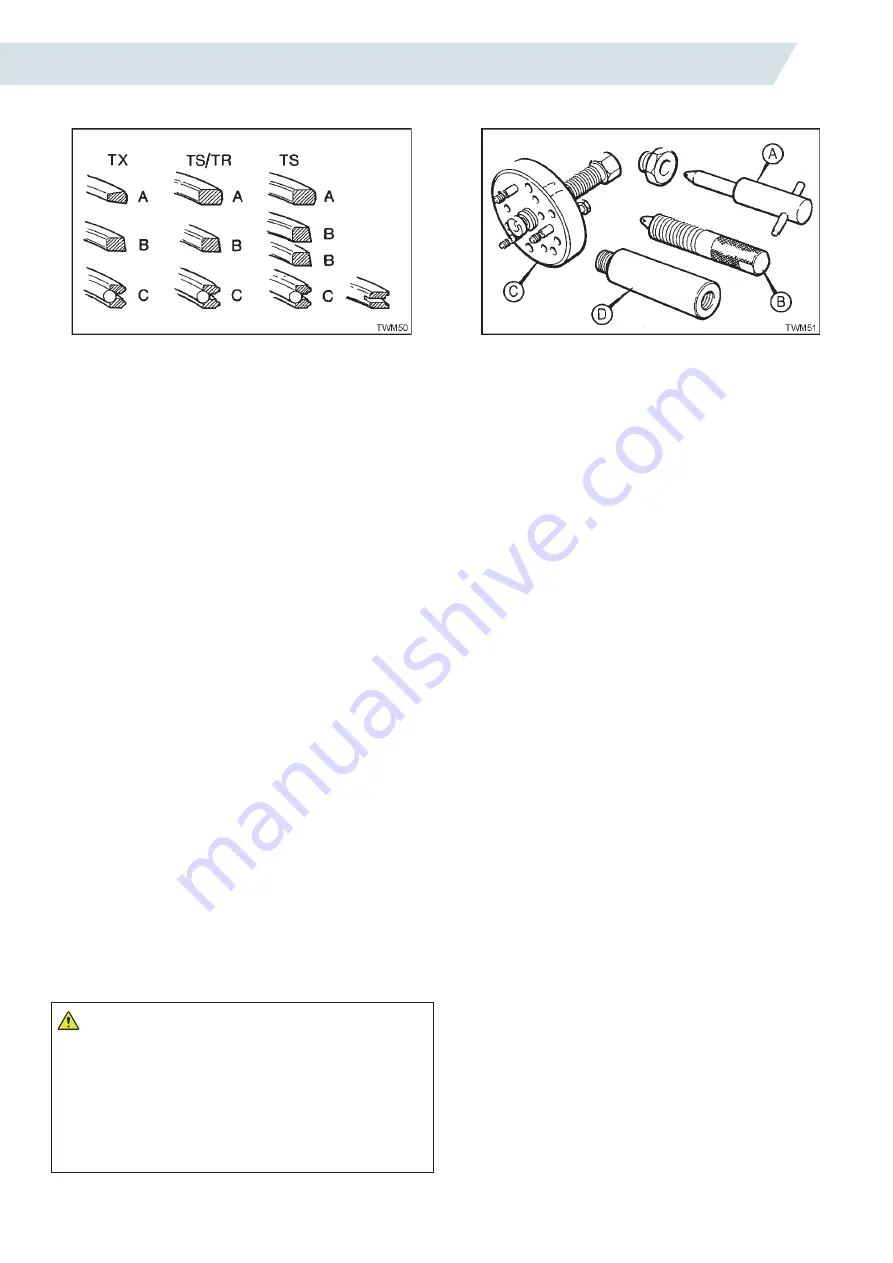
TS, TR, TX engines workshop manual
40
T SERIES ENGINES WORKSHOP MANUAL
43
Compression Ring
Two compression rings are fitted to the five ring
piston and one on the three ring piston. They
have a tapered face in contact with the barrel, one
surface on each is marked 'TOP' and the rings must
be fitted the correct way up with 'TOP' towards the
piston crown.
Oil Control Ring
One conformable type, with a spring expander, is
fitted above the gudgeon pin and a slotted scraper
ring is fitted below the gudgeon pin on five ring
pistons. On a three ring piston only one ring is fitted
above the gudgeon pin.
Removing a Piston
1.Remove the cylinder barrel together with the
piston.
2.Withdraw the piston from the barrel.
3.Release the circlip from one end of the gudgeon
pin.
4.Push out the gudgeon pin.
If the pin is tight, place the piston in hot water until
it can be removed; it may be necessary to protect
the hands.
5.Using a suitable piston ring expander remove the
piston rings.
Inspection and Servicing
a.Clean the piston, removing all traces of carbon
from the crown, ring grooves and oil holes.
b.Check all the piston rings in the cylinder barrel for
the correct gap clearance.
c.Clean the connecting rod and examine for
bending and twisting.
d.Examine the small end bush for wear.
e.If the big end has been dismantled because of
metal failure the oil passages in the crankshaft
must also be examined for obstruction and
fragments of metal.
Refitting a Piston
1.Fit the piston to the connecting rod.
On TS/TR engines ensure the wording
'CAMSHAFT SIDE' on the piston crown is the
same side as the identification marks on the
connecting rod big end.
2.Insert the gudgeon pin and replace the circlips.
3.Using a suitable piston ring expander replace the
piston rings in the order as shown below.
Figure 2.40.1 Piston Rings
A - Firing Ring
B - Compression Ring
C - Oil Control Ring
4.Distribute the piston ring gaps around the piston
circumference so that the gaps are not in line.
5.Lightly lubricate the piston and rings with new
engine oil.
6.Using a suitable piston ring clamp compress
the rings and fit the piston and connecting rod
assembly into the cylinder barrel.
2.41 THE FLYWHEEL
The flywheel rotates within the flywheel housing
and the type fitted depends on engine, speed,
application and build. All flywheels can be fitted
with ring gears for electric starting.
The TS/TR cooling air fan is fitted to the outside
face and is made of either polypropylene or cast
iron depending on the Build; the two types are not
interchangeable.
The flywheel is keyed on to the crankshaft and held
in position with a setscrew or nut. Early TS and
TR engines, up to the serial numbers given, were
fitted with a flywheel retaining setscrew and locking
washer. Later engines are fitted with a locking
washer and nut.
35 00630 TS1
36 00255 TR1
35 06716 TS2
36 00073 TR2
35 05963 TS3
36 00112 TR3
The retaining screw or nut should be torque loaded
to 475.0Nm (350.0lbf ft). All flywheels have tapped
holes for attaching couplings, shaft extensions,
pulleys etc.
The tolerance for bore and face run-out must be
within 0.25mm (0.010in) TIR.
Marks showing the firing point (FP) and the TDC
position for each cylinder can be viewed through
an aperture in the rear of the fanshroud.
The magnetic rotor for the TS and TR charge
windings is pressed into the rear face of the
flywheel.
Figure 2.40.1 Piston Rings
A - Firing Ring; B - Compression Ring; C - Oil Control Ring
4. Distribute the piston ring gaps around the piston circumference
so that the gaps are not in line.
5. Lightly lubricate the piston and rings with new engine oil.
6. Using a suitable piston ring clamp compress the rings and
fit the piston and connecting rod assembly into the cylinder
barrel.
2.41 The Flywheel
The flywheel rotates within the flywheel housing and the type
fitted depends on engine, speed, application and build. All
flywheels can be fitted with ring gears for electric starting.
The TS/TR cooling air fan is fitted to the outside face and is made
of either polypropylene or cast iron depending on the Build;
the two types are not interchangeable.
The flywheel is keyed on to the crankshaft and held in position
with a setscrew or nut. Early TS and TR engines, up to the serial
numbers given, were fitted with a flywheel retaining setscrew
and locking washer. Later engines are fitted with a locking
washer and nut.
35 00630 TS1
36 00255 TR1
35 06716 TS2
36 00073 TR2
35 05963 TS3
36 00112 TR3
The retaining screw or nut should be torque loaded to 475.0Nm
(350.0lbf ft). All flywheels have tapped holes for attaching
couplings, shaft extensions, pulleys etc.
The tolerance for bore and face run-out must be within 0.25mm
(0.010in) TIR.
Marks showing the firing point (FP) and the TDC position for
each cylinder can be viewed through an aperture in the rear
of the fanshroud.
The magnetic rotor for the TS and TR charge windings is pressed
into the rear face of the flywheel.
WARNING
The flywheel, without gear ring or fan, weighs in excess
of 54kg (1191bs) therefore it is important to bear this
point in mind when removing, handling or replacing it.
To prevent damaging the TS or TR stator of the flywheel
mounted charge windings the free length of studs or
bolts entering the flywheel must not exceed 20.0mm
(0.79in).
T SERIES ENGINES WORKSHOP MANUAL
44
WARNING
The flywheel, without gear ring or fan, weighs in
excess of 54kg (1191bs) therefore it is important
to bear this point in mind when removing,
handling or replacing it. To prevent damaging
the TS or TR stator of the flywheel mounted
charge windings the free length of studs or bolts
entering the flywheel must not exceed 20.0mm
(0.79in).
Figure 2.41.1 Flywheel Tools:
A - Early Locking Tool
B - Current Locking Tool
C - Puller
D - Mandrel
Flywheel Removal
1.Remove the starter motor.
2.Fit the flywheel locking tool into the tapped hole
in the fanshroud.
3.If the flywheel locking tool is not available wedge
the crankshaft with a suitable piece of wood to
prevent it turning.
4.Slacken the flywheel retaining screw or nut two
turns with a 65mm socket spanner.
5.Fit the flywheel puller tool by screwing three bolts
through the 'B' holes into the flywheel.
6.Turn the tool centre bolt sufficiently to loosen
the flywheel.
7.Remove the puller and locking tools.
8.Remove the flywheel screw or nut and fit the
correct flywheel mandrel to prevent damaging
the stator and for personal safety.
9.Support the flywheel at all times and keeping it
square, slide it over the mandrel and lift it off.
10.Remove the Woodruff key.
Refitting the Flywheel
The shaft and the bore of the flywheel must be
perfectly clean and should be smeared with clean
lubricating oil before assembly.
1.Fit a new Woodruff key.
2.Fit the correct flywheel mandrel to prevent
damaging stator and for personal safety.
3.Support the flywheel at all times and keeping
it square, slide it over the mandrel and into the
fanshroud.
Check that the key has remained in position in
the shaft.
4.Remove the mandrel.
5.Fit a new tabwasher and replace the setscrew/
nut.
6.Either fit the flywheel locking tool or wedge
the crankshaft with a suitable piece of wood to
prevent it turning.
7.Torque the retaining screw or nut to 475.0Nm
(350.0lbf ft).
8.Remove the locking tool.
2.42 THE FANSHROUD - TS/TR
An aluminium fanshroud is fitted to all engines
except Build 16 which has one of sheet metal.
Removing the Fanshroud
1.Remove the flywheel.
2.Remove the two nuts and then remove the
rectifier/regulator cover.
3.Carefully noting the position of the electrical
cables, disconnect all four cables.
4.Remove the two nuts, washers and distance
pieces and remove the rectifier/regulator unit
from the fanshroud.
The unit will be fitted to either, the manifold side of
the shroud or above the starter motor.
5.Remove the cable clip securing the cable inside
the fanshroud.
6.Remove the six screws securing the stator and
remove it, gently easing the cable through the
fanshroud.
7.Remove the two bolts that are fitted through the
lower end of the fanshroud securing it to the
sump.
8.Remove the self-lock bolts.
a.On older engines ease back the tab washers
and remove the bolts.
9.Lift off the housing.
Refitting the Fanshroud
Refitting is carried out in the reverse order and it is
recommended that new tabwashers are fitted and
correctly locked after the bolts have been torque
loaded to 43.5Nm (32.0lbf ft).
The tabwashers and bolts can be replaced with
the current self-locking setscrews which must be
torque loaded to 88.0Nm (65.0lbf ft).
Figure 2.41.1 Flywheel Tools:
A - Early Locking Tool; B - Current Locking Tool; C - Puller; D - Mandrel
Flywheel Removal
1. Remove the starter motor.
2. Fit the flywheel locking tool into the tapped hole in the
fanshroud.
3. If the flywheel locking tool is not available wedge the
crankshaft with a suitable piece of wood to prevent it
turning.
4. Slacken the flywheel retaining screw or nut two turns with a
65mm socket spanner.
5. Fit the flywheel puller tool by screwing three bolts through
the 'B' holes into the flywheel.
6. Turn the tool centre bolt sufficiently to loosen the flywheel.
7. Remove the puller and locking tools.
8. Remove the flywheel screw or nut and fit the correct flywheel
mandrel to prevent damaging the stator and for personal
safety.
9. Support the flywheel at all times and keeping it square, slide
it over the mandrel and lift it off.
10. Remove the Woodruff key.
Refitting the Flywheel
The shaft and the bore of the flywheel must be perfectly
clean and should be smeared with clean lubricating oil before
assembly.
1. Fit a new Woodruff key.
2. Fit the correct flywheel mandrel to prevent damaging stator
and for personal safety.
3. Support the flywheel at all times and keeping it square, slide
it over the mandrel and into the fanshroud.
Check that the key has remained in position in the shaft.
4. Remove the mandrel.
5. Fit a new tabwasher and replace the setscrew/nut.
6. Either fit the flywheel locking tool or wedge the crankshaft
with a suitable piece of wood to prevent it turning.
7. Torque the retaining screw or nut to 475.0Nm (350.0lbf ft).
8. Remove the locking tool.
2.42 The Fanshroud - TS/TR
An aluminium fanshroud is fitted to all engines except Build 16
which has one of sheet metal.
Содержание TS/TR1
Страница 1: ...P027 08270 edition 8 April 2021 TS TR TX Engines Workshop Manual T SERIES ...
Страница 80: ...TS TR TX engines workshop manual 80 T SERIES ENGINES WORKSHOP MANUAL 90 ct ical Wiring i g ...
Страница 81: ...TS TR TX engines workshop manual 81 T SERIES ENGINES WORKSHOP MANUAL 91 Elect i al Wiring Diagram ...
Страница 82: ...TS TR TX engines workshop manual 82 T SERIES ENGINES WORKSHOP MANUAL 92 ctr ca Wi ing Diagrams ...
Страница 83: ...TS TR TX engines workshop manual 83 T SERIES ENGINES WORKSHOP MANUAL 93 Electrical Wiring iagram ...
Страница 84: ...TS TR TX engines workshop manual 84 T SERIES ENGINES WORKSHOP MANUAL 94 ect ica Wiring Diagrams ...
Страница 85: ...TS TR TX engines workshop manual 85 T SERIES ENGINES WORKSHOP MANUAL 95 ...
Страница 99: ...TS TR TX engines workshop manual 99 ...