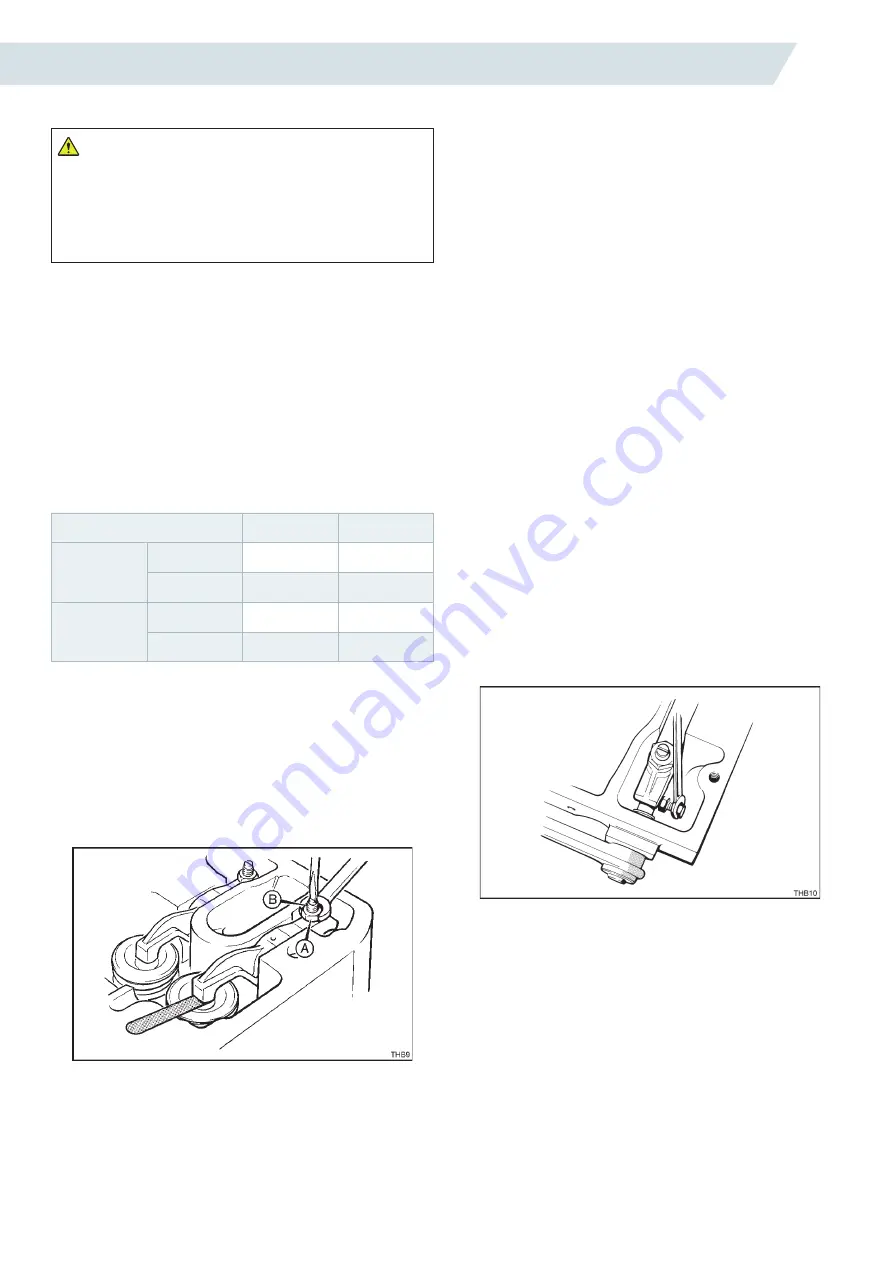
TS, TR, TX engines workshop manual
20
WARNING
The valve guide will be damaged if the mandrel is
adjusted too much when it is located in the guide and
care must be taken to ensure an even, gentle downward
pressure is applied when using the cutter to prevent the
removal of too much metal.
2.18 Valve Clearance
The valve clearance must be measured and adjusted when the
engine is cold. It is important that the clearances are maintained
correct to prevent serious damage to the valve gear. With new
engines, or engines which have just been overhauled, the valve
gear beds down rapidly during the first 500 hours running and
it is essential that the clearance is checked every 25 hours until
it is found that the clearances remain constant. The periods
between adjustments may then be increased to 1000 hours.
Adjusting the Valve Clearance
GO
NOT GO
TS/TR
mm
0.15
0.20
in
0.006
0.008
TX
mm
0.10
0.15
in
0.004
0.006
1. Ensure the decompressor is clear of the exhaust valve
rocker.
2. With the cylinder head cover removed, turn the engine until
the relevant piston is at the TDC position on the firing stroke
- both valves will be closed.
3. Hold the adjusting screw (A) with a screwdriver and slacken
the locknut (B).
Turn the screw until the correct clearance has been
obtained.
T SERIES ENGINES WORKSHOP MANUAL
21
pressing in the inserts, at ambient temperature the
head should be heated to 100°-150°C (212°-302°F)
for a minimum of 45 minutes and the insert chilled
to -65° to -75°C (-85° to -103°F) for a minimum of
30 minutes.
The width of the TS/TR seatings must be:
Inlet: 1.65-2.29mm (0.065-0.090in).
Exhaust: 1.35-1.78mm (0.053-0.070in).
If necessary metal must be ground or cut from the
top of the insert or recess. The valves are pre-
finished and no lapping or further processing is
required.
All seats are precision ground to allow the valves to
lay below the combustion surface of the head.
Up to the TS/TR serial numbers shown the
measurements were:
Inlet valves: 1.02-1.27mm (0.040-0.050in).
Exhaust valves: 0.89-1.14mm (0.035-0.045in).
36 00199 TS1 36 00025 TR1
36 00480 TS2 36 00020 TR2
36 00307 TS3 36 00043 TR3
On later TS/TR engines the measurements are:
Inlet valves: 0.63-0.94mm (0.025-0.037in).
Exhaust valves: 0.51-0.82mm (0.020-0.032in).
On TX engines the measurement for both valves is
1.020-1.550mm (0.040-0.061in).
Valve Recess and Seat Cutting
1.Fit the correct adjustable mandrel (A) into the
valve guide and turn the adjuster until the flutes
just bind onto the guide.
2.Select the necessary cutting tool (B) and
assemble it to the handle (C).
Figure 2.17.1 Recess and Seat Cutting Tool
3.Place the cutter over the mandrel and adjust the
three individual blades by using the Allen Key (E).
4.Rotate the tool in a clockwise direction until the
valve seat or recess finish is satisfactory.
WARNING
The valve guide will be damaged if the mandrel
is adjusted too much when it is located in the
guide and care must be taken to ensure an
even, gentle downward pressure is applied
when using the cutter to prevent the removal of
too much metal.
2.18 VALVE CLEARANCE
The valve clearance must be measured and
adjusted when the engine is cold. It is important
that the clearances are maintained correct to
prevent serious damage to the valve gear. With
new engines, or engines which have just been
overhauled, the valve gear beds down rapidly
during the first 500 hours running and it is essential
that the clearance is checked every 25 hours until
it is found that the clearances remain constant.
The periods between adjustments may then be
increased to 1000 hours.
Adjusting the Valve Clearance
GO
NOT GO
TS/TR
mm
0.15
0.20
in
0.006
0.008
TX
mm
0.10
0.15
in
0.004
0.006
1.Ensure the decompressor is clear of the exhaust
valve rocker.
2.With the cylinder head cover removed, turn the
engine until the relevant piston is at the TDC
position on the firing stroke - both valves will be
closed.
3.Hold the adjusting screw (A) with a screwdriver
and slacken the locknut (B).
Turn the screw until the correct clearance has
been obtained.
Figure 2.18.1 Valve Clearance
Figure 2.18.1 Valve Clearance
4. Torque the locknut, while continuing to hold the adjusting
screw, to 21.0Nm (15.5lbf ft).
5. Re-check to ensure the clearance is correct.
6. Repeat the procedure for both valves in all cylinders.
2.19 The Decompressor
The decompressor is fitted to the exhaust valve on some
engines. When the cylinder head cover is being replaced care
must be taken to ensure the lever is vertical between the two
stops.
The decompressor lever is spring loaded towards the cylinder
head and is located by a plain washer and a split pin or circlip
fitted through the decompressor shaft. A seal, fitted on the
outside of the cylinder head, prevents oil seepage along the
spindle. On engine builds not fitted with a decompressor the
drilling in the cylinder head is plugged with a dowel.
Removing the Decompressor
Remove the cylinder head cover.
Remove the split pin or circlip, washer, spring and adjusting
screw.
Withdraw the decompressor lever from the cylinder head.
Decompressor Adjustment
This adjustment should only be made when the valve clearance
is correctly adjusted.
After the decompressor has been set on TX engines the
maximum valve lift must not exceed 0.76mm (0.030in).
1. Remove the cylinder head cover.
2. Turn the engine until the piston is at TDC. firing stroke, for
the cylinder being worked on.
TS and TR Engines
T SERIES ENGINES WORKSHOP MANUAL
22
4.Torque the locknut, while continuing to hold the
adjusting screw, to 21.0Nm (15.5lbf ft).
5.Re-check to ensure the clearance is correct.
6.Repeat the procedure for both valves in all
cylinders.
2.19 THE DECOMPRESSOR
The decompressor is fitted to the exhaust valve on
some engines. When the cylinder head cover is
being replaced care must be taken to ensure the
lever is vertical between the two stops.
The decompressor lever is spring loaded towards
the cylinder head and is located by a plain
washer and a split pin or circlip fitted through the
decompressor shaft. A seal, fitted on the outside
of the cylinder head, prevents oil seepage along
the spindle. On engine builds not fitted with a
decompressor the drilling in the cylinder head is
plugged with a dowel.
Removing the Decompressor
Remove the cylinder head cover.
Remove the split pin or circlip, washer, spring and
adjusting screw.
Withdraw the decompressor lever from the cylinder
head.
Decompressor Adjustment
This adjustment should only be made when the
valve clearance is correctly adjusted.
After the decompressor has been set on TX
engines the maximum valve lift must not exceed
0.76mm (0.030in).
1.Remove the cylinder head cover.
2.Turn the engine until the piston is at TDC. firing
stroke, for the cylinder being worked on.
TS and TR Engines
Figure 2.19.1 Decompressor Lever
3.Slacken the locknut (A) and adjust the screw
(B) until it just touches the exhaust valve rocker
when the lever is vertical.
4.Turn the screw half a turn clockwise so that it
travels towards the rocker.
5.Tighten the locknut whilst restraining the adjusting
screw.
TX Engines
6.Place the decompressor lever in the vertical
position.
7.Slacken the decompressor pin locknut and adjust
the pin to take up the valve clearance.
8.Turn the pin a further half a turn and tighten the
locknut.
All Engines
9.Replace the rocker cover taking care to ensure
the decompressor lever is vertical.
2.20 THE CRANKSHAFT PULLEY - TX
The pulley is secured by a torque loaded left hand
thread nut.
Removing the Pulley
1.Slacken the alternator mounting bolts and move
the alternator as far as it will go towards the
crankcase.
2Remove the drive belt.
3.Fit the flywheel locking tool into the tapped hole
in the flywheel housing - check that the flywheel
will not turn.
If the flywheel locking tool is not available wedge
the crankshaft with a suitable piece of wood to
prevent it turning.
The pulley is secured by a torque loaded left
hand thread nut.
Figure 2.20.1 Flywheel Locking Tool
4.Remove the pulley retaining nut by turning it
clockwise.
5.Pull off the crankshaft pulley.
6.Remove the locking tool.
Refitting the Pulley
1.Fit the flywheel locking tool into the tapped hole
in the flywheel housing - check that the flywheel
Figure 2.19.1 Decompressor Lever
3. Slacken the locknut (A) and adjust the screw (B) until it just
touches the exhaust valve rocker when the lever is vertical.
4. Turn the screw half a turn clockwise so that it travels towards
the rocker.
5. Tighten the locknut whilst restraining the adjusting screw.
TX Engines
6. Place the decompressor lever in the vertical position.
7. Slacken the decompressor pin locknut and adjust the pin to
take up the valve clearance.
8. Turn the pin a further half a turn and tighten the locknut.
Содержание TS/TR1
Страница 1: ...P027 08270 edition 8 April 2021 TS TR TX Engines Workshop Manual T SERIES ...
Страница 80: ...TS TR TX engines workshop manual 80 T SERIES ENGINES WORKSHOP MANUAL 90 ct ical Wiring i g ...
Страница 81: ...TS TR TX engines workshop manual 81 T SERIES ENGINES WORKSHOP MANUAL 91 Elect i al Wiring Diagram ...
Страница 82: ...TS TR TX engines workshop manual 82 T SERIES ENGINES WORKSHOP MANUAL 92 ctr ca Wi ing Diagrams ...
Страница 83: ...TS TR TX engines workshop manual 83 T SERIES ENGINES WORKSHOP MANUAL 93 Electrical Wiring iagram ...
Страница 84: ...TS TR TX engines workshop manual 84 T SERIES ENGINES WORKSHOP MANUAL 94 ect ica Wiring Diagrams ...
Страница 85: ...TS TR TX engines workshop manual 85 T SERIES ENGINES WORKSHOP MANUAL 95 ...
Страница 99: ...TS TR TX engines workshop manual 99 ...