION SYSTEM
1.1.2 SIL safety
The SpeedSys300 ODS301 overspeed detection system is certified as SIL 2 and SIL 3
capable “by design”. Accordingly, the SpeedSys300 ODS301 module includes advanced
self-monitoring and diagnostics (also known as built-in self-test (BIST)) to detect problems
with the complete system. More specifically, the SpeedSys300 ODS301 module’s
diagnostics can detect problems with the sensor / measurement chain, the cabling and the
module itself. If the module detects any problems that could prevent it from implementing the
configured safety function, the module will drive the safety relays – relay 1 and relay 2 – and
the analog output to their safe states (de-energised and “zero” respectively) in order to ensure
that the machine being monitored is always safe.
The SIL 2 design of the SpeedSys300 ODS301 module is SIL 3 capable when used in a
redundant 2oo3 architecture. To implement the 2oo3 voting logic required by SIL 3 safety
applications (and 1oo2 voting logic), the safety relay outputs from three ODS301 modules
can either be wired directly together or they can be connected to an external system such as
a safety PLC so that the required logic is evaluated before initiating a shutdown.
1.1.3 Safety related and non-safety related functionality
While the two safety relays – relay 1 and relay 2 – and analog output provide the safety
related outputs, other SpeedSys300 ODS301 module functionality and outputs provide
additional monitoring capability.
Two additional (non-safety) relays – relay 3 and relay 4 – and are available for alarm/status
use depending on the requirements of the application. For example, the additional relays can
be used to indicate when a measurement exceeds a non-critical limit or to communicate
module status information, as configured using the application software.
A digital frequency (speed) output is available providing a digital output equivalent to the
measured speed processed by the SpeedSys300 ODS301 module. This is typically used with
a simple panel-mounted display in order to have a local digital readout of the speed for the
machine being monitored.
A serial communications interface supporting Modbus RTU is available to share
SpeedSys300 ODS301 module information with external third-party systems such as a DCS
or PLC. The Modbus RTU interface is read only and cannot be used to change the
configuration or operation of the ODS301 module.
While the proof-test interval of the SpeedSys300 ODS301 module itself is typically 10 years
(depending on the application), a digital proof-test control input is available to effectively
bypass the module’s safety relays for test purposes. This supports the proof test of a
complete system containing an SpeedSys300 ODS301 module, for example, external
systems such as a safety PLC. The SpeedSys300 ODS301 module proof test forces the
module’s safety relays to open, in order to allow the safety chain that comes after the module
/ safety PLC to be verified.
NOTE:
During a proof test, the SpeedSys300 ODS301 module cannot provide its normal
machinery monitoring and protection functions. Accordingly, it is highly
recommended that proof tests are only performed in accordance with the operating
procedures for the machinery being monitored and that appropriate precautions
are taken at the control system level (such as DCS or PLC).
Finally, a binary (status) output is available to indicate various aspects of the status of the
system (sensor / measurement chain, cabling and ODS301 module itself). For example, the
result of the advanced self-monitoring and diagnostics (BIST), overspeed, underspeed
and/or acceleration can be assigned to this digital output (as they can be assigned to the
relays).
Содержание vibro-meter SpeedSys300 ODS301
Страница 118: ...THIS PAGE INTENTIONALLY LEFT BLANK...
Страница 126: ...THIS PAGE INTENTIONALLY LEFT BLANK...